The Demak Group is a global leader in the resin dispensing field. Since 1984, Demak has been innovating and manufacturing state-of-the-art machines for the meter and mixing of epoxy, polyurethane, polybutadiene and silicon resins, designed specifically for encapsulation, gluing, insulation, and industrial components sealing. Additionally, Demak can supply customers with the most suitable resins for their production processes, thanks to Demak’s sister company S.E. Special Engines Srl, a chemical formulation and production company founded in 1976.
The Demak Group therefore proposes itself to the EV / HEV automotive market as a supplier of equipment and resins for the encapsulation of traction electric motors and other electrical-electronic components. The electric motors encapsulation is becoming more and more commonplace in the automotive world due to the rapid ongoing development of EV and HEV technologies. The Demak Group in recent years has acquired tremendous successes in the encapsulation of traction motors for fully electric and hybrid cars.
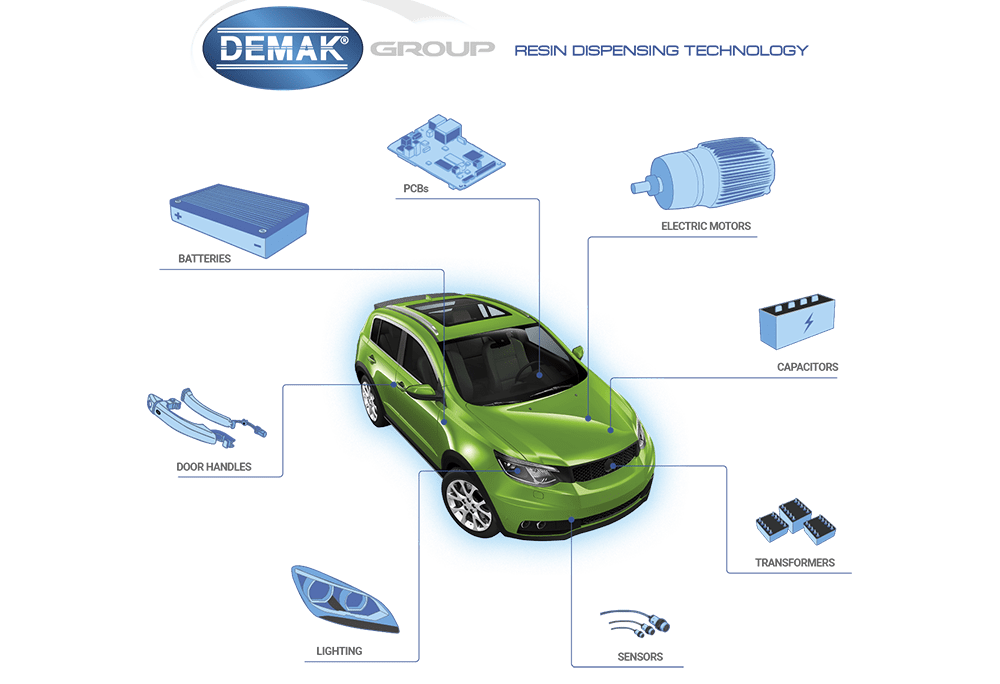
The use of vacuum encapsulation technology is becoming increasingly essential to provide the best protection and increased performances of the electric motor. With the formulation and application of a suitable resin, it is possible to guarantee thermal dissipation of the motor and a greater resistance to shocks, vibrations, chemical agents, water, dust and other external agents.
In addition to specific equipment systems, The Demak Group has developed resins specially formulated to guarantee thermal dissipation, an increased thermal resistance during continuous operation and during thermal shock cycles. This is critical because the resin has to resist the heat developed by the motor in action and potentially to extreme temperatures conditions. Encapsulation, compared to other resin methods, guarantees better protection of the windings and to the motor as a whole, as well as greater resistance to shocks, vibrations, chemical agents, water, dust and much more. Moreover, encapsulation guarantees much greater thermal dissipation compared to other methods of resin coating, such as impregnation and trickling.
Many applications and components, such as electric motors, require resin potting or vacuum casting in its production process.
The insulation of motors and other components is absolutely necessary to guarantee the highest levels of durability and performance. These final products require the absolute absence of moisture and avoidance to any contact with external agents that can damage the components internally.
The vacuum casting application, which incorporates the use of a vacuum chamber, contributes another great advantage to the e-motor by preventing the following:
Air bubbles or gaps in the resin can reduce the insulation of the motor and compromise its performance and durability. Furthermore, a bubble or void can create a partial discharge between the ground and the primary insulation.
Bubbles also decrease heat dissipation provided by the resin.
To obtain an electrical component without bubbles and humidity, the resin must be “forced” in all the internal spaces of the stator (in particular in the undercuts and in the windings), and the only way to do this is by dispensing under vacuum.
Demak can guarantee, credited to 40 years of experience in the field of insulation of electrical components, a total absence of air in the resin (through industry-leading degassing systems) and also in the final products (by incorporating its vacuum casting systems). Therefore, all the dispensing systems used in these types of processes are equipped with vacuum chambers. This is the last major step in the complete process of encapsulation, as Demak’s technology for vacuum degassing starts from the loading of the resin in the machine until the last moment of dosing.
Another fundamental component of the process are the resin and hardener tanks. These tanks are equipped with a thin-film degassing system for continuous dehumidification of materials, which facilitates the resin’s final results.
An efficient vacuum dispensing process, together with a high thermal resistance epoxy resin, allows the e-motor to be qualified for all the durability tests required by the OEM.
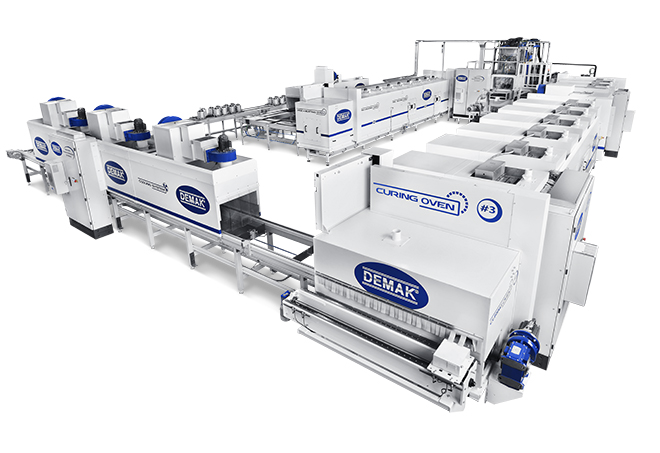
It is safe to assume that electrification, which has already been underway for some years, will become a vital step for all OEMs and their supply chain. But above all else, companies will have to integrate technologies that have zero or minimal environmental impact in their production cycle. Besides investing in R&D for the development of electric traction with greater autonomy, companies will also have to plan to invest in “Eco-Friendly” technologies that can guarantee top-level performance of the electric motor and other components. In this case, the Demak Group can be a reliable partner in all resin dispensing processes, providing tremendous value with its 360° knowledge, expertise, and first-class customer service.
For further information don’t hesitate to contact the Demak Team: