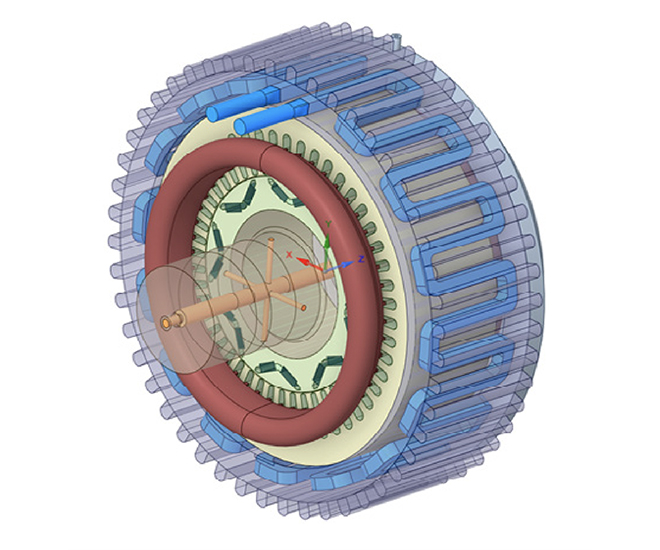
EV designers must address an increasingly complex matrix of engineering goals on tightening timelines. Optimized system design requires evaluation of many different concepts, topologies, and electronic interactions across disciplines. Considering the traction motor alone, there are several design decisions that impact the function of the entire vehicle. Engineers used to perform electromagnetic analysis in bits and pieces using their own calculations and programs, and, for a long time, that was a suitable solution. Today, engineers need simulation and regular prototyping throughout the design cycle. Implementing simulation workflows can improve power density, energy efficiency, and operational life while meeting design requirements, industry standards, and safety regulations.
Learn how simulation and optimization techniques can be used to address system-level multiphysics complexities to condense design cycles of high-performance electric traction motors. This whitepaper examines motor types, winding technology selection for PMM, and cooling types plus key technology considerations.
Download the full whitepaper from ANSYS
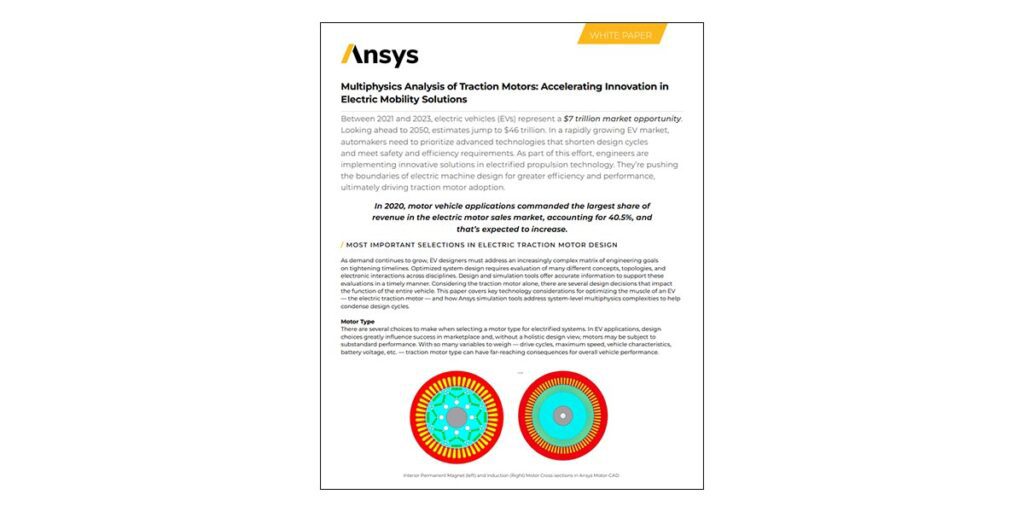