Li-Metal, a Canada-based vertically integrated battery materials company, has announced the successful production and shipment of its first batch of lithium metal ingots. These were produced at Li-Metal’s recently commissioned lithium metal reprocessing and casting facility in Markham, Ontario, which has the capacity to process up to 15 metric tonnes of anode scrap material per year.
Lithium metal anodes are produced either through a conventional extrusion/rolling process, or through a physical vapor deposition process, which Li-Metal is working to commercialize in conjunction with its exclusive manufacturing partner Mustang Vacuum Systems.
According to Li-Metal, battery gigafactories can have up to a 30% metal scrap rate. Lithium metal ingot manufacturing scraps are currently designated as hazardous waste, and are typically incinerated, sending critical battery materials up the smokestack.
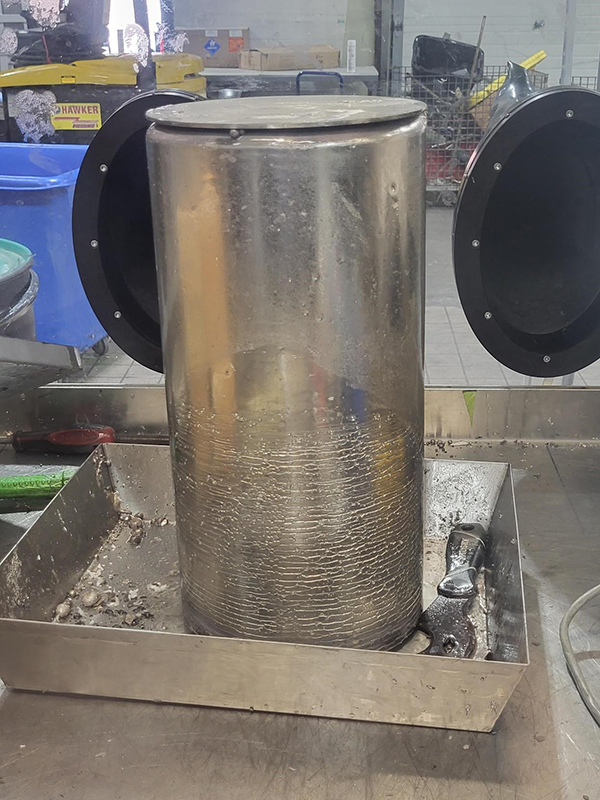
To enhance the sustainability of lithium metal anodes and to overcome the need to incinerate scrap lithium metal, Li-Metal developed a novel reprocessing and casting technology. The company’s technology reprocesses the scrap lithium into ingots that can be used for anode production.
As Li-Metal advances its lithium metal reprocessing program and demonstrates the continuous production of lithium metal ingots, the company is evaluating scrap samples from multiple partners to scale capacity. Li-Metal’s aim is to leverage the pilot facility and know-how generated during the scale-up of the reprocessing facility to help partners produce high-purity lithium-alloy ingots for battery producers.
“The ability to produce lithium metal products is a key differentiator for Li-Metal’s positioning in the next-generation battery ecosystem,” said CEO Srini Godavarthy. “This is an important milestone in our roadmap as we advance our technologies and plan to become a leading vertically integrated domestic supplier of lithium metal and high-performance anode materials.”
Source: Li-Metal