Researchers at the Fraunhofer Institute have developed a new dry-coating process that’s designed to reduce the environmental impact of electrode manufacturing. The Institute says its new DRYtraec process uses machines that do not require long drying tracks, and will take up less space than conventional battery electrode manufacturing systems.
The new coating process uses similar raw materials as the slurry process, but with a binder instead of solvents. The materials form a dry mixture that is fed into a gap between two rollers rotating in opposite directions. One of the rollers turns faster than the other to induce a shear force, which ensures that the binder forms thread-like networks known as fibrils.
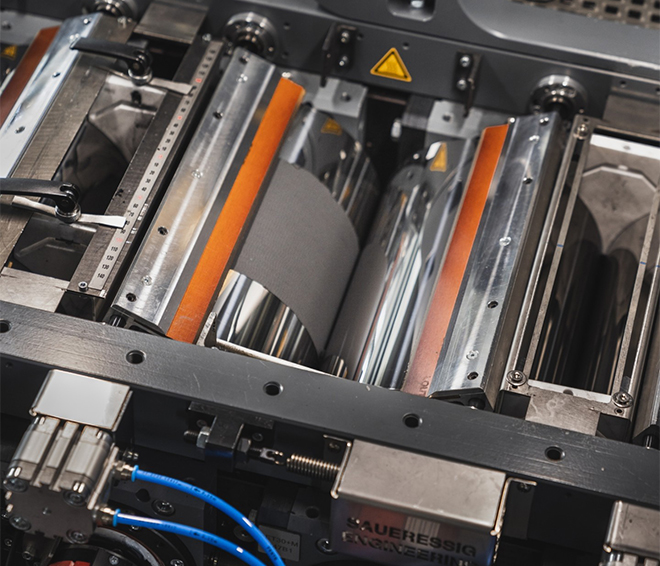
The pressure and motion form a fine film on the faster-rotating roller. This film is then transferred in a second calender gap onto a current collector foil. This allows both sides to be coated simultaneously without significant additional work. In the final step, the resulting coil is cut to the required size and the individual parts are stacked in order to produce the finished battery cell.
“The range of possible uses for the technology is not limited to a particular cell chemistry,” says Fraunhofer Group Manager Benjamin Schumm. “It could equally be used on lithium-ion cells as on lithium-sulfur or sodium-ion cells. We are even looking at solid-state batteries.”
Source: Fraunhofer Institute