Sponsored by Nordson SEALANT EQUIPMENT
As businesses and consumers evolve in 2020, the world is left wondering how their footprint impacts the Earth as a whole. Every day businesses are implementing eco-friendly habits. Whether it’s recycling paper waste, encouraging the use of a water fountain or even purchasing energy efficient lighting, the way businesses operate can affect the generations yet to come. What does that mean for electric vehicles? They are already perceived as environmentally friendly. How could they be engineered greener?
Process improvement
When you think about the process to build an electric vehicle, there are a thousand steps and parts. Over time new models, versions and technology will be released. But have you ever wondered why engineering constantly evolves? There are the traditional answers like being the first to market with a new feature or design, a better experience for the end consumer, or maybe even to make the world a cleaner and safer place.
Nordson’s team of engineers actively seeks to build a better tomorrow but places the EV manufacturer’s goals first. When it comes to manufacturing an EV battery, Nordson strives to be innovative with attention to detail at every step. We focus on leading the automation of sealant dispensing for 1-part and 2-part materials used in EV battery cell manufacturing. That’s why we are exploring how foam dispensing can improve the process of EV battery pack manufacturing.
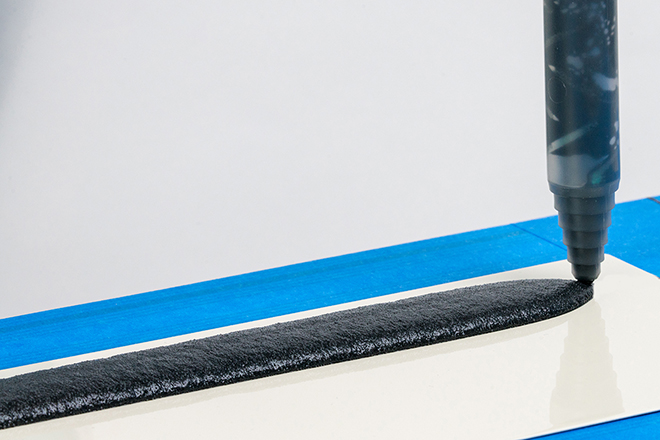
Lightweight sealing alternative: foam
Why foam? Every element within an electric vehicle affects the overall weight and efficiency of the car. Automotive manufacturers are challenged with the balance between designing a new feature, which adds weight, and increasing the maximum miles per a single charge. Foam is a lightweight alternative when compared to conventional gasket materials, because of its cellular structure. A homogeneous mixture allows the 2-component foam to expand when sealing a battery pack, ultimately covering more space with less product. The foam is also durable enough to detour environmental factors, like dust and water, from entering the battery pack. These factors can improve the longevity of an EV battery.
Enhanced technology provides greener solutions
Foam gasketing could also provide the ability to open and close a battery pack multiple times. With a traditional sealing gasket, once the battery pack is sealed it cannot be reopened. If one or two battery cells fail over time, then the maintenance repair operator (MRO) is unable to reopen that battery pack to replace the bad cells. Instead the driver will never be able to fully charge their battery until the entire lithium battery pack is replaced, which can hinder the driver’s experience with electric vehicles. This small factor, the charge life of a battery, could affect a customer’s repeat purchase with the same automotive brand in the future. It is important to automotive manufacturers to create a loyalty with their drivers and retain a customer for life.
Now foam gasketing is being tested to allow EV battery packs to be reopened and dissected to only replace the cells that have failed over time. This provides a better end-of-life process for each battery pack. It ensures all reusable components are salvaged and non-reusable parts are economically disposed. When the MRO replaces each battery cell individually it drastically helps eliminate the amount of waste in our landfills and saves money for the car owner and manufacturer.
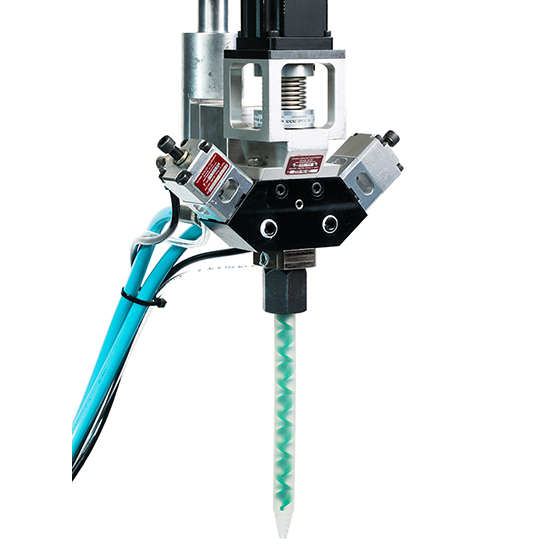
Precise application is key
Since foam expands, manufacturers often realize how difficult it is to dispense accurately. At Nordson, we have a variety of meters and valves to dispense foam precisely. We leverage Positive Rod Technology to displace the foam at a perfect volumetric ratio every time. This minimizes the wear and tear on the meter itself, helping automotive manufactures reduce their maintenance costs. Whether its little shots, big dispenses, Micro-Meters or Pro-Meters we have the technology that can meet your demands. We have even analyzed how the smallest of dispensing errors are magnified with foam. It is important that we produce clean starts, stops, corners and knit line ending. Our Dynamic Power Mixing Value produces quality dispensing, helping to maintain an evenly consistent gasket. Regardless of your application our engineers can design and test foam’s greatest challenges.
Partner with us
Today we engineer for a better tomorrow. We’ll put your customer first and help build a cleaner life for the generations yet to come. If you need help precisely dispensing foam, then let us partner with you. Right now for a limited time only, we’re offering complimentary CPK tests for qualified projects*. Our material testing labs based in Wixom, MI, United States can help provide a thorough analysis of your dispensing material. See if you qualify, contact us today!