One EV, a thousand applications
- Commercial vehicles, which are required in thousands of different varieties, are typically built under a model in which OEMs provide a basic chassis, and upfitters add the specialized bodies and equipment. This model has existed for many years in the on-road market, but Dannar is now bringing it to the world of off-road equipment.
- Electric off-road equipment offers a long list of advantages over legacy diesel equipment: lower fueling and maintenance costs; lack of idling; quiet, vibration-free operation; and less wear and tear on hydraulic components.
- Dannar’s vehicles are compatible with thousands of attachments made by trusted brands for diesel equipment. These can be switched out quickly and easily, so the same vehicle can serve more than one application.
- Dannar’s vehicles can also serve as Mobile Power Stations, providing charging for other EVs in the field.
Q&A with CEO Gary Dannar
Different buyers need (or want) different vehicles—that’s why most consumer automakers offer a range of a dozen or so models, from practical family cars to sleek sports cars to hulking pickup trucks. But in the commercial vehicle sphere, this wouldn’t be good enough—different markets demand not dozens of different vehicle types, but thousands. Some of these vehicles, often called vocational trucks, are designed for incredibly specialized applications (think of a cement mixer, a street cleaner or an airport de-icing truck), and it wouldn’t be economically efficient for an OEM to offer enough dedicated models to address them all. Instead, they build generic chassis/cab combinations, and leave it to other companies (called upfitters) to build specialized bodies, some of them custom-designed for specific customers.
When it comes to on-road commercial vehicles, this has been the model for decades. However, in the off-road market, OEMs tend to offer an array of purpose-built vehicles (or equipment—the distinction between the two is sometimes fluid). Some of these can be fitted with a wide array of interchangeable attachments (e.g. a tractor can power a mower, a loader, a tiller, etc.) but others are pretty much built to do one set of jobs (e.g. a loader, a digger or a backhoe).
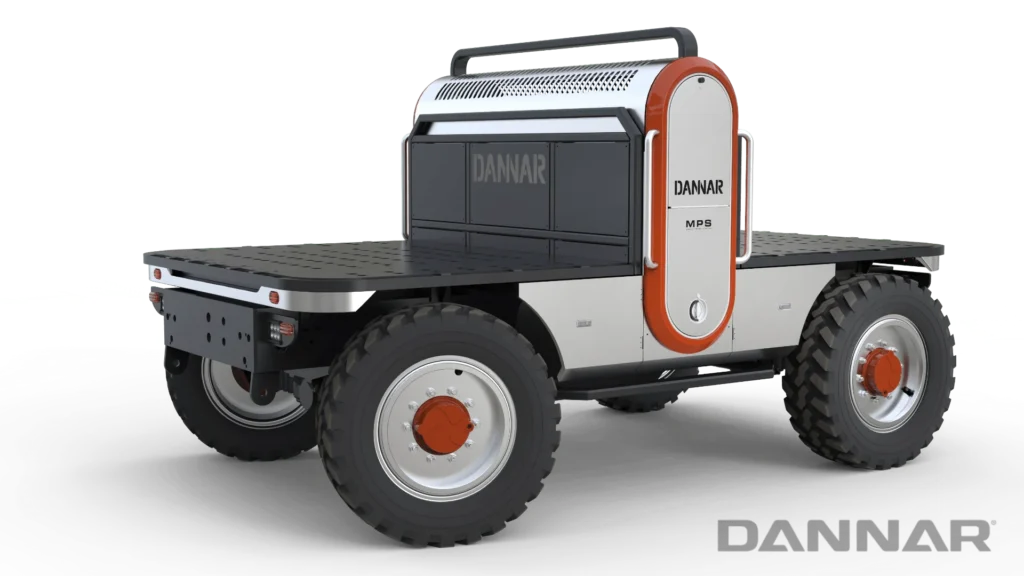
Electrification offers an opportunity to bring a much higher degree of customization to the off-road world, and Dannar, Inc. was founded to offer a modular EV platform that can work with most of the attachments that already exist for diesel equipment. Now, fleet buyers can benefit not only from the savings on fuel and maintenance that EVs offer, but also from the ability to perform more tasks with the same powertrain platform—perhaps using one vehicle to do a variety of jobs that would previously have required two or more separate pieces of equipment.
Charged spoke with founder and CEO Gary Dannar.
Charged: How about a brief history of the company and your personal background?
Gary Dannar: I started the business 13 years ago. My background personally has been 35 years in off-road industry equipment for global manufacturers. It became clear around the turn of the century that electrification was becoming more relevant for commercial off-road vehicles, and we recognized that a multipurpose platform was really what the industry wanted. Multipurpose year-round use is very advantageous to commercial fleets—agriculture, construction, military, emergency response and more. So, we started with a concept, went through four generations, and today we have good relationships with suppliers and customers, a backlog of Mobile Power Station (MPS) orders and several machines out in the field.
“We’ve made the multipurpose platform in such a way that we can use all those attachments that are manufactured by great companies, that allow fleet owners to use that machine year-round.”
Charged: Multipurpose means building different types of vehicles on the same platform?
Gary Dannar: Exactly. The platform we started with was an off-road platform that had been in the industry for decades—a 20,000-pound military forklift platform using a diesel engine—so we had a lot of confidence in that frame and that undercarriage, which featured Dana 212 axles, limited slip, four-wheel drive and four-wheel steer. But we wanted a platform that could receive winter equipment such as snow blowers and plows, but also summer equipment like mowers, trenchers and asphalt planers. We’ve made the multipurpose platform in such a way that we can use all those attachments that are manufactured by great companies, that allow fleet owners to use that machine year-round.
Charged: So, a fleet might use that platform for several different applications, changing the attachments instead of having to buy several pieces of equipment?
Gary Dannar: That’s exactly right. What we provide is basically three versions on the same frame, and the difference has to do with the batteries. We are currently using the BMW i3 battery pack, a high-volume off-the-shelf battery. The 250 kWh and 375 kWh versions of the MPS can be configured with a cab and several attachments like a loader, scissor lift, forklift and more, while also featuring a robust charging capability. The last version has as much energy on board as possible—500 kWh—and we offer 480-volt 3-phase as an option for DC fast chargers. Perhaps a customer wants four DC fast chargers on board—we can do that. This version is all about energy delivery, being able to receive charges from anywhere, and export that energy in multiple formats. All three can charge other vehicles, but the 500 kWh MPS can charge large equipment such as excavators and loaders.
Also, all three versions can be controlled with a wireless remote control from up to one mile away. It’s an encrypted, one-mile, line-of-sight control. We have semi-autonomous features in development with some military functions now.
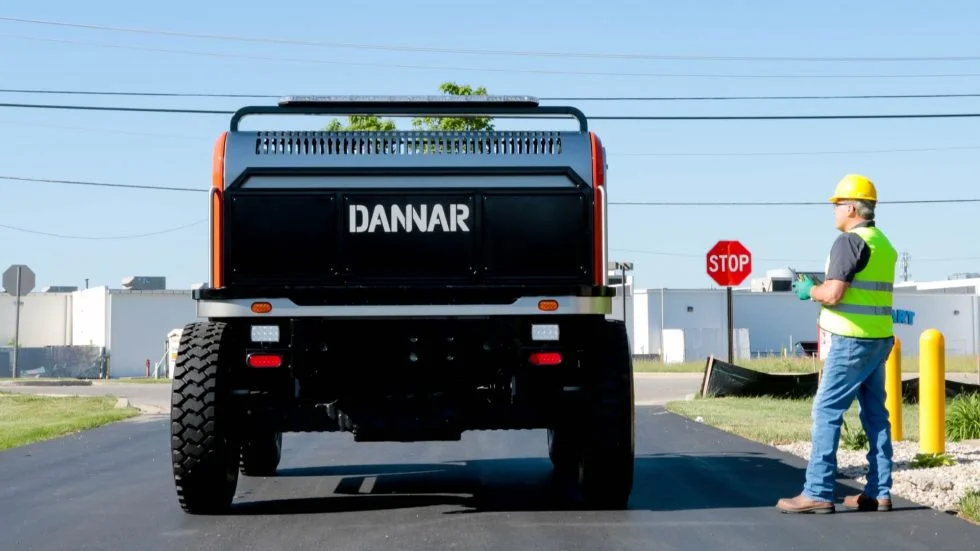
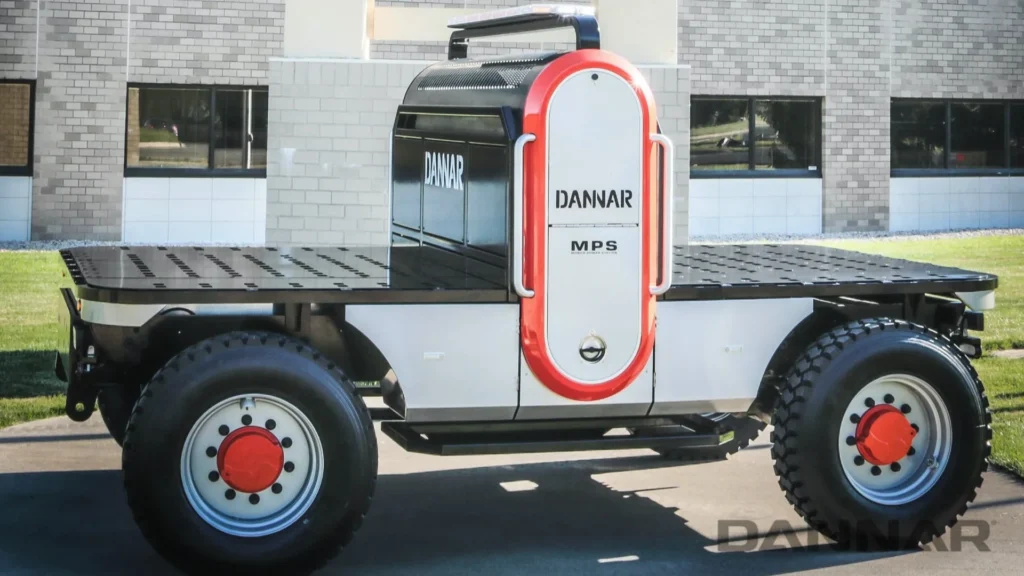
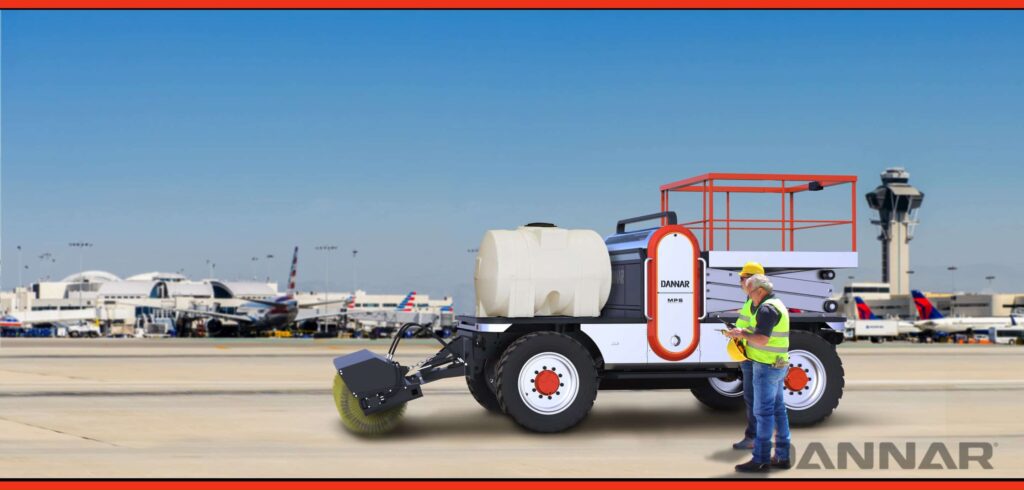
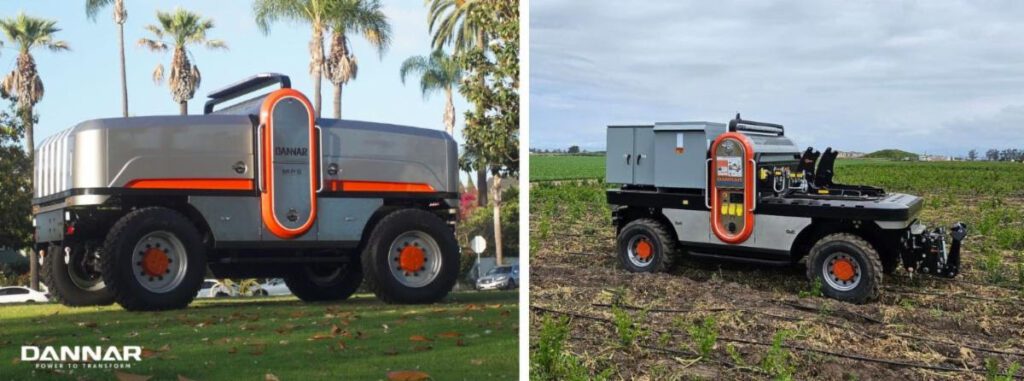
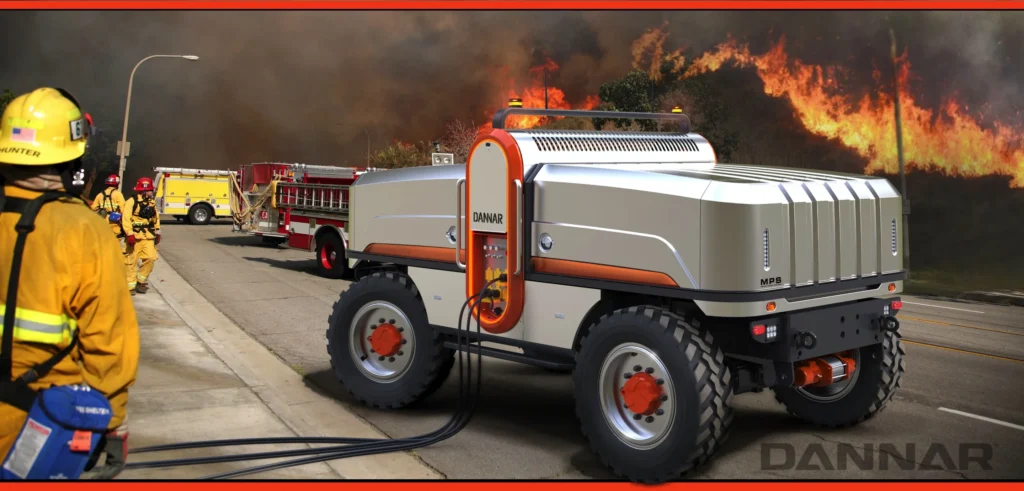

Charged: We’ve spoken with companies that are doing something similar with on-road vehicles. Ree Automotive makes a skateboard platform that’s designed for customers and upfitters to put bodies on top of. I guess they’re taking a concept that has always existed in the gas world and adapting it to the EV world. Is your product like an off-road version of that, or are there some other differences?
Gary Dannar: Well, the theme is very common. As you mentioned, the chassis cab idea’s been around for a long, long time. It has a frame and possibly a cab on the front, along with an engine and transmission. Now you can put an ambulance body on there, you can put a tank on there, you can do whatever you want with it.
That has never happened in the off-road industry. We’re really the first one to bring in a mobile multipurpose platform that is finished to the point that you can use it as is to receive branded attachments—a Viking snow blower, a Bradco trencher, a Caterpillar backhoe, a John Deere trencher—and it’s designed so the fleet manager can change that weekly or monthly or seasonally as the need changes.
After World War II, a couple of brothers, Louis and Cyril Keller of Minnesota, invented a little four-wheel skid steer that could fit inside chicken coops and be used to clean them out. This evolved into what is now called a Bobcat. People soon realized that you could put attachments on that bucket plate, and over the last 30-plus years, people started recognizing that work attachments could fasten onto the loader arms.
By all means, there’s a lot of single-purpose equipment that’s been designed to do wonderful work at just one thing, or just a few things—for example a tractor/loader/backhoe. That’s great, but there’s more than just that—there’s lots of attachments. We made our platform so it can receive all those skid steer attachments, and it can also receive platform attachments like scissor lifts and dump beds and cranes. There are over 250 attachments alone from just one manufacturer, so the number of use cases is endless.
Charged: These are existing attachments that are made to go on diesel-powered vehicles?
Gary Dannar: That’s right. Now some of them are hydraulically powered, and we have a hydraulic system on the Mobile Power Station now. The hydraulic system is run from an electric motor, so you end up with the best of both worlds. You have a high-torque electric motor with variable speed that is able to run a hydraulic system extremely efficiently and with a lot of control. That means a lot of these hydraulic attachments and tools actually work better.
Charged: You must have had to cooperate pretty closely with the companies that make these attachments in order to make sure that everything was going to fit onto your platform with a minimum of work.
Gary Dannar: Absolutely. The cooperation, though, is more engineering teams working together to make sure that things are compatible so the end user will not have problems. Electric power is very controllable.
It hasn’t been difficult to work with large companies and make sure their attachments will fit on a zero-emission vehicle. The names are familiar: Caterpillar, Case, John Deere, JCB, Komatsu, and European brands. After 30-plus years, most attachments are pretty universal. There are still some proprietary connections, or handshakes if you will, but most people making those attachments would rather use a universal, well-adopted type of attachment mechanism so it can work on any brand of tractor. That’s a concept borrowed from agriculture—think about all the attachments that go on a three-point hitch.
Charged: Someone told me that the hydraulic systems on these things are one of the main things that go wrong, and are hard to maintain.
Gary Dannar: Well, the hydraulic manufacturers have been doing diesel-electric for a long time, as well as diesel-hydraulic, and then electric-hydraulic. But an internal combustion engine, in order to be at optimum torque and horsepower, needs to spin at 2,000 or 2,200 RPM. Many times, that RPM is correlated with a mechanical PTO shaft coming out the back and turning at 1,000 RPM, but the hydraulic pump always has to spin at 2,000 RPM, and there’s no clutch in between. So, hydraulics have been designed for decades in a way that when you don’t want to pump oil, the pump itself goes to neutral but it’s still spinning at 2,000 RPM. There are other systems that are designed to send the oil back to a tank if it’s not needed to run a cylinder or motor, but the pump is still running at 2,000 RPM. That results in a lot of lost energy and added wear and tear on the hydraulic pump, because as long as the engine is running, the hydraulic pump is running.
With an electric motor, if nothing is moving. The battery’s not giving up any energy. And if you say, “I want just a little bit to happen for just the next 30 seconds,” that’s all that happens. A few electrons leave the battery, go to the motor, it only works for a few seconds and it’s over. So having the opportunity to be that efficient with energy, that it only moves when there’s a requirement, improves the durability and lifecycle of the hydraulic system.
Charged: I have heard that cited as an advantage of electric equipment—unlike diesel equipment, which is idling all the time, the electric equipment only needs to run when it’s working, so the hours of operation are less than one might think. You’re saying that there’s an additional advantage in that you’re also saving wear and tear on the hydraulic components.
Gary Dannar: Exactly. It was one of the first things that started showing up when the industry started going electric. The mining industry and defense industry found that the advantages of not idling showed up almost immediately.
“Having the opportunity to be that efficient with energy, that it only moves when there’s a requirement, improves the durability and lifecycle of the hydraulic system.”
The last point I would make is that some of these electric machines in construction, agriculture, mining and so forth are smart enough to recapture energy, just like automobiles. When you hit the brakes, it’s putting electricity back in the battery—but it goes a step further. When you have an excavator and you are using that power to dig and pull and swing that machine over a heavy load in one direction, when you slow down, you can recapture energy from that activity.
You can start regenerating on a particular movement. Meaning if I have an electric forklift and raise 20,000 pounds to set it on the third story, the whole time it’s coming down, it’s putting electricity back in the battery. Or the forklift lifts up to the third story and grabs the 20,000 pounds to bring it down, the whole time it’s coming down it’s putting energy back into the battery. So, there’s an opportunity in construction equipment to actually recapture energy back into the battery. You can’t do that with internal combustion engines.
Charged: Tell me about some of the different markets for your equipment.
Gary Dannar: It’s all markets. Working machinery has had over a hundred years to be specialized and add productivity to all industries. This includes cemeteries, railroads, amusement parks, the film industry. You can’t name any industry that isn’t using machines. Today, they’re using traditional forms of power, and we recognized long ago that electric power was the best work power.
We know that things work better with electricity. We electrified the toothbrush, for heaven’s sake! All of those industries are going electric. They make the first move because of low cost and low maintenance, but they soon find that clean energy is not only safer, but it’s quiet, and quiet is also safer. You can actually hear someone next to this machine running. The utility industry figured that out very quickly with bucket trucks and putting a person 20 feet up in the air. When that becomes electric, they can actually talk to one another. Communication using things like hand signals doesn’t go away, but you can actually hear people around you as you’re working.
Charged: What can you tell us about some existing customers and partners that you’re working with?
Gary Dannar: We’ve actually sold into nine industries at this point, but the ones that are at the top are construction, agriculture, cities, counties, states, anyone that is maintaining large commercial fleets for infrastructure. The emergency response and defense industries have been focused on electric for a long time.
As you would guess, for emergency response, usually there’s a power component involved. The loss of power, like what was experienced recently in Florida, is a great example. These work machines can respond to whatever the emergency is, like a collapsed building or a downed power line. It can bring the right tool to do the work, but it also can power communications, lights, water pumps, and charge other vehicles. You need a fuel truck on a construction site any time machinery shows up. We’re the “electric fuel truck.”
Charged: Do you build any components yourself, or do you mostly buy off-the-shelf components?
Gary Dannar: From the very beginning, we’ve focused on buying high-volume components that are proven in the off-road industry. High volume also means great product support and parts availability. There’s not a real price penalty for going electric because we’re using high-volume parts throughout the process. We assemble the entire MPS in our facility and have some proprietary manufacturing, but really what we’ve done is create software to make the hardware perform better than ever before. The MPS is basically a bill of materials engineered around what we can source at high volume, but we use our proprietary software to make all the various components work together.
We made a decision early on that we would always be open to whatever the best components were for our end users, so we’re battery-agnostic. We do use BMW batteries, but we will also be using other batteries, and as a US manufacturer, we want to see a very high percentage of domestic content. It’s exciting to see American manufacturing responding to this electrification movement. There are more and more great American companies now that are manufacturing inverters, chargers, and both high- and low-voltage components. We are constantly changing and adapting to those. We’re seeing that an underground mine might have a different preference for batteries and components, however, agriculture might have a different price point, so we want to be very flexible.
“We’re open to whatever the best components were for our end users, so we’re battery-agnostic. It’s exciting to see more and more great American companies manufacturing components. We are constantly changing and adapting to those.”
Charged: Are there any existing customers that you can name at this point?
Gary Dannar: Most of our customers are government fleets, and unfortunately, we’re not in a position to discuss our specific customers. I can say that all branches of the defense community have either tested an MPS, are currently using one, or have one or more units on order. The same with cities and counties—we have machines at city, county and state level, in addition to utility companies.
Charged: Do you have any machines in Florida right now?
Gary Dannar: The City of Orlando is a customer of ours, and we have their MPS in our building because we are upgrading that machine with some new batteries. Our machine is very modular, and the whole idea was that it can always be upfitted, upgraded and changed to have the latest components. That’s exactly what we’re doing with the City of Orlando’s machine.
Charged: Here in the Tampa Bay region, we’re currently living in a disaster area. My neighborhood got an eight-foot storm surge and the whole peninsula was covered with four feet of sand. The first thing they had to do was bring in loads of diesel fuel. A few days after the storm, I saw a huge truck loaded with tanks of diesel, and I said, “Aha! That means they’re getting ready to start digging out this sand.” Since then, the whole neighborhood has been filled with the roar and stink of engines. I for one would love to see some electric machines doing the work.
Gary Dannar: We actually have people we work with in Florida, and I know you’re living through a tragedy. Too many times, it is in the tragedy that it is most noticeable that there is a void in having the right equipment in the right place at the right time. That’s emergency response.
The defense community has been struggling with this for a long time. Adversaries would know something was coming when the diesel fuel started showing up. That’s not a very good tactical way to run an invasion. Before the defense community can start getting troops and equipment mobilized, they need to make sure they have fuel in place. The logistics of getting the energy to where it is needed and quickly has always been a challenge. Most people don’t know that we went to the first Gulf War with electric vehicles.
Containers of batteries are showing up all over the place, so instead of the diesel tanks, a container of electricity will be delivered, and now you can have electricity immediately available to run electric equipment and handle everyday power needs.
For those of us who are on the front edge of this, there are already excavators and loaders working on job sites. The question to fleet managers is: Do you want the diesel model or do you want the electric model?
Florida emergency responders will figure out how they want to start acquiring the right equipment for the future. If they have a choice of getting an electric excavator on that beach in front of your house or a diesel, I think they’re going to choose the electric excavator. And I think you’re going to see electric equipment being used for search and rescue missions, such as the condo collapse in Florida. What would’ve been more advantageous for that site where dogs and rescuers were searching?
The answer is quiet, clean electric equipment that can remove rubble and debris with little noise and vibration. I think it’s going to show up in these disaster emergency response areas very quickly, just like it’s already shown up for us in defense applications. And these are just two industries responding to the advantage of all-electric off-road equipment and energy supply systems.