Sponsored by ELANTAS PDG, Inc.
Thermal conductive materials are increasingly important in electrical and electronic applications as heat management is critical to improving performance and efficiency of today’s modern equipment. ELANTAS provides an industry-leading, global portfolio of products to manage thermal dissipation in applications as diverse as motor impregnation, component encapsulation, gap fillers and thermal interface material (TIM) pads for battery and electronic devices.
Impregnating Materials
Motors have long been impregnated with coatings that improve electrical properties along with providing chemical and environmental protection. Improved motor efficiency has led to more copper being squeezed into a smaller form factor, which in turn concentrates the energy lost as heat. Getting the heat out of the windings is a major concern with new motor designs.
There are a number of different chemistries that can be used to achieve thermal dissipation of heat. A common resin utilized is Pedigree® 8183 unsaturated polyester, which has a thermal conductivity of 0.2 W/mK. Epoxy-based impregnating materials also give similar values. The use of nanomaterials and selective fillers allows us to achieve between 0.3 and 0.5 W/mK while maintaining good impregnation properties. The key design feature is thin film with low application viscosity that allows for impregnation with rheological properties that minimize air gaps.
ELANTAS is also actively developing novel thermosetting materials that achieve 0.4-0.8 W/mK thermal conductivity without significant levels of filler loading. By controlling the architecture of the cured coating, we believe we can significantly improve the thermal dissipation without compromising environmental, chemical and electrical properties.
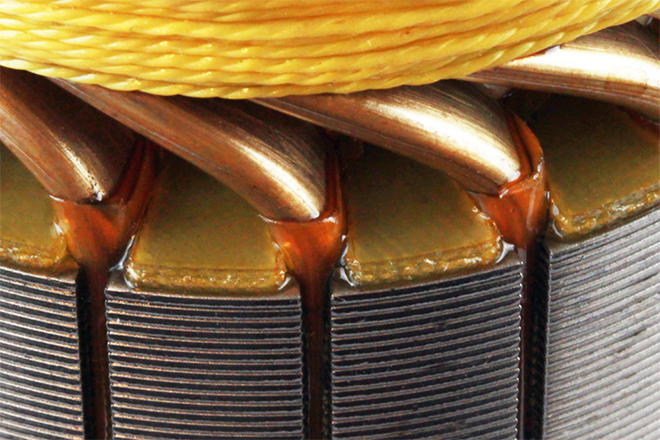
Encapsulants
Many electrical or electronic devices need more environmental or electrical protection than a thin film coating can provide. In most cases, an encapsulating material can achieve the needed properties for vibration resistance, moisture resistance or dielectrics. The drawback to thick film encapsulation is that most thermosetting materials have low thermal conductivity. Heat generation can degrade the polymer leading to premature failure of the electrical device. For example, the end windings on motors used in EV applications are particularly demanding. Heat cannot be adequately dissipated on the end turns using conventional encapsulating material. ELAN-Cast® P 300 filled unsaturated polyester is one example that provides the needed thermal conductivity (0.6 to 2.0 W/mK) while achieving excellent barrier properties to moisture and vibration stability. Application viscosity and cure time can be optimized depending on properties desired. Epoxy-based encapsulants are also available with thermal conductivity reaching 2.0 W/mK while achieving useable viscosities.
Film and Future Developments (TIM Gap Fillers/Pads)
Every component in an EV motor or battery is critical to overall thermal management. Not much thought in the past has been given to the thermal impact of components such as the slot liner in motor windings. ELANTAS has introduced the ELAN-Film® series of composite insulating film to be used in place of aramid fiber based slot liners. Aramid fiber papers contain many air pockets that lower the thermal conductivity even when fully saturated with impregnating material. Aramid papers also have poor electrical properties compared to ELAN-Film® insulation, and therefore allows one to down gauge while maintaining the same electrical properties. For example, 10 mil aramid paper has a dielectric breakdown of roughly 10,000 volts. Aramid paper also has poor thermal conductivity of only 0.18 W/mK. ELAN-Film®, on the other hand, has a thermal conductivity of 0.20 W/mK and requires only 3 mils of material to achieve 10,000 volt dielectric breakdown. This is not only a space and significant cost reduction but also a thermal management improvement compared to Aramid papers.
In development are future free-standing and composite films that achieve exceptional corona or PDIV resistance compared to conventional films. The use of semiconducting nanoparticles allows us to extend dielectric breakdown by 2-3 orders of magnitude under pulse discharge conditions. An improvement in thermal management of up to 40% was also observed for 1 mil films.
To complete the portfolio of products for thermal management, ELANTAS will soon introduce thermal interface material (TIM) gap filler and pads based on silicone and polyurethane. In development are pads with 00 hardness of 20-80 and thermal conductivity ranging from 1.0 to 4.5 W/mK as measured by Guarded Hot Plate (the Hot Wire method is expected to give 1.3 to 6 W/mK).
There are a number of silicone-based gap filler TIM materials in the marketplace. Silicone has the advantage of high thermal stability while maintaining ease of handling and thermal management properties. Our silicone gap fillers expand on the product offerings in the marketplace by focusing on low migration materials with improved ease of use.
One drawback on silicone based TIM pads is the potential for outgassing of volatile organic materials. This outgassing or migration of silicone components can be detrimental to nearby components or lead to a hardening of the silicone material. The silicone pads also are of low mechanical stability with poor tear strength. Acrylic TIM pads are also available on the marketplace at a range of thermal conductivities. However, acrylic pads have much lower thermal properties with being mostly thermoplastic materials. There is a market need for TIM pads that are higher in thermal properties than acrylics but without the migration issues and higher mechanical properties that accompany silicone materials.
One potential solution to the gap in properties between silicones and acrylics is the use of polyurethane binders. Urethanes have very low outgassing while achieving higher mechanical strength than silicones. Our recent developments have achieved significant advances in urethane thermal conductivity while maintaining good mechanical properties. Shown below on the left is our developmental polyurethane pad at 1 W/mK versus our polyurethane pad at 4 W/mK on the right. Both pads were placed on the heated surface at the same time and imaged with an infrared camera. As expected, the heat conduction was much faster for the pad on the right.
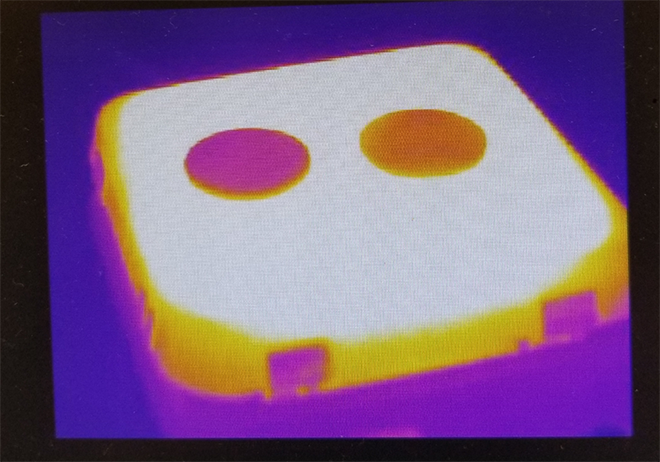
Heritage of Innovation
ELANTAS produces insulating materials for the electrical and electronics industry and a full range of thermal management materials. They are found in electric motors, household appliances, cars, generators, transformers, capacitors, digital cameras, wind mills, computers, lamps, circuit boards, and sensors, and help to ensure that product design engineers can construct ever smaller and more powerful electronic devices, thus saving materials and energy.
The ALTANA division, which is managed by a holding company headquartered in Wesel, Germany, has nine independent manufacturing companies in all major regions worldwide. In 2016, ELANTAS employed a total workforce of 976 people.
Learn more at:
www.elantas.com/PDG
Please reach out to the ELANTAS team of experts to select the right thermal interface material for your application.