There are many innovations to improve power density in stator windings at the moment, with technologies like axial flux motors gaining momentum. On the other side, radial flux motors with hairpin windings are getting pushed to new limits in terms of efficiency and industrialization.
WAFIOS is the world leader in wire bending for almost 130 years, and is always up for new challenges.
For the applications of flat wire edge-wise winding, WAFIOS came up with a unique new tooling concept that allows the maximum possible fill factor in an axial flux stator. The flexibility of the CNC equipment makes it possible to manufacture axial flux motor windings complete on one machine, without additional process steps.
This tooling concept can also be applied to rigid busbars up to 200mm², an exciting product that WAFIOS has been delivering production cells globally since 2014.
Join this presentation at our Spring Virtual Conference on EV Engineering, presented by WAFIOS, to learn more about flexible wire forming solutions, stator winding, and power density!
Other sessions at our Spring Virtual Conference include:
Electrical Insulation Materials In E-Drives: Sustainability. Performance. Efficiency.
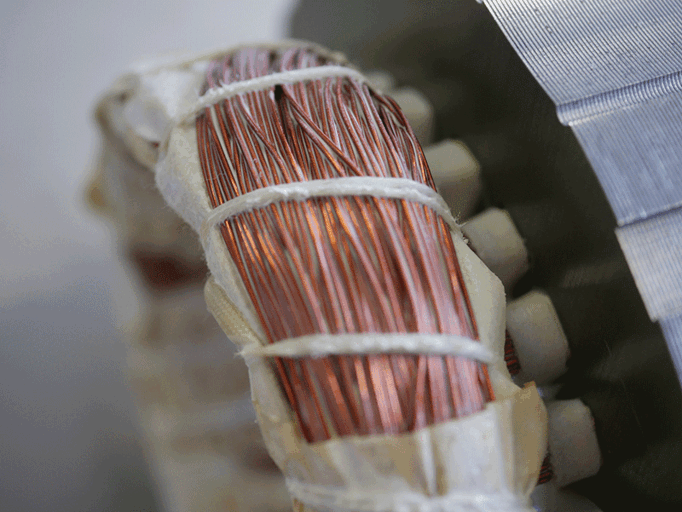
The electric industry has seen a wave of new development during the past decade. E-mobility and energy transition towards renewable resources have been key drivers to this evolution without any doubt. Yet new advances allow improving the sustainability of e-drives even further, be it through new motor designs or materials that allow for less copper or electrical steel in an electric motor. Metals make up for the major portion of cost in electric machines, thus metal usage and quantity of metal used are driving the CO2 balance in a similar manner as cost. Key enablers have been thermally conductive insulation materials and materials with exceptionally high thermal rating as well as improved thermal management of the lamination steel core by using novel joining technologies, like Backlack technology.
Improving the carbon footprint by saving metal is a major driver, however, Axalta keeps working on the sustainability of insulation materials itself. Impregnating resins are increasingly switching from styrene or vinyltoluene based materials towards epoxy or acrylate materials without volatiles, reducing emissions and improving operators’ lives significantly. Electrical steel coatings are almost exclusively waterborne and advanced materials have eliminated Chromium (VI) from their formulations. Further, the increased use of renewable raw materials will help to lower carbon footprint.
Wire enamels are using coal-based solvents (phenol, cresylic acid etc.) or low molecular amides (NMP, DMF, DMAc). Axalta takes on the challenge to replace those feedstocks by more environmentally and user-friendly solvents, reducing toxicity and hazard on the shop floor level. Further, coal as a feedstock may see more dynamics in the future due to the energy transition itself. Following this approach the overall manufacturing process cost can be kept at the same level as the current state, eliminating special storage conditions or exhaust air treatment by improving the level of material usage, while keeping performance at least on the same level as conventional materials.
Register here to learn more—it’s free!
The Key Factors Of Hairpin Stator Impregnation For EV Motors
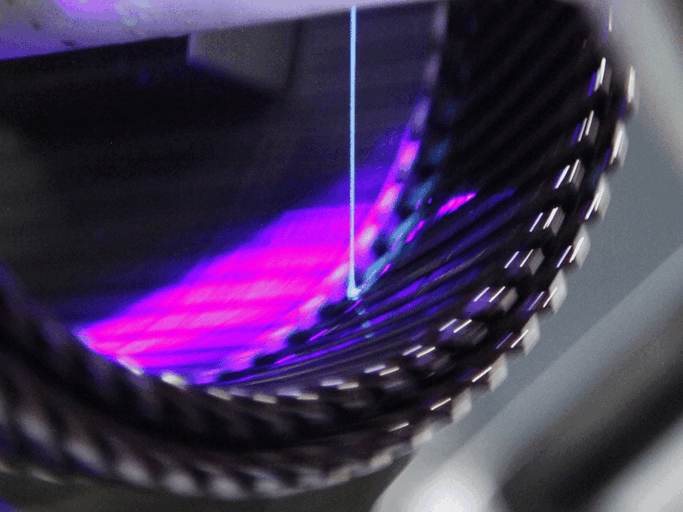
The launch of the hairpin technology applied to electric traction motors has changed the concept of traditional impregnation. Tecnofirma has committed itself to research innovative techniques to continue obtaining high-quality levels.
In a recent study conducted in collaboration with the Politecnico di Milano, Tecnofirma has developed a theoretical calculation method that is representative of the capillarity of the resin applied to a hairpin motor. This new method assesses—in an analytical and experimental way—the variables that interact the most and determine the quality of the impregnation process.
Register here to learn more—it’s free!
See the full sessions list for the Spring Virtual Conference on EV Engineering here.
Broadcast live April 4 – 7, 2022, the conference content will span the EV engineering supply chain and ecosystem including motor and power electronics design and manufacturing, cell development, battery systems, testing, powertrains, thermal management, circuit protection, wire and cable, EMI/EMC and more.
