Tesla spends a considerable amount of resources on basic research into EV systems – as well it should. EV technology is very young compared to that of ICE vehicles, so it’s safe to assume that, in a few short years, the aggregate of many incremental technology advances could lead to significantly better EVs.
Of course, battery technology gets the most media attention, and Tesla is constantly hustling to stay up with the state of the art. Last year Elon Musk said the company was monitoring about 60 research efforts to develop and improve batteries around the world. Tesla rates each on its long-term promise, from 1 to 5, “where 5 is ‘we should be doing business with them,’ and 1 is complete B.S.,” explained Musk. In June 2015, Tesla also signed a 5-year exclusive partnership with one of the world’s preeminent experts in Li-ion battery R&D, Professor Jeff Dahn of Dalhousie University in Nova Scotia.
So, it should come as no surprise that Tesla also has a world-class team dedicated to developing better traction motors. Among that team is Konstantinos Laskaris, Tesla’s Chief Motor Design Engineer, who is responsible for the geometry optimization and technology selection of traction motors.
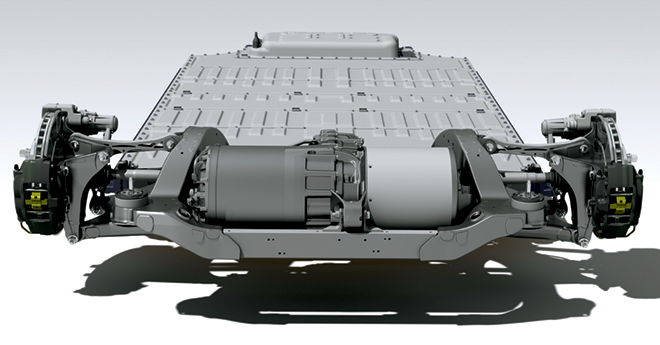
Laskaris earned a PhD from the National Technical University of Athens, Greece while studying the geometry optimization of variable speed drives. After leaving academia, he immediately joined Tesla. “Sometimes I feel like I am in my 9th year of PhD work,” Laskaris told Charged, “which is a good thing. [After joining Tesla] I was not constrained on what I would research. Of course the objective becomes different, and now you need to deliver on a company level and in a more competitive environment, but I would say that the transition was quite smooth.”
Laskaris compares research at a university to being an opera singer, relative to working at a company which is more like being in a rock band. “Tesla has a unique way of combining opera singers with a rock band,” he explained, “because it really understands the gravity of having research people.”
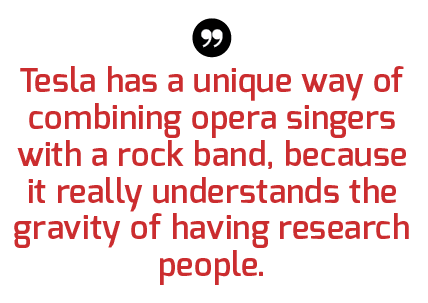
“Seeing your design going to production in a car like Model S, what could be more rewarding for a motor design engineer?” he added. “Of course the environment sometimes is very competitive. There are so many good engineers that are very involved with what you are doing. It makes sense that it is a bit stressful, but the reward is huge, because the objectives of the company are big. It makes you feel really good about your design work that your work is being appreciated.”
I had the chance to interview Laskaris for the keynote at the Coil Winding, Insulation & Electrical Manufacturing Exhibition (CWIEME) in Berlin. It was clear that Laskaris wasn’t at liberty to talk about the specifics of Tesla’s motor technology – often the case when interviewing engineers from major automakers – so I didn’t bother asking. Instead, since Laskaris sits at the forefront of determining what new motor technologies are ready for commercialization, I asked him for his general thoughts on some interesting new research areas and their near-term potential for the EV industry.
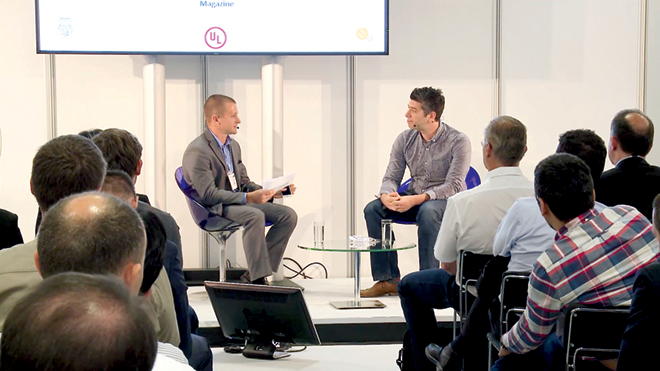
The following is a transcript of our on-stage conversation edited slightly for clarity.
Charged: We hear a lot of discussion about battery costs – historical trends and projections. Can you talk a little about the trends in motor costs?
Konstantinos Laskaris: When we’re talking about permanent-magnet motors, the magnet price in the past has fluctuated so much that maybe this is not very representative of a general discussion about motor cost.
But motor cost is going lower the more we are optimizing, and as we’re getting more power-dense motors, they get smaller. And if you don’t compromise efficiency with smaller motors and more power density, motor costs will be gradually dropping. The materials in the motors, apart from magnets, again, have a stable price.
So, we’re seeing a trend that motors are gradually becoming cheaper because of the technology improvements that we are making through the years. Also better manufacturing methods. We’re making manufacturing cheaper. If we had attempted to make the motors that we are using today twenty years ago, the cost would be much higher, obviously. There are many types of technologies that are coming to play a role here to make motor cost lower.
It’s a combined material technology and design technology evolution. For example, getting higher slot fill at the windings will effectively make the motor smaller and cheaper. Having thinner steel, which allows you to go to higher frequency, will make the motor smaller and cheaper as well.
Understanding the electric powertrain as a system is a very important thing that will drive the cost lower also. And not only the cost – it will make a better product, because knowing which operating conditions you want to optimize for, or understanding the system thermally and designing a system that takes advantage of the material capabilities but is not over-designed, is something that comes with experience and more advanced simulation techniques.
Optimization is a huge part of making an affordable car that also has amazing performance and range and all of the specifications of interest.
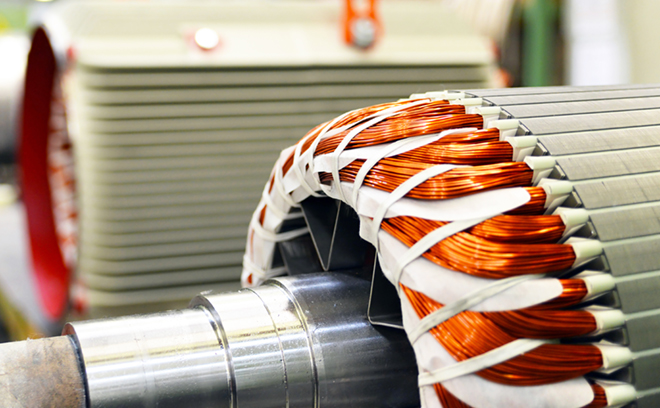
Charged: Where do you see growth in the field of optimization – is it in the software’s capabilities?
KL: It’s a combination of software capabilities – like modeling motors in an accurate way – and having more advanced modeling tools to represent motors that you don’t want to manufacture, so that you don’t make design mistakes. And then understanding what you want to optimize for, which comes from experience, how a car is driven, what a customer would like. This all leads to understanding what motor to design, and finally the simulation to show you that you have designed the right motor in the end.
Charged: Is there a technology (or set of parameters) that could be considered the Holy Grail of motor design – similar to the way that something like lithium-air battery technology is discussed (low cost, long life, high energy density)? What would that look like in the motor world?
KL: It’s motor technology and motor materials, the two components that would make the ultimate traction motor. On the materials side, I would say a core that is plastic – doesn’t have conductivity – and has got huge permeability that you can excite with very low current. [Maybe] it’s not achievable but companies are trying to get towards that direction. Then you have limits of conductivity on the materials that you can use. So these materials would get us to better performance, and we know where the ideal is from a material perspective.
But, from the design perspective, I would say that I can give an example, but don’t stick to it too much. Like a synchronous separately excited machine that has full flux regulation capability, for example, is sort of an ideal motor for controlling and performance. But it has big manufacturing challenges.
So, motor designers understand that there are kinds of motors that are designed for manufacturability and feasibility. Then there are also motors that are uncompromised but difficult to manufacture. This is why you see so many motors around.
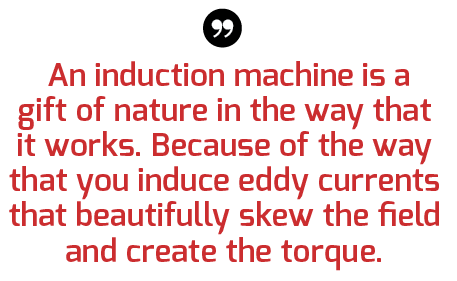
An induction machine, for example, is a gift of nature in the way that it works. Because of the way that you induce eddy currents that beautifully skew the field and create the torque. It’s something unique. You don’t have brushes, don’t have conductors, and the motor has very good characteristics. It has been around for over a century, and the fundamentals have not changed. Of course the methodology that we use has changed a lot because of computers. It’s a smooth motor. It’s a torque-dense motor.
Charged: We have put together a list of motor technologies that we’ve heard discussed as possible next-gen solutions for EVs. Could you briefly give me your thoughts on each? (i.e. do you think the technology is promising, too challenging to implement, too expensive for your desired product roadmap for the foreseeable future, solves a problem that doesn’t need to be solved, etc.)
First, advances in nanomaterials have shown the potential for improvement in the electrical and thermal properties of metallic conductors, reducing stator and rotor I2R losses. What are your thoughts on high-performance thermal and electrical conductor manufacturing?
KL: Reducing the copper losses of windings is something that practically everyone is trying. It’s so dominant and obvious, and if we get higher conductivity that is beyond what copper can do, it will be groundbreaking and significant, not only for Tesla, but for everyone that is manufacturing motors.
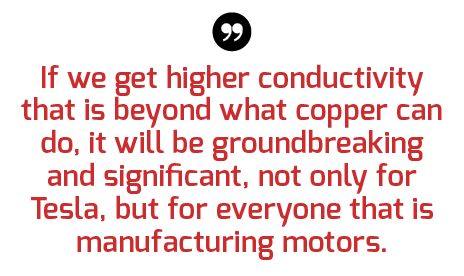
If it happens, we will know it very soon and it will be adopted. So far there are very few materials, though. Silver is the most conductive material you can find, but it’s way more expensive than copper. This is why copper is dominating in most cases. But I will be excited to see evolution there.
I am seeing some companies doing work, but they’re also trying to improve the mechanical characteristics at the same time. I have not seen something yet that will be directly implementable in the foreseeable future.
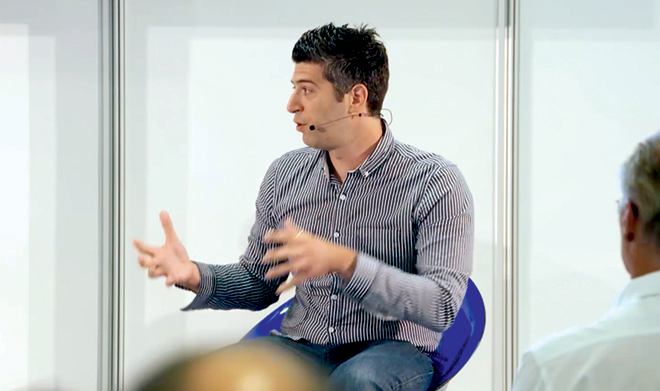
Charged: Electrical steel with 6.5% added silicon has been shown to reduce core losses without sacrificing saturation magnetization level. What are your thoughts on silicon steel manufacturing?
KL: Getting lower-loss steel gradually allows you to change your design considerations and go to higher frequencies and get the motors smaller. For example, if you have an 8-pole machine at a certain frequency, if you had lower-loss steel you could go for a 10-pole machine and then you get more torque density. So, effectively, you can trade iron loses with torque density. So there are all these design tweaks you can do and redesign a motor to give you a better product in the end.
There are companies that are doing higher silicon contents. It requires a lot of energy and it’s difficult to drop the cost, because energy has a given cost. But we will see, we are interested to see the evolution for sure.
Charged: Breakthroughs in high-temperature superconductors make it possible to eliminate rotor resistance losses and enable higher flux densities. What are your thoughts on superconducting wire manufacturing?
KL: That is a bit further away for the vehicle industry, because the cost of cooling has to outperform the cost of the efficiency benefit or the compaction benefit that you’re getting. So maybe the traction application for electric cars is, at least for now, not the right application. It’s better for applications that require more continuous power density.
Charged: What do you think about the state of low-loss and high-speed bearing technology?
KL: Higher speed is one of the two ways to increase power density. One is torque density, and one is speed. And high speed is limited by mechanics – like structural, bearing and gears. So bearings are sometimes one of the limiting factors to go to as high a speed as we’d like. And getting cheap bearings that can withstand higher speeds is definitely something that we are looking forward to. I think this is applicable for traction applications.
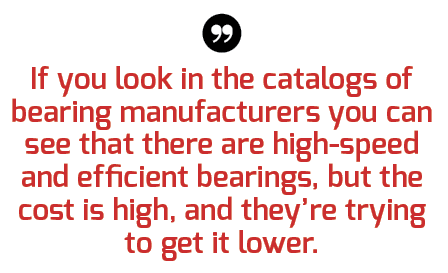
If you look in the catalogs of bearing manufacturers you can see that there are high-speed and efficient bearings, but the cost is high, and they’re trying to get it lower. We’re excited to look at the results and to assess if some better bearings are attractive solutions for drive units.
Charged: What are your thoughts on using soft magnetic materials to make motor cores – such as amorphous, nanocrystalline and soft magnetic composites (SMC)?
KL: Amorphous provides a very good tradeoff between saturation and losses, but it has limitations in manufacturing. We’re not there yet to see a wide range of commercial motors, although I know some companies that have done prototypes with amorphous steel.
Silicon steel is a very good deal for now, between losses and saturation level as well. For radial flux machines, that might be the direction.
SMC allows the field variation to mitigate iron losses when you have a 3D field variation in the core, like when you have transverse flux machines or axial flux machines. But again, there might be a bigger compromise between saturation and iron loss there. So I think that silicon steel evolution is something that the automotive industry is looking forward to.
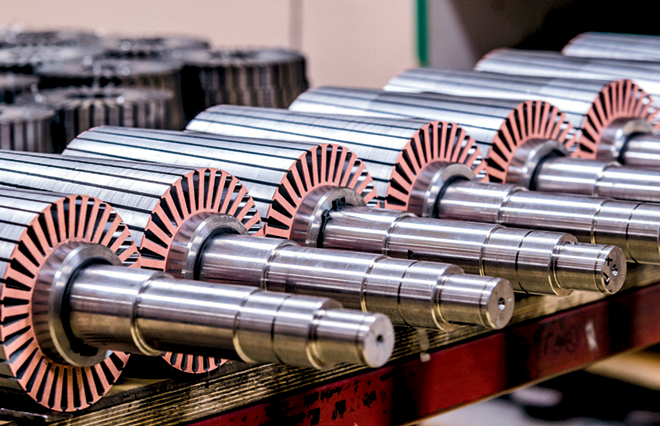
Charged: What are your thoughts about new techniques for active torque ripple minimization?
KL: I prefer optimizing the geometry to not have torque ripple in the first place, rather than trying to mitigate that with controls. I think there is a lot that can be done optimizing your geometry not to have torque ripple. It’s something that you can capture pretty easily with finite elements. And if you need to do active mitigation, then you have a bandwidth limitation, because the frequency gets high. So I believe that torque ripple should be addressed by hardware tweaks that will mitigate the torque ripple.
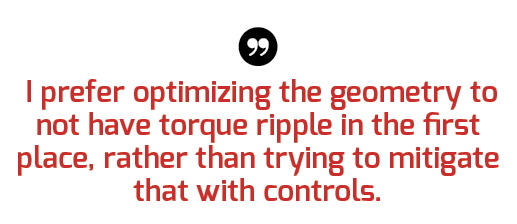
Charged: There is a lot of talk about switched reluctance machines (SRMs) as a possible next-generation EV traction motor. Do you have any thoughts on SRMs?
KL: An SRM is a very particular machine. It’s very simple to manufacture, but it’s difficult to control. It’s got some acoustic noise and vibration challenges. With design you can make it a lot better, and you can control it in a way that you mitigate all these problems.
It is not too bad in torque density, but the constant power is a bit of a challenge to build up, and you need constant power in traction applications. So, again, I’m always hoping to see new ideas and definitely it’s attractive to have something that is so robust because it’s a very simple rotor construction. It could potentially work for this class of problems.
Charged: For young engineers who want to make an impact on the EV industry, what specific areas of technology do you think they should focus on? What do you think are the most impactful technological challenges that get the least amount of attention?
KL: I would say, don’t underestimate the classic sciences first – a good math background, good physics background. It’s always a trend. You will always make good use of your understanding. If you learn how to use commercial tools for design you will be more ready for the industry, but it’s much better to have a good theoretical background.
After that, motor controls is a topic that has a bright future. But I would say that someone who will design good motor controls in the future also needs to understand motors very well. There are people who want to do motor controls before studying electric motors in the first place, and that’s something that I would not recommend.
Electrical energy storage systems are also exciting. It’s a field that has a lot of research opportunities.
And of course, software engineering and writing code. You will do great if you know how to put your thoughts as an engineer into code. Once you start having your own imagination and ideas it’s a huge advantage. I would say that having some programming skills is definitely very important.
This article originally appeared in Charged Issue 30 – March/April 2017 – Subscribe now.