When it comes to electrical devices, there are two things at the forefront of every consumer’s mind: how long will my battery last, and how long will it take me to charge it? This mentality goes double for EVs. A lot of attention is being put into extending EV battery range, but decreasing EV charging time is another useful way to combat the perennial problem of range anxiety.
Faster charging means higher power, and equipment manufacturers are already preparing for the future charging needs that industry observers believe are just around the corner. One company working to enable higher power is HUBER+SUHNER, which started looking into fast charging solutions when car manufacturers turned to the company for its connectivity experience.
Go big or go cold
To build a faster charging cable, there are two options. The first is simply to increase the size of the cable by increasing the cross-sectional area of copper wire. The bigger this area, the more current the cable can handle without overheating. Unfortunately, for the 400 or so amps of current required for next-gen fast charging, you’d need a cross-sectional area of 180 mm2 or more, which is simply too big and unwieldy for consumer applications.
The second option for a faster charging cable avoids the need to increase the cable size by instead managing the temperature of the copper wire at high currents. To do this, it’s necessary to make a cable with a built-in cooling system.
HUBER+SUHNER’s solution, the RADOX HPC High Power Charging System, supports up to 500 amps and 1,000 volts, for a total of 500 kilowatts. Even with this high power, because of its built-in cooling system, the RADOX has a cross-sectional area of only 25 mm2.
The RADOX HPC
To keep the cable cool during high-power charging, RADOX uses a non-conductive coolant combined with temperature sensors placed throughout the system.
“We start cooling down the contacts at the connector,” HUBER+SUHNER Market Manager Max Göldi told Charged. “And then the cooling liquid goes back directly onto the power lines back to the charging station. In the charging station we have a small container with a pump. So the coolant is just pushed around this circle.”
“The coolant itself is cooled with a ventilating system or heat exchanger at the option of the customer,” says Göldi. “The heat exchanger needs a cooling circuit with a central cooling unit and is only used for bigger charge parks.”
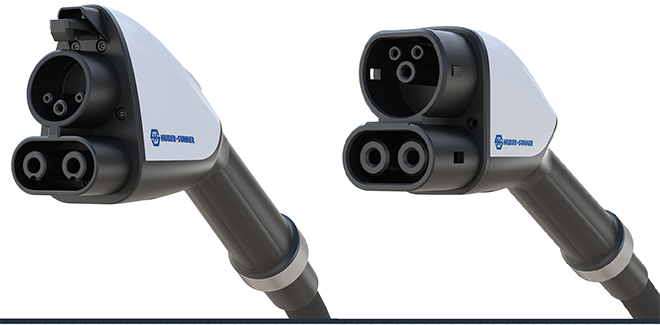
Temperature sensors are placed throughout the cable to ensure that no part of it becomes dangerously hot. This is especially important for the handle and the outside of the cable, which can come into direct contact with human operators.
“There are sensors on the pins at the connector, there’s sensors on the cooling, there’s sensors on the jacket material,” says Göldi. “The standards organizations are setting some [temperature] limitation guidelines. The handle and the cable cannot exceed a certain temperature, so that it’s no risk to use in daily life.”
Though the official standards have not been enacted yet, a commonly sought power rating for fast charging cables is 400 amps and 1,000 volts DC for 400 kilowatts of power. The RADOX system meets and exceeds these figures, as it’s been tested for use up to 500 kilowatts.
Preparing for the future of EVs
Even though the EVs available today aren’t equipped to handle RADOX’s high power levels, HUBER+SUHNER and other EVSE manufacturers recognize the need to plant seeds for the future.
“The target is to provide the car industry a corridor so they can charge their cars up to 500 kilowatts in the future,” says Göldi. “So that’s the idea behind why people are already starting to put high-power charging systems on American highways and important roads. And the same thing in Europe, just a couple months behind.”
The HUBER+SUHNER RADOX HPC system was approved by Intertek according to UL and IEC standards in April. The company now plans to sell the system – connectors, conductivity, cooling, and all – to charging station manufacturers.
“We provide the cooling system, but the control and the safety and surveillance features are done by the charging manufacturer,” said Göldi.
Göldi presented a prototype of the RADOX system at the 2017 Electric and Hybrid Vehicle Technology Expo Europe. At this year’s expo, he’s excited to be able to show off the finished product. “Last year we announced it, this year we can show where we’re standing – that is, a real, operational, serial product.”
This article originally appeared in Charged Issue 37 – May/June 2018 – Subscribe now.