Can a company that’s 100 years old be called a startup? Mary Petrovich, Executive Chairman of AxleTech, certainly thinks so. AxleTech was founded in 1919 as Wisconsin Custom Built Axles, and has seen a century’s worth of sales, acquisitions, and rebrandings since then. Petrovich herself brought AxleTech back from the brink of failure not once, but twice – and now she’s at it again. She’s repositioned the company in the technology space, and AxleTech is now smack-dab in the middle of the EV industry.
“If you think about us today, we are very much a technology company,” Petrovich says. “We are what you might consider a hundred-year-old startup.”
Though AxleTech has had to bring in new recruits to aid its electrification effort, the company’s hundred years of experience in suspension, brakes, wheel ends, gearing and drivetrains has proven advantageous.
“We’ve been developing everything in between the wheels for the last hundred years,” says Jay DeVeny, AxleTech’s VP of Engineering. “And to do that with a motor now, and the inverters, and the power controls, and shifting pieces, that actually comes quite naturally for us.”
AxleTech has partnered with a number of powertrain manufacturers, including Proterra, TM4 and Wrightspeed, to develop custom electric powertrain systems for heavy-duty EV applications, including Class 8 refuse trucks and Class 7 buses. Through these projects, AxleTech has fine-tuned its EV products, developing what it now considers its third generation.
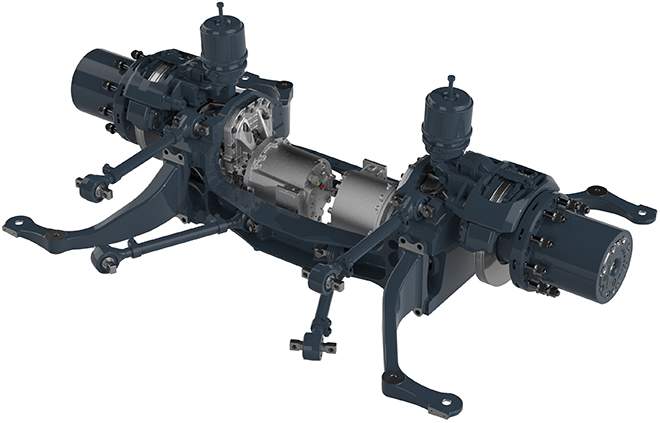
It’s all about the battery
One of the key factors in AxleTech’s pivot to electrification has been the standardization of battery technology, according to Jay DeVeny.
“When we were first getting in these projects, they were looking at ultracapacitors, nickel metal hydride batteries, sodium batteries…all of that has really standardized on lithium-ion,” DeVeny explains. “It’s the VHS of batteries. It may not be the best at everything, but it’s a lot less expensive than the Betamax. Betamax is much better in a lot of other ways, but the standard was VHS. And from our perspective we’ve seen lithium-ion become that, where it just makes it economical for these vehicles. And that’s really been the driver of the big electrification effort that we’ve seen over the last four years. It’s all about the battery.”
Petrovich saw the opportunity presented by the burgeoning EV industry, and knew AxleTech could position itself as a market leader. But to do so would require some big changes to the company, as she explains.
“To give you an idea of how focused and how committed we are to the electric vehicle space in particular, we have increased our engineering by 70 percent over the last several years,” Petrovich says. “We brought on new skill sets that we didn’t have before – folks that understand transmission, people that have expertise in powertrain as opposed to just drivetrain, and the software and controls engineering capability. We have filed more patents in the last twelve months than we have in the last decade, and that is in great part due to the electric vehicle innovations that we’ve made.”
Electric axles
“We’re into our third generation of axles for the bus and truck market now,” DeVeny explains. “We’ve really condensed everything so that the whole powertrain is in between the wheels. All of the motors, the gearing, suspension pieces, what you traditionally had with a very long traditional drivetrain. That’s what we call our north-south configuration, which is a diesel engine, transmission, and then running into a T of an axle. With electrification you’re able to rotate that around and go what we call east-west, and have everything basically packaged between the wheels.”
“But it’s not grassroots for a specific customer, it’s a product line that we can adapt to various vocations and various needs,” adds Petrovich. “So I think we’re one of the very first if not the only axle player to have that capability.”
AxleTech’s electric powertrain systems are focused on two markets: low-floor buses and medium-to-heavy-duty trucks, both fully electric. “The first ones to electrify are the first ones that make sense economically,” DeVeny says. “And those are the city delivery type of vehicles, drayage vehicles, vehicles that are depot-oriented and come back to that depot at night so they can be charged.”
Long-haul trucks, DeVeny believes, still require some improvements in battery technology before they’re economically viable. And as for hybrid electric vehicles, DeVeny sees fully electric vehicles as a much better option.
“I personally view that the hybrid was a transition stage, and it’s quickly being obsoleted,” he says. “In 2010 batteries were $1,000/kWh, and we see that going below $150 over the next couple of years. That’s an order of magnitude drop over eight years. And so I think when you look at the complexity and cost of a hybrid system, a fully electric system just makes a lot more sense. Many fewer parts, and little to no maintenance compared to traditional internal combustion engines.”
For the low-floor bus market, the move to electrification has been able to solve an annoyance that traditional buses have long suffered from: the rear axle requires the bus floor to be raised at the back.
“What we see with electrification is you’re able to get that to be a low-floor bus,” DeVeny explains. “Basically the floor from the front to the back of the bus is the same height. And that gives bus designers and transit authorities a lot of flexibility, because you can add another door at the rear. And that really helps with ingress and egress.”
For the truck market, AxleTech has found a sizeable variety of customers, even given the small size of the city delivery and drayage market.
“We very quickly came to the conclusion that we would need to work within the existing chassis and suspensions that are out there to provide an electric powertrain. There’s a multitude of body types and suspensions that are in that market. And we needed to be able to provide that type of packaging and interface with the existing platforms while still replacing the traditional diesel transmission prop-shaft configuration,” DeVeny says.
A systems engineering approach
To properly take on the challenges required in powertrain design, AxleTech has adopted a systems engineering approach, according to DeVeny. “You can, in a simple way, just take out the diesel engine and transmission and put a big electric motor in front of it. But that’s not the best way to do it.”
AxleTech’s customers have a few crucial needs, all of which need to be considered in powertrain design: a high load capacity, the capability to go up steep grades, the capability to attain a decent speed, and, of course, efficiency. Balancing all these requirements is exactly why AxleTech has taken a systems engineering approach, and it seems to have paid off: with Proterra, AxleTech recently helped set the world record for longest distance travelled by an EV on a single charge: 1,100 miles.
“We showed with the Proterra system, by taking that system-level approach and really thinking about what you’re trying to achieve, you come up with the optimal type of system,” explains DeVeny. “If you look at how far Proterra advanced with the distance, it was over 20% from the prior record holder. And I attribute that to that systems-level approach.”
Whatever the reason, AxleTech has undoubtedly found success with its pivot to the EV industry. The company’s collaboration with Wrightspeed is in early production, it will be running production systems for Proterra by the third quarter of this year, and in the next 24 months will see what Petrovich calls a rapid-fire succession of programs come into production.
“It’s going to be a big part of our growth engine, and we think it could essentially double our revenue, or help us get most of the way there in the next 24 months,” she says.
This article originally appeared in Charged Issue 36 – March/April 2018 – Subscribe now.