There is no doubt that the early days of charging infrastructure rollout had some bumps in the road. Plug-in vehicles interact with the outside world in a much more complicated way than legacy gas-guzzlers do, which led to early interoperability issues. The automakers needed to quickly learn how to work with many infrastructure and hardware providers to be certain that newly launched vehicles worked flawlessly in many different environments. Thankfully, the major car companies and testing organizations continue to make significant strides towards eradicating interoperability issues.
Another lingering problem experienced by EV drivers is equipment outages – pulling up to a charging station only to find that it’s out of order. Or in some cases, the station appears to be operational but does not deliver any energy.
As the market for EVs continues to grow, it is critically important for the industry – and individual brands – that public charging stations have as little downtime as possible. Impressions of poor quality can be very damaging and last for years after any real issue has been fixed.
The UK-based Seaward Group recently launched a new handheld charge point tester. The company says that its EV110 EVSE test and diagnostic tool for AC charging fills a major gap in the industry’s ability to raise the quality control of charging stations installations to higher levels.
Charged recently chatted with Jim Wallace, Seaward’s Technical Standards and Applications Specialist, to learn more about the new charging station testing tool.
Charged: This is Seaward’s first testing product for the plug-in vehicle industry. Why did you decide to enter the EV market?
Jim Wallace: The availability of good testing tools tends to dictate the level of testing people will do in a given industry. If you ask any electrical equipment installer they will say, “Yes, of course, we test to make sure installations are safe, installed properly, etc.” But, in reality, when the diagnostic tools are expensive or less accessible, it tends to happen less and less. And when highly capable off-the-shelf tools are available and affordable, it tends to happen more and more.
When we started looking at the charging station industry about six years ago, we were a little surprised at the very limited amount of testing that actually goes on. From the point of view of safety, but also from the point of view of insuring that these things are operational on an ongoing basis. The future of EVs is, in part, dependent on the infrastructure. The public will only buy into this when they’re satisfied that the vehicles will have a range that’s adequate for their needs, but also when there’s a healthy infrastructure in their area that’s consistently operational.
We had some discussions with different groups in the EV industry, and they all had a similar story about the lack of dedicated test and diagnostic equipment available. They were all struggling at the time to verify that new charging stations were properly installed, fully operational and safe. Some installers would take an EV with them and plug it in to see if it starts charging, which is not a very comprehensive test. And in cases where installers didn’t have a plug-in vehicle, they just assumed the charger was wired correctly and hoped everything was safe and fully operational.
We found that various EVSE manufacturers had access to some test equipment, usually some kind of dedicated solution that they put together with their expertise in how an EVSE should operate. Outside of that there was pretty much nothing available besides some very simple devices.
The problem is that in many cases it’s not the EVSE manufacturers who are installing the chargers, it’s subcontractors or customers. How can you ensure the quality of work carried out on your behalf by a third party? If a customer comes up to a charging station that doesn’t work, it’s your name that’s written on the front of it. It’s your equipment they’re going to blame and be unhappy with.
So, we set out to make a safety-testing tool but also a quality control tool. We thought, wouldn’t it be great if third parties working on your behalf could supply you with a report based on collected data? Then you could confirm that every installation followed your instructions. So, we also built an app that comes with the tester to capture all of the pulse-width modulation (PWM) data, duty cycle, response time, etc. and create a full diagnostic report on your cell phone capable of generating certificates.
When we were looking into the market, we also found all of the various industry reports saying that EVs were emerging quickly with high growth rates around the world, so it also ticked all the boxes from a commercial point of view. We decided to work with a lot of people in the industry, who gave us guidance on exactly how the equipment is supposed to operate, what their needs were in terms of test requirements, diagnostics, etc. We also have a long track record with electrical test equipment in terms of international standards bodies, national standards and legislation.
Charged: Can you give us an idea of how it works?
Wallace: The handheld unit comes with a cable harness that plugs into a port on the instrument. Then, you plug the charging station into the port on the other end of the harness. Because of the physical size of the connectors involved, there isn’t a big enough piece of real estate on the tool to fit a connector. Also, we launched the testing tool at the end of 2015 in the US and European markets simultaneously, so using a cable harness assembly allowed us to make a single product for all the markets, and supply connectors as appropriate.
Basically, you plug it in and through a few simple key presses it simulates the presence of an EV to energize the charging post. It will step it through all of the different states to make sure it’s within tolerances, and it will also measure the PWM signal between the vehicle and charging post. It measures the PWM frequency and duty cycle and compares that with the requirements of the standard. It captures all of that diagnostic info and stores it in the tester.
Then it will request a charge and energize the EVSE to measure things like its ability to supply the correct line voltage. Equally important is that we make sure that when the vehicle is finished charging, the voltage disappears and the contactor is operating correctly. It will also do a test called the ground loop impedance test. We’ll measure the resistance of the ground connection to the charging station to take sure it’s safe. We also have a test to measure the tripping current of the ground fault circuit interrupter (GFCI), to make sure it operates correctly.
Charged: It will test the charger’s cable too, is that correct?
Wallace: Yes, we measure the insulation resistance between all of the live conductors in the cable and the ground wire. It is a stand-alone test operated by a specific test key rather than part of the auto test sequence. This gives the operator the opportunity to decide if the insulation test is appropriate for the EVSE.
There are challenges with the tethered cables found on the chargers in the US, because we can’t separate the cable from the charging station to test the cable alone. Some charging stations actually have either monitoring circuitry on the line conductors or some other low-resistance path, so if we try to do an insulation test at the vehicle end, it will give you an apparent failure that is not due to an insulation fault, it’s due to monitoring circuitry that’s in the charging station.
That is the reality of testing an electrical system or an electrical appliance that has components between live conductors and ground. An insulation tester can only indicate what it sees, and a test instrument cannot distinguish between an intentional path between live conductors and ground and an insulation fault.
This illustrates why electrical safety tests must be performed by a competent person who can determine which tests are appropriate for a given situation, and determine the cause of a low insulation resistance reading.
Charged: What are the most common faults or problems with charging stations found in the field?
Wallace: One of the most common problems I’ve come across, personally, is the lack of a pilot signal coming out of the charging station. When that happens, it will not recognize the presence of the vehicle. That caused us a lot of headaches while developing this tool because we assumed there must be a problem with our tester – that we weren’t simulating the vehicle correctly. So we took some other diagnostic kits out with us and found out that, while the posts were lit up and ready for use, they never responded to a request for charge because they had problems with a pilot signal.
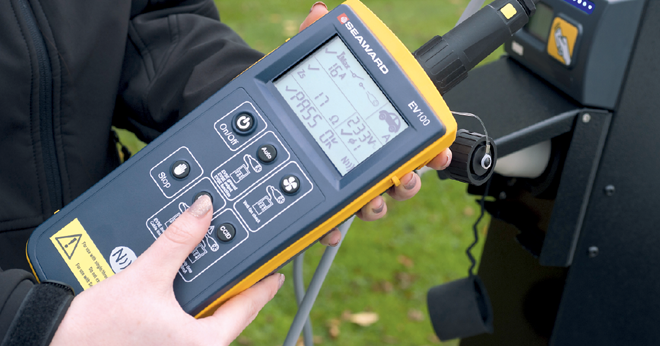
The second most common thing I’ve seen is tripped GFCIs – where someone plugged in a vehicle with a fault on it tripping the circuit, and then no one ever came out to reset it. In this case the charger will go through the motions but never deliver any power.
I’ve also seen a lot of mechanical faults where something is physically broken.
While developing the product over the course of a few years, I used chargers in our local area a lot, and I was really surprised at the number that were not operational, and the fact that they remained non-operational for long periods.
Charged: Things have changed a lot in the EV industry in the past few years. Have you found that the charging station outage situation has improved since you first started looking at the market?
Wallace: Yes, definitely. In our area, specifically, the uptake of EVs in general has helped. If no one ever uses the charging point, it will never be reported as faulty.
We still see media reports here in the UK about a large number of charge points that aren’t operational, but those tend to come from sources that are anti-EV for whatever reason. And if you look closely at their numbers, you’ll see data that is a bit tainted or misleading. I saw one that said 50% of chargers are not operational – but that included cases when there was a gas-powered vehicle blocking access. It didn’t mean all the charging points were faulty.
Also, a lot of the early first-generation hardware is now being replaced with charging stations that are designed much better. The manufacturers have learned a lot about designing the products, and the newer ones are more mechanically robust and smarter. If they do develop faults, for example, generally the modern systems will self-recover – a GFCI that will self-reset once the fault clears, for example.
We really believe that the EV110 EVSE test and diagnostic tool will go a long way towards making the quality of the EV experience even better. One recent example is a company that bought a fleet of EVs simply because they’re far more cost-effective than traditional fuel. They were having issues with charging, and all of a sudden they were involved in a dispute between the EVSE and vehicle manufacturers – each blaming the other for the fault. It’s possible that they’re both right – that the cars and charging stations are functioning as designed, and the quality of the installation is causing problems. In cases like this, having test equipment is invaluable. The customer doesn’t care whose fault it is, they just want it to work so they can get on with their business.
This article originally appeared in Charged Issue 24 – March/April 2016. Subscribe now.