Tesla has devised a new wiring architecture for its vehicles
that could greatly streamline production. The new wiring system is designed to
allow robots to handle more of the assembly process.
One of the main reasons for the highly-publicized delays in early production of Model 3 was that Tesla tried to introduce too much automation, using robots to perform tasks to which they aren’t well suited, such as manipulating cables.
Tesla has been addressing this issue by reducing the length of the wiring harnesses in its vehicles. Elon Musk recently said that Model S has about 3 kilometers of wiring harnesses, whereas Model 3 has only 1.5 kilometers. Using the new wiring architecture, Tesla hopes to bring that figure down to a mere 100 meters in the upcoming Model Y.
A recently filed patent application (via Electrek) reveals some details of the new system:
In this new wiring architecture, subsystems are packaged and defined in one or multiple assemblies in certain embodiments. For example, a door assembly might contain one controller (or hub) that controls multiple devices, such as locking components, lighting components, audio components, etc. In addition to decreasing the number and length of wiring needed, the ability to create these subassemblies and then connect them to the wiring-architecture backbone will decrease assembly time during general assembly, which is very desirable to increase productivity in a vehicle manufacturing process. The subassembly may be created ahead of general assembly with only the connection between the door subassembly and subsystem made and verified during general assembly.
Tesla also explains some of the problems with the traditional wiring harness:
Traditional car wiring for vehicles are piecemeal solutions [sic]. Typically, there are different wiring harnesses that connect each different electrical component to a central battery or power source. Each component receives power, but requires multiple wiring harnesses for communication and signals. The total length of the wire may be many miles within a single vehicle. These wiring harnesses typically consist of multiple round conductors that are not rigid. Round conductors are not optimal for transmitting current and the lack of rigidity of traditional wiring harnesses requires assembly into the vehicle using human hands, which can be a slow process. Further, connecting each component to the central battery is not optimized on an automobile level.
To the average car buyer, an improved wiring harness may seem like an insignificant detail, but as Electrek put it, “This looks like a big deal.” It’s yet another upgrade to Tesla’s “machine that builds the machine.” More automation means savings on labor costs, production time and factory floor space, which should ultimately translate to lower prices and/or higher margins – good news for Tesla and its customers.
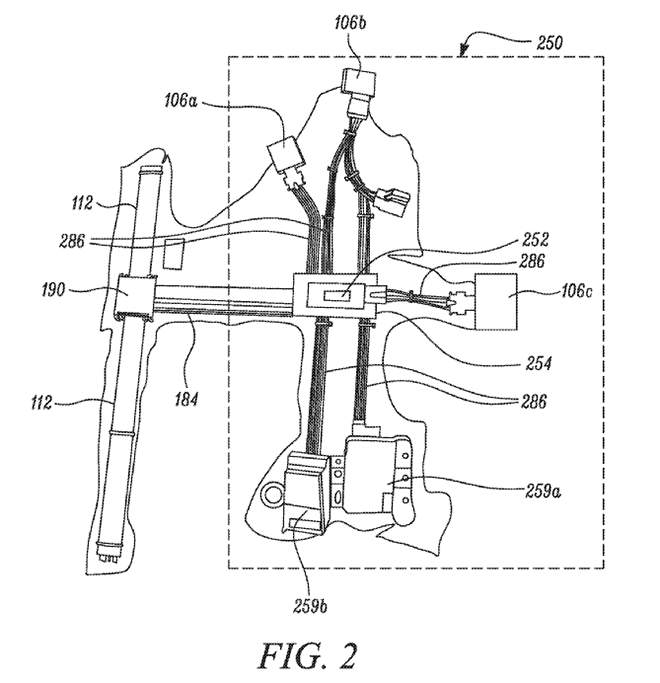
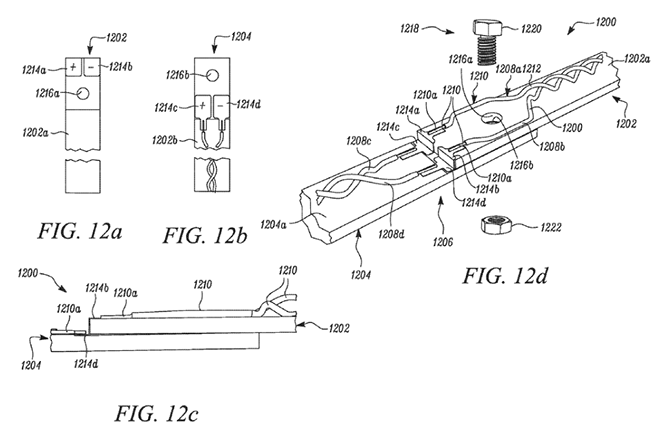
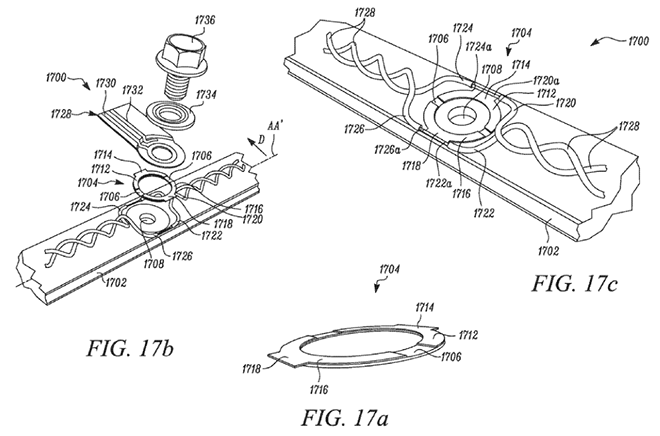
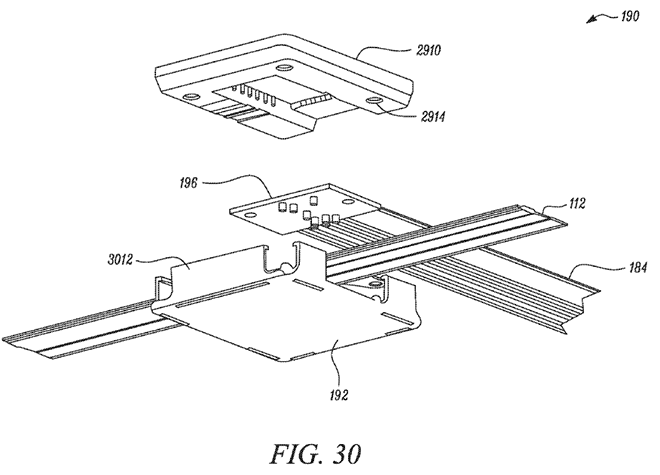
Source: Electrek