Continental has introduced a 30 kW, 48-volt high-power drive system for full hybrid vehicles, which it says is cheaper than the high-voltage systems used up to now.
Until now, manufacturers have typically used 48-volt systems in “mild hybrid” vehicles, in which the electric motor doesn’t drive the vehicle directly, but only assists the ICE. Full hybrid vehicles can drive on electricity alone, but typically need high voltages – up to 800 volts. Continental says its engineers have developed a 48-volt hybrid system that boasts features similar to those of a high-voltage electric drive and can drive vehicles without help from an ICE.
The 48-volt high-power system is comprised of an electric motor, integrated power electronics, and a battery. Continental says it reduces fuel consumption and CO2 emissions by around 20% compared to similar ICE vehicles.
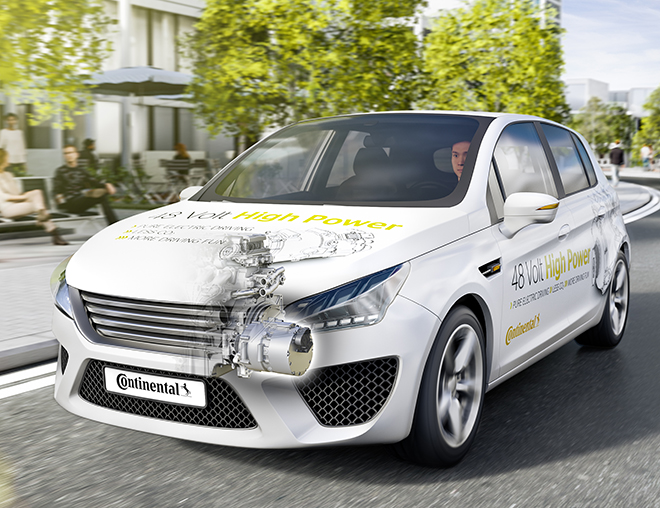
In the latest stage of development, Continental engineers repositioned the 48-volt system from in front of the ICE on the crankshaft to behind it, between the combustion engine and transmission (P2 hybrid). The key component in the system is a new water-cooled electric motor with a peak output of 30 kW, double that of previous versions. Continental says that electric-only driving is possible up to a speed of 80 to 90 km/h.
The company also says the 48-volt system delivers a lower cost than high-voltage systems, as it requires less insulation protection and electrical components are smaller and cheaper. The system is also more compact because it requires smaller gaps between the individual components.
“With the new hybrid system, we are making the most of what is currently technologically possible for a 48-volt system,” said Stephan Rebhan, head of Technology and Innovation at Continental’s Powertrain business.
Source: Continental