The focus of LORD Corporation’s study is to investigate how the superior thermal transfer provided by gap fillers versus gap pads affects cooling of actual battery modules. Battery modules were assembled using LORD gap fillers with thermal conductivity of 2 and 4 W/m·K, and also with commercially available gap pads of the same nominal thermal conductivity. The degree of cooling for each assembled module was then measured during a fast charging cycle.
The work confirms that the LORD gap fillers provide superior battery cooling compared to the gap pads. Liquid-dispense gap fillers allow for infinite patterns and volumes to fill all of the gaps, whereas thermal pads are limited by their thickness and mechanical hardness. The following figure illustrates this effect.
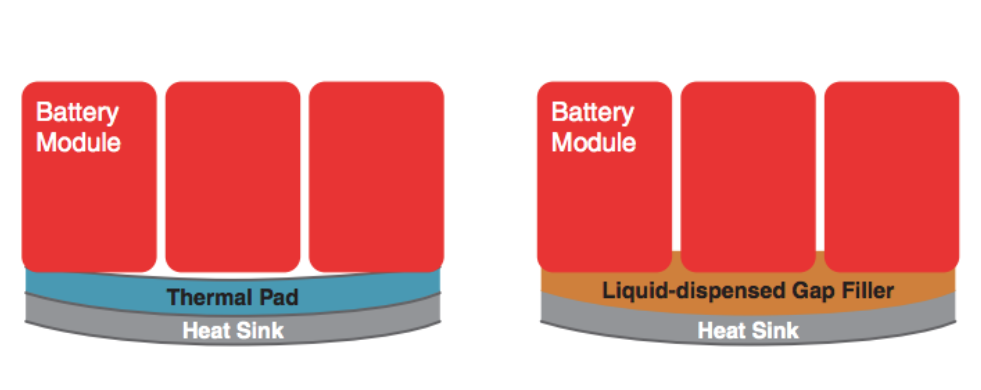
Experiment:
Table 1 lists the gap filler and thermal pad TIMs used in this study along with key properties. The thermal gap pads were selected to have comparable thermal conductivity and hardness values to that of LORD CoolTherm SC-1200 and SC-1500 cure-in-place liquid gap fillers. Gap pads with a thickness of 1 mm were used. LORD partnered with the National Renewable Energy Lab (NREL) in Denver, Colorado (USA), for assistance in test design and for manufacture and testing of cell modules. NREL recommended a five-cell module using Samsung SDI prismatic cells (94 A·hr, 4.1 V), the same cells as used in the BMW i3 electric vehicle. All cells were outfitted with thermocouples at the top left, middle, and bottom right of one face. The central cell in the module had an additional two thermocouples at the top middle and bottom middle of the same face.Reported by supplier on product technical data sheet
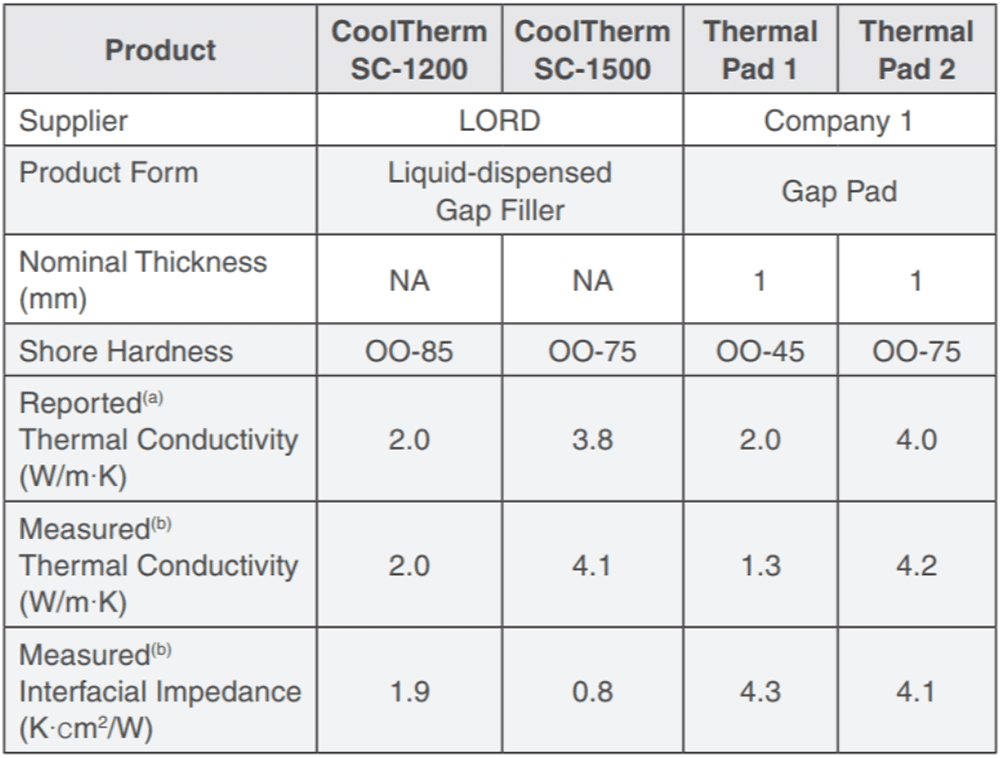
(b) Measured via ASTM D5470 as reported in previous white paper
Thermal performance for the different modules was tested under fast-charging conditions. In this test, a constant current of 150A was applied until the voltage limit was reached, corresponding to 1.5C charge rate for our modules. Because the five cells were not completely electrically balanced during the charge event, it was necessary to apply lower levels of current for short time increments after the initial charge to reach 100% state-of-charge for the module. A typical charge cycle and the resulting voltage response are shown here:
The total amount of heat removed from each module during the charging cycle was determined by measuring the increase in temperature of the cooling liquid at the outlet of the cooling plate and using this value, combined with the known coolant flow rate and heat capacity of the coolant, to calculate the power transferred to the coolant. These values are plotted versus time in the following figures. A higher value of heat removed indicates a more efficient TIM and more cooling of the battery module.
This graph compares CoolTherm SC-1200 gap filler (2 W/m·K) with the 2 W/m·K gap pad and with the baseline modules containing no TIM. Without simulating tolerance, the gap filler removes about 62% more heat than the baseline and about 24% more heat than the gap pad at the peak. With additional 1-mm shims at cells #2 and #4, the gap filler performance was barely affected, whereas the gap pad and baseline both decrease significantly. In this configuration, the gap filler removed twice as much heat as the baseline and about 47% more heat than the gap pad. This is likely due to the ability of the liquid-dispensed gap filler to conform to the irregularities in the cell-to-cooling plate distance, as predicted in our prior white paper.
This next graph shows a similar comparison between CoolTherm SC-1500 gap filler (4 W/m·K) and the 4 W/m·K gap pad. Without additional shims, the gap filler removed nearly 70% more heat than the baseline and about 27% more heat than the gap pad at the peak. With additional shims the CoolTherm SC-1500 gap filler performed about the same as the 2 W/m·K gap filler, but the 4 W/m·K gap pad performed worse than both the 2 W/m·K gap pad with shims and the baseline without shims. We attribute this worse performance to the increased hardness of the 4 W/m·K gap pad, which prevents it from conforming to the uneven gaps between the individual battery cells and the cooling plate as well as the 2 W/m·K gap pad does. A similar effect was observed in our previous work, which showed that the thermal impedance of the 4 W/m·K gap pad was nearly the same as that of the 2 W/m·K gap pad (see Table 1) and was not improved as much by application of pressure due to its higher hardness.
Conclusions
Our results show a clear advantage for liquid-dispensed gap fillers versus thermal gap pads for removing heat from and reducing temperatures in battery modules. Liquid-dispensed materials are able to fill irregular gaps due to surface roughness and also due to manufacturing irregularities to give uniform and repeatable performance in a full battery module. This is a practical demonstration of the fundamental findings in our previous white paper, which showed that the thermal impedance of gap fillers was much lower than gap pads due to a lower interfacial thermal resistance. With proper application, even a lower-conductivity gap filler can out-perform a higher conductivity gap pad.
Our results also show that you can gain excellent thermal performance even using a relatively low thermal conductivity gap filler. Higher conductivity gap fillers will become more valuable and more differentiated as the thermal load increases. In addition to the improved thermal performance, the ease and speed of application of CoolTherm liquid-dispense gap fillers makes them ideal for high-volume automotive manufacturing processes.
Acknowledgements
We sincerely thank Matthew Keyser and Thomas Bethel at the National Renewable Energy Laboratory (NREL) in Denver, CO, for their invaluable assistance in planning, conducting, and analyzing the data for this study.
To read the full white paper and view additional data points, please click here. If you have any questions for our technical service team, please reach out to us.