Charging power levels are heading upwards to accommodate longer EV ranges, and it’s becoming apparent that some sort of cooling system for charging cables will be needed.
The Swiss firm HUBER+SUHNER has introduced a cable and connector with an integrated cooling system that allows high power throughput while keeping charging times below 20 minutes (to 80% state of charge). The cables are designed to be highly flexible, lightweight and easy to handle – they are slimmer in diameter than a gas hose at a legacy filling station.
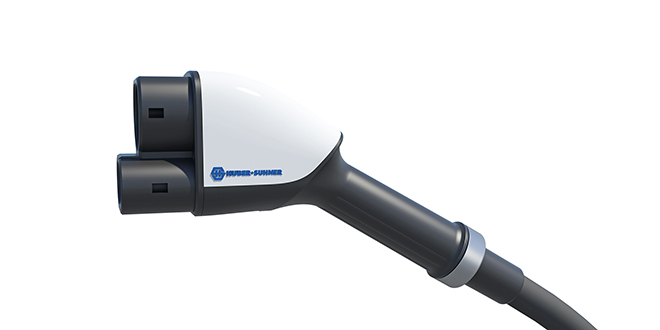
HUBER+SUHNER’s cooled cable system enables charging currents of 500 amperes and higher. It is available with CCS type-1 (USA, Canada) and type-2 connectors (Europe), and can be customized with customer-specific design and labeling.
The system includes the connector, cable, inlet to HP-CS, junction to power supply, cooling system with pump heat exchanger or cooler and coolant. It features integrated stress relief, and has nominal system performance of 350 A and 1,000 V according to the ISO/IEC 61851-23 standard.
Source: HUBER+SUHNER