When one thinks of Nikola Tesla and electric vehicles, the obvious connection points to Elon Musk’s favorite part-time project. However, we also have to give the Serbian inventor proper credit for pioneering technology that eventually may become even more important to EVs than battery breakthroughs. Tesla’s obsession with wireless power transmission defined much of his life. When he first demonstrated wireless energy transfer in 1891, he may not have thought about using the breakthrough to power a motor carriage – an invention a mere five years old at the time – although we wouldn’t put it past him.
We know that in many ways Tesla was far ahead of his time, and it was more than a century after his first wireless power demonstration that a form of wireless energy transmission known as inductive charging would be used to juice up the infamous General Motors EV1 and others such as the Toyota RAV4 EV. Those Magne Charge (also known as J1773) chargers used induction, but they still required the insertion of a paddle-type plug into the vehicle.
Hands-free inductive charging made a quiet debut in 2002, when the Italian cities of Turin and Genoa activated a couple dozen electric buses that were charged with induction coils installed in the bus chassis and at stopping points along the route. The German company Conductix-Wampfler produces the Inductive Power Transfer (ITP) system, which is still in use today. However, like hydrogen vehicles, inductive charging has largely remained one of those technologies that always seems a few years away.
Finally, those years for inductive charging are creeping up on us. In addition to Conductix-Wampfler, companies like Qualcomm, Momentum Dynamics, WiTricity, Evatran and WAVE have systems on the path to wide commercial availability.
A key turning point may have been in 2009, when WiTricity demonstrated wireless inductive power at a TED conference, and Evatran, maker of the Plugless Power EVSE based on inductive charging, was founded.
That was also the year that researchers at the Korea Advanced Institute of Science and Technology (KAIST) first tested its On-line Electric Vehicle (OLEV) system. This inductive charging scheme uses a technology called Shaped Magnetic Field in Resonance (SMFIR), which places lengths of cable beneath the street surface and allows compatible vehicles to receive a charge automatically while still in motion. In 2009, KAIST installed a system on its own campus and was able to charge vehicles inductively with 60 percent efficiency over a gap of 12 cm.
Since then, KAIST has steadily improved all aspects of OLEV, and spun off the technology into two companies: OLEV Korea and OLEV Technologies in Boston, launched in 2011. With a recently appointed CEO and a new round of angel funding, OLEV Technologies is poised to commercialize its wireless charging technology for commercial and industrial EVs in the US.
Power strips
Bryan S. Wilson, CEO and President of OLEV Technologies since December, arrived at the company 12 years after founding and successfully growing Northeast Wireless Services, which developed infrastructure for broadband wireless service providers. While his new post also deals with growing a wireless infrastructure business, it’s a whole new world for the executive. Still, he thinks that OLEV’s unique technology and cost-saving propositions practically speak for themselves.
For example, compared to OLEV’s 2009 results, the system can now charge with 85 percent efficiency at 100 kW over a gap of 20 cm. And with OLEV, vehicles can charge while in motion.
“Instead of having a coil that creates the inductive field – basically a dot like a manhole cover that the vehicle has to be stationary over, our inductive charging system is linear and charges in a strip,” Wilson said. “The vehicle can be charged either moving or stationary. A bus might stop for three minutes and pick up a charge, but if that bus needs additional power to go up a steep hill, our system can send the power directly to the motor while in motion.”

Last August, OLEV Korea set up its system for two buses in Gumi, South Korea, each running a continuous 24 km inner-city route. As an example of a typical application of the OLEV charging system, charging apparatuses are installed beneath the street in strips of concrete-encased wires 5 m at a time. The wires create the inductive charge, and when needed are placed in series, as in the case of “take-off segments” – 20 m strips that provide an extra lift for accelerating up hills.
“If it’s a 20 m strip, it’s not all 20 m turned on at the same time,” Wilson said. “It’s only 5 m turned on at any given time. They all run off of the same inductive inverter, so if you have five segments of charging strip, you don’t need five different electronic controllers – it’s all controlled by the same unit.”
The inductive charging begins almost instantaneously as soon as the vehicle is within reach of the charging electronics. Naturally, the idea is to install only as much charging infrastructure as needed – usually 10-15 percent of a total route, according to Wilson – but there is no limit to the length of the segmented charging strips.
“Obviously, if there’s one 5 m strip, and the vehicle’s running at 50 mph, it’s not going to pick up much of a charge,” Wilson said. “But the segments turn on and off as the vehicle goes over them. You theoretically could have an endless strip – the vehicle would charge the whole time it’s going regardless of the speed – and you’d never run out of battery charge. You could put in one of our charging systems around the Indianapolis Speedway and run a bus around it at 100 mph forever.”
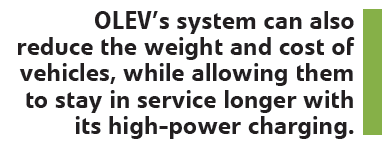
Benefits & applications
That life-size Hot Wheels racetrack scenario sounds like a blast, but OLEV rather has its sights set on economizing the performance of many types of heavy-duty industrial and commercial vehicles. By reducing the amount of batteries that such vehicles need by as much as two-thirds, OLEV’s system can also reduce the weight and cost of vehicles, according to Wilson, while allowing them to stay in service longer with its high-power charging.
Each of the current OLEV pickups charges at 20 kW, so on a large vehicle installation, five pickups along the bottom of the chassis would combine for a 100 kW charge rate. The OLEV companies and KAIST are working on a system that would charge at 200 kW, to hit the marketplace soon.
“Because we can charge at 100kW, we are most suited for transit buses or off-road vehicle applications, like airport equipment, cargo ship terminal equipment or mining equipment,” Wilson said. “Anything where a vehicle needs to be in service for a long period of time and needs to have no emissions, or reduced emissions.”
The high power of the OLEV charging system currently makes it impractical for consumer vehicles because of the equipment needed on the vehicle. “The pickups themselves are designed for high-power transfer, and weigh about 400 lbs apiece,” Wilson said, “so it wouldn’t make sense to put something like that on a Nissan LEAF. But it sure makes sense to put it on a 40,000 lbs transit bus if you can save thousands of pounds in battery weight by doing that. So we’re probably not going to compete in the space with WiTricity or Plugless, which are trying to do an installation for somebody’s driveway or garage.”
OLEV’s specific market niche gives it the advantage of going after service vehicles that currently show a total cost of ownership savings when electrified, and then making their lifetime costs even lower. Wilson also mentioned that it doesn’t hurt that there are currently federal and other subsidy dollars available to municipalities to add electric buses to their rosters.
“It’s attractive for operators to pay the premium for electric busses right now,” Wilson said. “In terms of acquisition costs, electric buses aren’t really competitive with diesel busses, but for total cost of ownership, they’re much more attractive. Our infrastructure that goes in the road can charge all of the buses on that route. So if you have 10 buses that typically run a 10-mile route around the city, and you can reduce the batteries by two-thirds on all of them, then it’s more of a cost savings using our technology. These things are easy to install overnight at a low cost. There are no moving parts; there are not a lot of electronics. What goes on the bus is just an inductive pickup. There’s a small box that goes on the roadside that connects to the electrical grid. The system’s really low maintenance.”
With OLEV’s SMFIR system on the verge of going into production, the company is seeking capital that would enable it to produce the hardware in the United States, rather than ordering it from Korea. Concurrently, Wilson is courting as many potential customers as possible. “We are reaching out to electric bus companies, municipalities, marine terminal operators, mining companies, airlines and anybody who has an electric vehicle they need to keep in service and either reduce costs or weight,” Wilson said.
OLEV’s system can potentially save its customers additional money by avoiding standalone large-capacity recharging facilities, and save employee person-hours by eliminating the need for battery swaps and other tasks. Wilson gave the example of industrial warehouse forklifts, which are often subject to expensive battery swapping. “With our system, they never have to go offline,” Wilson said. “They can recharge while in motion, or the operator can just park it in a certain place to recharge. Potential customers also have told us that in situations where they need to plug in a vehicle to recharge the batteries, a specific employee has to do that – they can’t just let the operator plug it in. It has to do with union regulations and operational protocols.”
Because the OLEV SMFIR system is not a pantograph-type system like the one commonly used on electrified streetcars, the vehicles can move off the specified route at any time. That makes it attractive in cases where a set route is usually followed but is not constant, like the aforementioned warehouse vehicles or airport baggage handling systems and aircraft tugs.
The possibilities for KAIST’s system, which is now in pilot programs in the Seoul, Jejudo, Daejeon, and Sejong regions of South Korea, are legion. And now, four years after SMFIR was named to Time Magazine’s 50 Best Inventions of 2010, this could be its time to make its mark on American transportation and industrial efficiency.
This article originally appeared in Charged Issue 12 – FEB 2014
