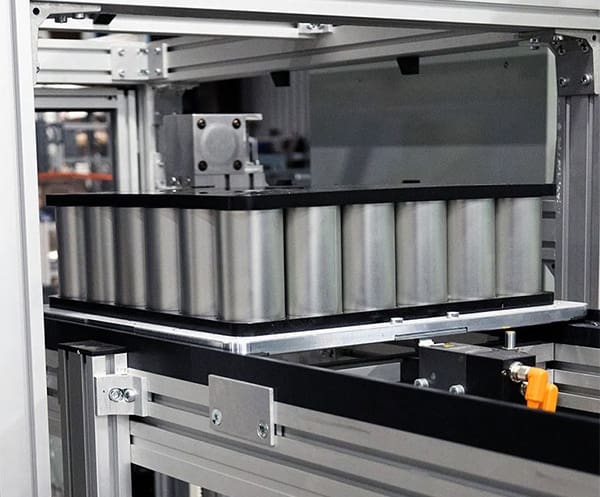
The production of batteries for the electric vehicle industry is growing and changing rapidly, based on the expansion of knowledge within the industry. And that is why it is so important to ensure the conveyors that are sourced for your ev-battery production line are not only up for today’s challenges, but tomorrow’s challenges as well.
In this article we will explore several EV battery production challenges that can be met with material handling systems; as well as provide you with additional information via case studies, example videos, a white paper and even two different tools to help you select the right conveyor system for your project. So let’s get started.
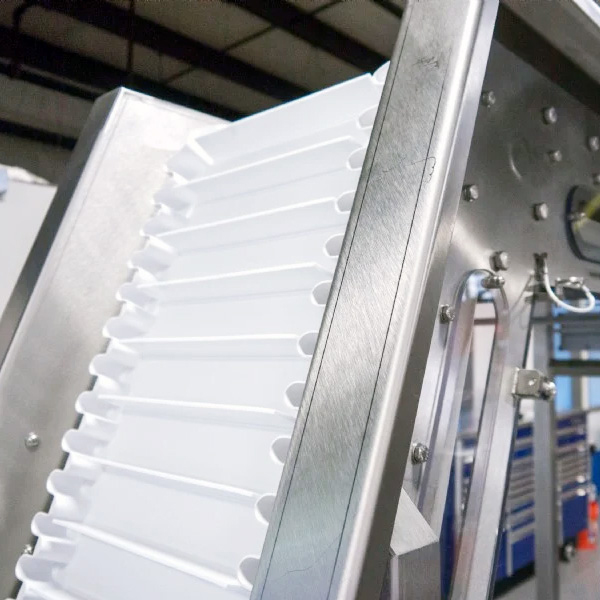
If we begin by looking at the raw materials and subcomponents that are necessary in battery manufacturing, we are met with some of the very first material handling challenges. Raw materials such as lithium, nickel, cobalt, manganese, and graphite can be conveyed in powered form or in “play-doh” like cylinders. Because of the nature of these materials, it is critical to use a continuous belt, often with sidewalls adhered to it. These conveyor components will help keep the raw materials from collecting under the belt’s surface thus reducing the efficiency of the conveyor. The use of positive drive conveyors is also routine in these applications as this will continue to provide the conveyor with the necessary belt engagement to move the belt forward should material does get lodged under the belt.
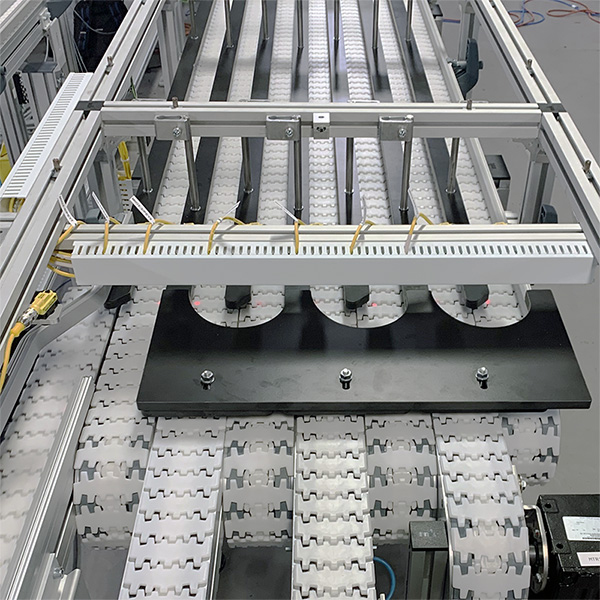
Skipping ahead in the production process to round battery cells; specifically, once the round batteries are complete. These batteries now need to be stored (accumulated) and then inspected – on all sides. When inspecting the top and the bottom of the round battery cell it is necessary to convey the battery by its edges – allowing for clear lines of site vertically on the battery. In these instances, wedge or gripper, style conveyors are utilized. But they are not the only solution. Check out these two Case Studies to learn more.
- Wedge or Gripper Conveyors for Battery Cleaning and Inspection
- Timing Belt and Linear Motion Solutions for Battery Inspection, using trays
Moving along further ahead to battery pack production, the material handling challenge has shifted from smaller parts to large (and heavy) battery packs. Due to the size and weight of these items, they are based conveyed on pallet-handling systems. Additionally, the use of pallet-handling systems allows for battery packs to change elevations and travel around corners. In some instances, the battery packs themselves can act like the pallet, but conveying the battery pack on a pallet offers additional functionality such as precisely locating the battery and even rotating it.
Check out this Whitepaper on how pallet-handling conveyors can help streamline and optimize manufacturing processes of all sorts. Looking for a quick overview? Then check out this Infographic.
If you are unsure of what you need in a conveyor system mk offers two tools that can assist you in that. The first is a simple Infographic that provides a step-by-step guide to understanding what needs to be known to configure a conveyor system. Already know what you need in a conveyor? Then try mk’s Conveyor Product Finder. This is an online tool that will help you select the best conveyor for your application based on known parameters. Try it HERE.
Automotive Battery Conveyor System from mk North America, Inc. on Vimeo.