Researchers at the University of Michigan have developed a streamlined approach to testing new battery designs which they say could cut the time for both simulation and physical testing by as much as 75%.
The new study, “A generic battery cycling optimization framework with learned sampling and early stopping strategies,” was published in Patterns-Cell Press. The research was funded by LG Energy Solution.
“The goal is to design a better battery, and traditionally the industry has tried to do that using trial-and-error testing,” said Professor Wei Lu, leader of the research team. “It takes such a long time to evaluate.”
As the researchers explain, parameters involved in battery design include everything from the materials used to the thickness of the electrodes to the size of the particles in the electrode. Testing each configuration usually means several months of fully charging and then fully discharging (cycling) the battery as many as 1,000 times to simulate a decade of use. It is extremely time-consuming to repeat this test through the huge number of possible battery designs to discover the better ones.
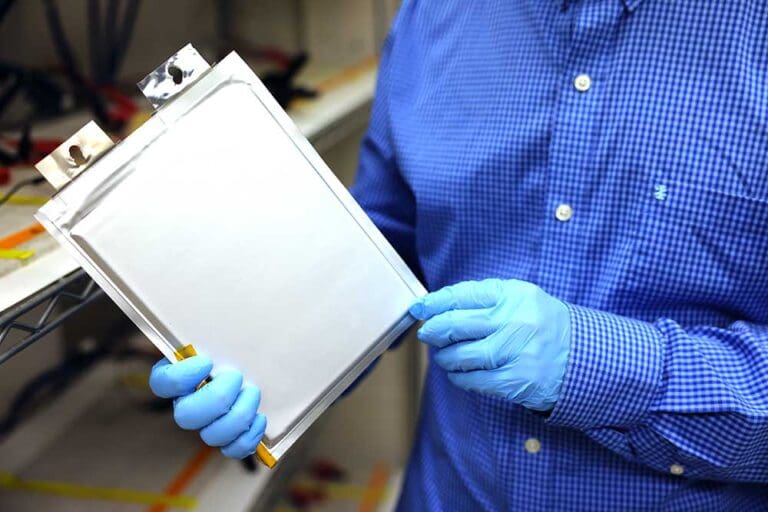
“Our approach not only reduces testing time, but it automatically generates better designs,” Lu said. “We use early feedback to discard unpromising battery configurations rather than cycling them till the end. This is not a simple task, since a battery configuration performing mediocrely during early cycles may do well later on, or vice versa. We have formulated the early-stopping process systematically and enabled the system to learn from the accumulated data to yield new promising configurations.”
U-M engineers used the latest in machine learning to create a system that knows both when to quit and how to get better as it goes. In addition to cutting off tests that lack promise, U-M’s system generates multiple battery configurations to be tested at the same time, a process known as asynchronous parallelization. If any configuration completes testing or is discarded, the algorithm immediately calculates a new configuration to test without the need to wait for the results of other tests.
“By significantly reducing the testing time, we hope our system can help speed up the development of better batteries, accelerate the adoption or certification of batteries for various applications, and expedite the quantification of model parameters for battery management systems,” Lu said.
Source: University of Michigan