The principal motor engineer at Tesla describes why modeling and optimization is so vital to its design process.
Creating a start-of-the-art electric vehicle requires a deep understanding of all the components. More importantly, it requires a continual process of analysis and optimization of the components to push the limits of driving range, efficiency, performance and cost reduction. The internal combustion engine has had the benefit of millions of man-hours in engineering analysis and refinement over the past century, while the collective engineering effort of the EV industry has just begun.
It comes as no surprise that Tesla, the EV trailblazer, spends a considerable amount of resources on internal R&D to develop better parts for EVs, and that its testing facilities and engineering talent are at the forefront of the industry.
As Tesla’s Principal Motor Designer, Konstantinos Laskaris is responsible for the electromechanical design and optimization of the company’s existing and future traction motors. Before joining Tesla, Laskaris earned a PhD from the National Technical University of Athens, Greece. There he combined advanced methodologies and developed algorithms for motor geometry optimization.
Charged recently chatted with Tesla’s motor guru to learn more about the process the company uses to continually evaluate and optimize motor design choices.
Charged: In general, how are electric motors inherently better for traction applications than combustion engines?
Laskaris: When you simply compare any other high-end conventional car to a Tesla, you see a tremendous difference. This is because of the technology.
As for the motor, specifically, there is a huge efficiency advantage, and it is extremely quiet and vibration-free, with very high power density and instantaneous direct response to inputs. All these characteristics of electric motors give an unparalleled performance advantage.
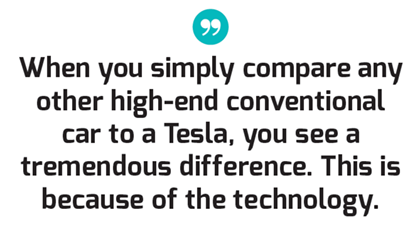
This is why it was so important for Tesla, as a company, to break the stereotype that’s been out there for years. People needed to see that performance, efficiency and range can coexist in an EV. The dual-motor powertrain Model S is the fastest sedan that has ever been mass-produced. The total motor power exceeds 700 hp, and it spins as fast as 18,000 rpm – speeds that we previously only found in Formula 1 racing vehicles.
You could say that the electric motor is magic from the perspective that it awakens the soulless car.
Electric motor cutaway on display at Tesla headquarters in 2013 (Windell Oskay – CC BY 2.0)
Charged: When Tesla decides to change a parameter of its vehicles – like increase the peak battery current or add towing capacity – what does that mean for your motor design team? Do you have an iterative design process?
Laskaris: At our factory in Fremont, we manufacture practically every aspect of the car in-house. We have a motor winding and manufacturing facility, so we can optimize every aspect of our motor manufacturing and control the quality of the product. Also, we can implement changes in production very fast, we’re a very agile company from that perspective.
We can generate motor geometries and analyze them with finite element analysis very quickly. We have a big computer cluster with more than 500 core processors that run finite elements – a typical personal computer has two cores, maybe four. That means you can create many virtual models in parallel and do a very large number of calculations. Basically it allows us to solve the loss and efficiency maps very fast and see – according to any metrics that we created – how good any motor design is for an application we’re designing for.
Charged: There seems to be an endless array of electric motor topologies, architectures and configurations. How do you begin to evaluate and compare all of the possible options?
Laskaris: Understanding exactly what you want a motor to do is the number-one thing for optimizing. You need to know the exact constraints – precisely what you’re optimizing for. Once you know that, you can use advanced computer models to evaluate everything with the same objectives. This gives you a panoramic view of how each motor technology will perform. Then you go and pick the best.
With vehicle design, in general, there is always a blending of desires and limitations. These parameters are related to performance, energy consumption, body design, quality, and costs. All of these metrics are competing with each other in a way. Ideally, you want them to coexist, but given cost constraints, there need to be some compromises. The electric car has additional challenges in that battery energy utilization is a very important consideration.
Everyone will have a different perception of what tradeoffs should be made. How much driving range are you willing to trade for faster acceleration, for example? Once these parameters are set, you can begin to evaluate options and optimize.
Charged: You have a background in creating the algorithms that allow computers to simulate how a motor will function in the real world. How do these simulations translate into better vehicles?
Laskaris: The mathematical modeling technology, or methodology, that you use is very important and has tremendous impact on the success of electric vehicles. When I say “modeling,” I mean to understand the mathematical principles behind a system and then create software tools that will represent accurately how it will act in the real word.
Tesla’s electric motor rotor in 2007 (Tinou Bao – CC BY 2.0)
Accurate motor modeling is so important because through it we can evaluate a hypothetical motor before we produce it – the losses, performance capabilities, torque ripple, thermal management, and anything that we are interested in to classify how good or bad is a motor. And, in this way, we avoid unnecessary prototypes and unpleasant surprises.
Beyond that, through good motor modeling, we can achieve the best optimization – which means we can achieve exotic performance without the use of exotic materials and exotic manufacturing methods.
Optimization is the art of being able to navigate through different motor candidates to see what is good and what is bad, and by how much. As you begin to do optimization, you realize that without good modeling, it is meaningless. This is because the process would be based on a bad representation of the motor, and in the end the motor wouldn’t be truly optimal.
Charged: Could you give us an example of some tradeoffs that you would use modeling to optimize for?
Laskaris: Yes. A large portion of the time people spend driving is in low-torque highway situations. However, there are a lot of motors that offer great 0-60 MPH performance but are very inefficient in the low-torque highway-speed regions. So the question is, can I have everything – both high efficiency and high performance? The answer, unfortunately, is no. But you can make intelligent choices between things that are competing with each other.
This is the beauty of optimization. You can pick among all the options to get the best motor for the constraints. If we model everything properly, you can find the motor with the high performance 0-60 MPH constraint and the best possible highway efficiency.
Another example is the overall motor efficiency versus its cost. There are cases where making a motor in more expensive ways could potentially increase efficiency and buy off multiple times the cost difference by saving money on the battery, or other aspects of the car. So, if you are able to model the motor efficiency and costs accurately, you can plot it against battery cost savings. Now you can see that the optimal motor for total cost minimization is often different from the cheapest motor.
These all come together to form the characteristic metrics of the car that you want to build. It’s a general approach of how we start from parameter design and end up with ultimate configuration.
Charged: At what point do you perform physical prototype tests to verify the results from your virtual models?
Laskaris: We do many verification tests before there is even a prototype for a specific application. They are what we call characterization experiments. And they allow us to get a known correlation point and to see if the isolated modeling tools are in sync with reality. So it’s a back-to-back comparison between what the model predicts and what is actually measured. It might not even resemble a motor, it might just be a piece of iron spinning, for example.
We then, of course, build and test full prototypes as well.
MORE: Tesla’s chief motor engineer discusses the potential of next-generation motor technologies
This article originally appeared in Charged Issue 21 – September/October 2015. Subscribe now.