Tesla has taken a major step towards implementing an innovative new chassis design—the first Model Y megacasting has come out of the enormous Idra “gigapress” at Gigafactory Texas. Front and rear megacastings will be combined with the company’s new structural battery pack to form the underbody of Model Y.
Current automobile chassis are made up of tens or hundreds of individual parts, which are made of many different materials, and must be joined together in several different ways—welds, bolts and adhesives. Tesla’s plan is to use two huge single castings for the front and rear underbody sections, and to connect them with a battery pack that serves as part of the body structure. This innovation reduces weight and greatly simplifies vehicle assembly.
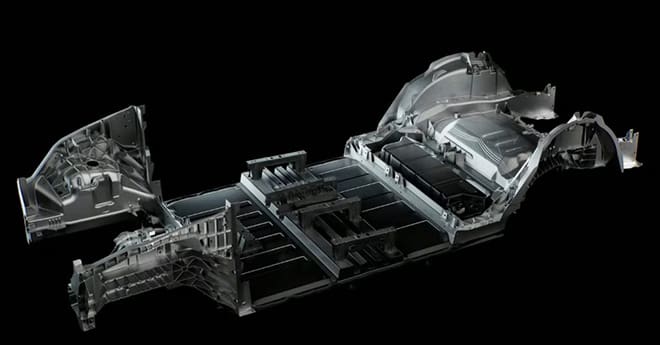
Cast components are a staple of auto manufacturing, but the norm is to cast smaller parts, which are then assembled into larger structural elements. As Elon Musk tells the story, one day he was considering a die-cast toy car on his desk, and wondered what the practical size limit for a casting would be. After some research, he learned that there really is no size limit, and decided to fabricate the front and rear underbodies of a vehicle as two castings with huge machines made by IDRA GROUP.
Now casting expert Axel Turck has released an image of the first front-end megacast underbody produced by Tesla. The part, which weighs 286 pounds, will be used in the production of Model Y at Gigafactory Texas, which is expected to start by the end of this year.
Source: Electrek