Lithium Australia subsidiary VSPC has figured out how to make Li-ion battery cathode material, and Li-ion batteries, from tri-lithium phosphate produced directly from mining waste. The proprietary SiLeach process eliminates the need to generate high-purity lithium hydroxide or carbonate, which is one of the most cost-intensive and challenging steps in the manufacture of Li-ion batteries.
VSPC converted the tri-lithium phosphate to lithium iron phosphate cathode material at its electrochemical laboratory in Brisbane, Queensland.
VSPC found the cathode material to be of similar quality to its standard lithium iron phosphate material. Lab workers subsequently produced coin cells that were tested under a range of charge and discharge conditions, and the cells achieved equivalent performance to VSPC’s current cathode powders, which use lithium carbonate as the manufacturing feed.
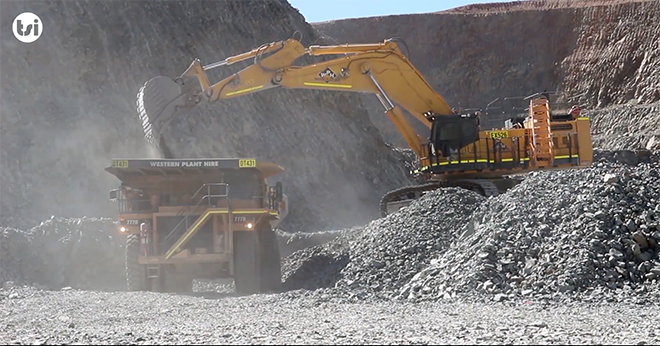
Lithium Australia’s Managing Director Adrian Griffin said the development has a lot of potential. “The most notable aspect of this achievement is its simplicity, and the ability to streamline the processes and cost required to produce LIB cathode materials. The broader application to lithium brine exploitation provides enormous potential for that part of the lithium industry, by removing the cost-intensive route to lithium hydroxide.”
Source: Lithium Australia