“I am testing these motor flying Inverters on this motor flying plane”
Motors, inverters, and power systems for electric aircraft have strict requirements for weight, efficiency, and safety. For this reason, these motors are pushing technology, going to higher voltages, high phase counts, and unique topologies for both the motors and inverters. Many of these decisions have electrical and mechanical effects that affect the entire aircraft. These evolutions in motor technology require significant amounts of testing from prototype to installation, and ultimately certification. A significant amount of this testing is not only on the components but involves testing the entire aircraft electrical network for system stability and certification.
In this webinar at the Fall Virtual Conference on EV Engineering, presented by HBK, we will review new tests for evaluating these motors and power systems:
- Copper bird testing & flight cycles
- High phase count evaluation
- Failure testing
- High fundamental testing
- Electromechanical evaluation
- Structural effects of electric motors
- High voltage measurements
Other sessions at our Fall Virtual Conference include:
Managing Heat Through E-Fluids
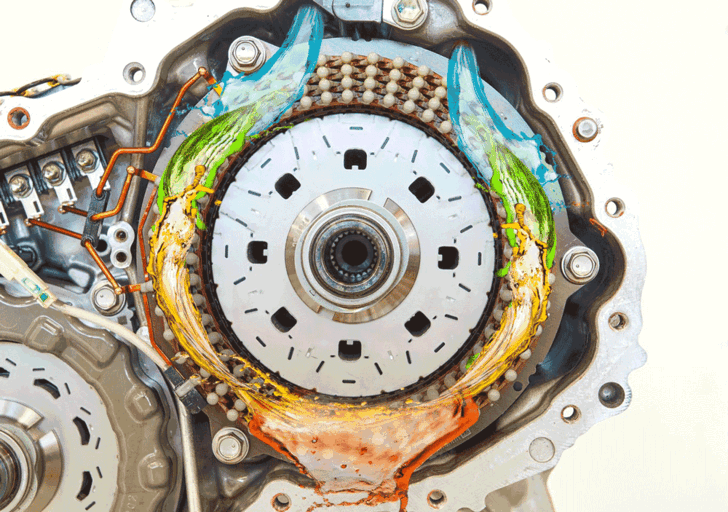
New thermal management driveline e-fluids, designed to enable the latest electrified powertrains and batteries to perform at their very best, have been developed for the latest electric vehicle hardware.
For example, many earlier electric vehicle powertrains were developed using automatic transmission fluids (ATF). Not optimised for EVs or their thermal management, these are being superseded by the latest generation of lubricant fluid technology, termed driveline “e-fluids”. e-Fluids are optimized for automotive electrified hardware types, such as the latest generation of e-axles, and cool and protect such devices much more effectively.
Lubricants are now expected to be in direct contact with powered motor windings and exposed and electrically insulated electrical components. Characteristics such as the ability to cool electrically energized surfaces in addition to other surfaces that can become hot as well as the protection of exposed electrics are of increased importance.
Motor efficiency increases with reduced fluid churning losses and suitable cooling. It can be further improved using optimised fluids which provide thermal management. Ensuring suitable wear performance as required by the hardware engineers is of vital importance to protect the gears and bearings, and is an essential benefit provided by the e-fluids.
The latest types of additive components used in e-fluids have evolved significantly over traditional types, and a new class will be described in the webinar. This is the most recent type of powertrain e-fluid technology to enter the market, which has no corrosive active sulfur additive present, sometimes termed “sulfur-free”.
The e-fluid is an engineered component and forms part of the overall design of the electrified hardware. The presentation will cover the fundamentals of the latest e-fluid design, fluid properties, and how a thermal management e-fluid is best evaluated for performance.
This presentation will be of interest to engineers and fluid formulators seeking an introduction the basic principles behind fluid thermal design. In addition, the latest fluid testing methods to address some of the hardware challenges, resolved by the fluid, will be described with the aim of enabling the engineer to make the best thermal management fluid choice for their latest hardware designs.
See the full session list for the Fall Virtual Conference on EV Engineering here.

Broadcast live on October 2 – 5, 2023, the conference content will span the EV engineering supply chain and ecosystem, including motor and power electronics design and manufacturing, cell development, battery systems, testing, powertrains, thermal management, circuit protection, wire and cable, EMI/EMC and more.