How higher-voltage battery packs enable faster charging ecosystems
Porsche took on a considerable engineering challenge when it decided to design an 800 V EV system for the Taycan, because nearly every other hybrid and EV in the world operates at 400 V or less. There simply was not a wide range of high-voltage off-the-shelf parts that have been rigorously tested for the high demands of the automotive world (operating every day, in any climate on earth, for 10 to 15 years without issue). So, Porsche reportedly worked very closely with suppliers to design and qualify everything from the power semiconductors to the insulation.
But why go to the trouble? The answer comes down to heat generation along the charging current path from the electrical grid to the cells – in particular, the heat generated in DC fast charging cables and connectors. In fact, this is the limiting factor of the 400 V EV fast charging ecosystem.
Claiming that a higher battery voltage allows for faster charging doesn’t sound right at first. After all, an EV battery has a certain energy capacity in kWh, and it really doesn’t matter if that is achieved with 200 V * 200 Ah, 400 V * 100 Ah or 800 V * 50 Ah. A 100 kW fast charger isn’t going to cram energy back into a battery any faster at 800 V than at 400 V or 200 V; charging time is, quite simply, battery capacity divided by charger power.
However, with all other things equal, the heat energy generated in a conductor is related to its cross-section and the level of current. In the case of DCFC cables and connectors, they are already quite bulky and increasing the size (or cross-section) is not possible if everyday humans are expected to handle them practically. This is why we now see a lot of companies working on liquid-cooled charging cables and increasing the overall system voltage.
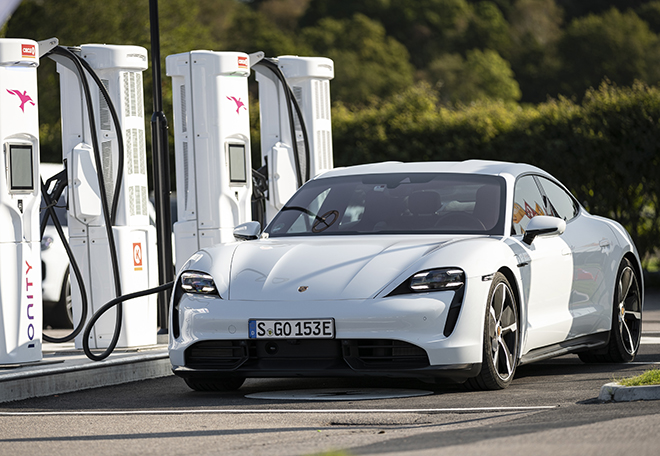
That may seem like convoluted logic for Porsche to consider when designing a new vehicle – after all, the car company doesn’t manufacture DC fast charging stations. Why would it care about those engineering problems?
Here’s another way to look at the history of higher-voltage EVs.
In the early days, EV fast charging was limited by the cells. They could only accept limited high-power charging at the ideal temperature, or it was unsafe.
However, slowly but surely, battery tech is improving. Cells can accept much higher charge rates at wider temperature ranges. Large battery packs maxed out at 50 kW, then 100 kW, then 150 kW, and higher rates are expected in the future that will exceed first-generation CHAdeMO and CCS maximum specs. So CHAdeMO and CCS developed next-gen specs, which went from about 500 V to 1,000 V max – to cram more power through the same size cable without increasing heat generation (because, again, you can’t make the cables any bigger, so you have to increase the voltage if you want more power: P=V*I).
So now, if Porsche or any other EV maker wanted to use these future ultra-fast charging stations, they would have to build EVs with higher pack voltages.
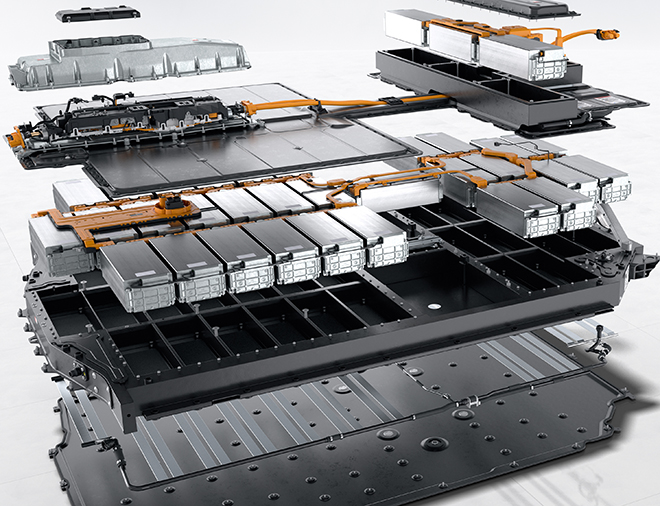
The Taycan’s 800 V pack doesn’t rely on any revolutionary battery tech. The cells are arranged in a sequence of series and parallel connections that increases the overall pack voltage. The same cells could be arranged in a 350 to 400 V pack sequence with the same overall pack capacity as the 800 V arrangement.
The big engineering challenge, however, is that using a higher-voltage pack affects the design of many other systems in the EV. Because increasing the battery voltage from 400 V to 800 V requires substantial modifications to every device in the drivetrain, this needs to be implemented at the earliest point in the design process: motors need more turns, conductors need more insulation, inverters need 1,200 V-rated components in the power stage, etc. And since Porsche’s typical suppliers weren’t producing higher-voltage automotive grade components (i.e. no MOSFETs or IGBTs to make a higher-voltage EV inverter) the automaker had to work with its suppliers to solve that problem too.
But the whole reason the company went through the 800-volt effort is that conductive parts get too hot along the charging current path from the grid to the cells – mainly the DCFC cable and connectors, which can’t be made any larger.
Read more EV Tech Explained articles.
Sources: Porsche, Ars Technica, IEEE Spectrum