Sponsored by Hesse Mechatronics
Benefits of Smart Welding
There are many types of welding used for the interconnection of battery packs. Laser, resistance, spot, etc. are just a few of the common types. Smart Welding was developed by Hesse Mechatronics to offer an alternative option. Smart Welding is “wire bonding without the wire” as it continues to use ultrasonic energy to help form the interconnection. The benefits of Smart Welding is that you have a lower cost of ownership when comparing to wire bonding since you do not use wire, wire guides, cutter blades, and you don’t spend the time setting up the bond head or changing wire spools.
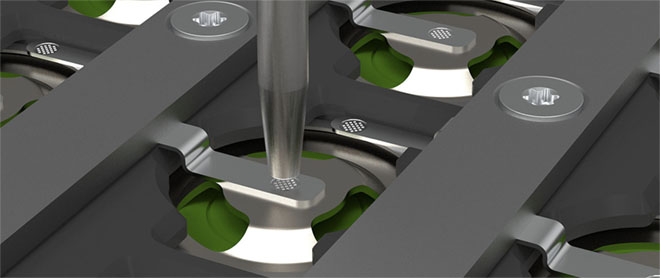
Smart Welding is a room-temperature process. One primary concern with laser welding is the potential for excessive heat to penetrate the negative terminal and cause thermal runaway, which will lead to catastrophic failure.
PiQC
Hesse’s patented PiQC (Process Integrated Quality Control) is one of the components that makes this a “smart” welder. We monitor up to five variables during the interconnection process. No other welder on the market has such sophistication. If the PiQC sensor detects a quality index less than the set threshold, the machine could stop or send a signal to the barcode notifying that the specific bond needs further review. Figure 3 displays a PiQC screen-shot.
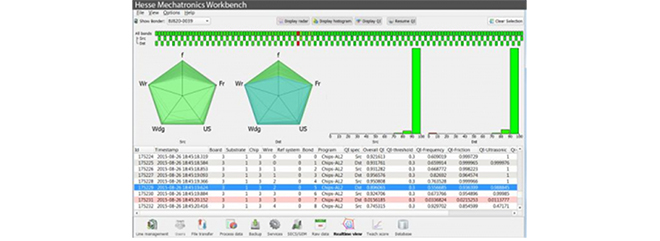
Cell and Busbar Metallization
Ideally, the busbar material should be aluminum. Al1145 is the best type. Other Al types such as 3003, 5052, or 6061 will suffice. If you use a Cu busbar, you will have to clean the Cu before wire bonding due to the oxide layer, or you may plate it with ENIG (Electroless Nickel Immersion Gold) or ENEPIG (Electroless Nickel Electroless Palladium Immersion Gold). These are off-the-shelf chemistries that are excellent for Smart Welding. Refer to the IPC specifications for 4556 and 4552. All busbar material should be half-hard temper. The overall thickness of the tabs that will get ultrasonically attached to the cylindrical cell should be .3mm thick and 1mm thick, depending on the current generated.
Summary
There are many ways to interconnect cylindrical cells in a battery pack. Wire bonding is common because it has a lower cost of ownership model than laser welding. Smart Welding would even have a lower cost of ownership than wire bonding, but the busbar needs a different design. One key issue is that Smart Welding is a room-temperature process and that no external heat gets generated. One primary concern with laser welding is if excessive heat penetrates the negative terminal, the cell could go into thermal runaway. Resistance welders have little to no in-line process monitoring. Smart Welding will be safer and provide real-time quality data on your interconnections.
Hesse Customer Solutions is another Hesse division that offers production service for wire bonding or smart welding of battery packs and other microelectronic devices. Also, Hesse Customer Solutions provides process support, online support, training, and cost of ownership reviews. Contact us so we could discuss your application with you. https://www.hesse-mechatronics.com/en/customer-solutions/
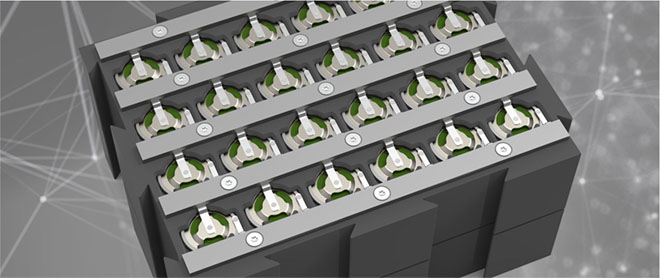
Hesse Mechatronics is a manufacturer of wire, ribbon bonders, and Smart Welders. For more information, please contact sales@hesse-mechatronics.com