Sponsored by Nordson Sealant Equipment
Nordson Sealant Equipment is in Wixom, MI, USA and specializes in automated sealing and dispensing for 1-part and 2-part materials used in electric vehicle battery cell manufacturing. Nordson designs and manufacturers meters and valves to precisely dispense sealant and adhesives materials. We proudly partner with most of the top 10 automotive manufacturers globally to enhance their vehicle production. Our leading engineers can provide dispense solutions tailored to a customer’s top priority. Whether it’s EV battery back bonding or sealing battery modules our technology will save you time and money.
Nordson helps EV battery customer save thousands
Nordson recently met with an existing customer who was looking to increase their production rate in a specific EV battery manufacturing cell. The customer’s current process was dispensing 600 individual 0.3cc shots per battery module totaling 173cc total volume. The entire process took 450 seconds, or seven-and-a-half-minutes to complete. This affected the customer’s production output and their integrator determined that to meet the customer’s target cycle time of 240 seconds they would require a second line to achieve the target production rate. The current seven-and-a-half-minute duration also caused the sealant to cure before the assembly was complete. These challenges had to be resolved or their production would suffer in time and product costs.
Our team of experts met with the customer and integrator to understand their target process. The customer needed to decrease their cycle time from seven-and-a half-minutes to 240 seconds, or four minutes altogether. They still wanted 600 individual 0.3cc shots per battery module with a total of 173cc volume per part. The weight of the battery module and speed were incredibly crucial to the performance of the vehicle. We knew the only way to improve this process was to replicate it.
Our solution exceeds customer’s target
First the customer took advantage of our onsite material testing lab in Wixom, MI. They shipped us their parts and material, so we could replicate their current process in-house. Our engineers quickly started testing the material properties, bead size, and cycle time. This data would allow Nordson to provide the customer with the best solution. The material testing lab can take up to two weeks for a thorough analysis but can save thousands for a customer.
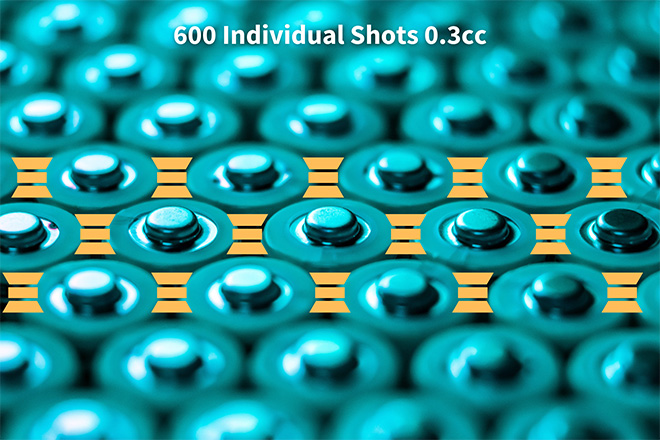
Throughout the testing phase our engineers discovered that the robot was the biggest impact to the cycle time. The robot had to move, stop, dispense, and then move repeatedly to individually dispense the 600 shots accurately. Our engineers decided to alter the shape of the 0.3cc individual shots to a 4.5cc continuous bead to speed up the total dispense time. This solution allowed each battery module to only need 18 continuous beads versus 600 individual shots. The new continuous beads decreased the material usage and weight of the battery in half, from 173cc total volume to 81cc total volume per part. The customer was able to incur a 50% material savings. The entire dispense process only took 65 seconds to complete which surpassed the customer’s goal of 240 seconds. The one minute and five second solution was seven times faster part throughout and eliminated the need for a second line, saving the company thousands. The customer was in astonishment when we shared our findings with them and were quick to implement the new dispense process into their production line.

(3) Common mistakes in EV battery cell manufacturing
How can OEM, automotive manufacturers, or even you improve your EV battery pack assembly? Nordson has learned what mistakes you could make that can cost a manufacturing plant time and money. There are three common mistakes: choosing the dispense equipment last, not testing your material, and wanting the fastest research and implementation timeline when assembling an EV battery cell and pack.
The first common mistake is choosing the dispense equipment last. Most OEM and automotive manufacturers begin the research process by contacting a material supplier. Then, they spend a week or two discussing their product and the ideal adhesive or sealant. Once the OEM or auto manufacturer has analyzed multiple materials with a material supplier, they select one. Next, they contact various equipment manufacturers and focus solely on the material chosen and the application needed. The problem is their production output may be impacted. OEM and automotive manufacturers end up paying for a system that simply dispenses the chosen material the best. What they don’t think about is how that material can affect their equipment over time. The equipment may meet their production specifications i.e., speed, accuracy, and volume, but what about the cost of replacement parts, or cost of frequent downtime? The material chosen could be abrasive and wear down the equipment faster than intended. The material may not dispense easily and can cure in hoses and pumps over time causing an increase in unwanted cleanout and downtime.
The second common mistake is not testing material options with the preferred dispense equipment. As we previously mentioned, most OEM and auto manufacturers select the material first then search for dispense equipment. This can narrow their search options for dispense equipment. If OEMs and auto manufacturers searched for material suppliers and equipment systems at the same time they could improve their process and save costs. At Nordson when we provide a customer with a solution, the material is an incremental step in selecting the equipment. Therefore, we test all the materials they are contemplating and ensure it does not diminish the quality of their EV battery pack. We analyze durability, abrasiveness, volume, application, line speed, cycle time, material usage and anticipated part life time. All these factors impact a customer’s bottom line. Our goal is to make sure they invest in the right equipment and material to maximize their income and ensure they deliver a quality product to their end customers.
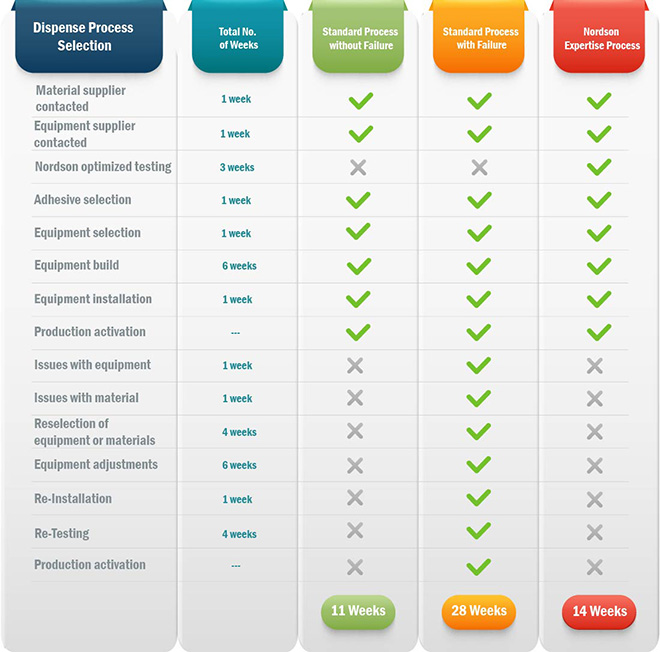
The third common mistake EV battery manufacturers make is wanting the fastest research and implementation timeline. Every organization is up against a deadline; whether they have a customer order or end of the year budgets, something important is driving their delivery time. At Nordson we have realized that not taking time at the beginning of the research phase can negatively impact a manufacturer’s production weeks later. In a traditional timeline, as depicted above, the standard process without any failure in equipment or material, can take roughly 11 weeks from the first contact to the installation and production activation. However, if the material chosen and dispense equipment counteract with one another the entire process could take up to 28 weeks, that’s seven months. Why is that? The most common reason is because they failed to test their material and equipment together before the implementation stage. This causes the manufacturer to reformulate the material or even reselect or retrofit equipment. These two factors alone could cost them 10 more weeks of downtime. Remember that customer order or year-end budget they were trying to make? Those are no longer achievable. If auto manufacturers and OEMs follow Nordson’s Expertise Process they will learn that by testing their material and equipment in advance it could add three weeks to the standard process without failure, but it could save them a minimum of 14 weeks if something fails. When manufacturers accurately plan, they can realistically deliver to their customer and organization.
Enhance your EV battery cell manufacturing
The next time automotive manufacturers, OEMs or even you look to enhance your EV battery cell manufacturing make sure you follow these three steps: 1) research your equipment and material at the same time, 2) remember to test your material options with the desired equipment to avoid challenges, and 3) realistically plan your research and implementation process to save you time and money. Nordson Sealant Equipment is always available to help enhance EV battery cell manufacturing. Contact our team today to build the best sealant application for your organization.