There seems to be an endless array of electric motor topologies, architectures, and configurations. Among the many design choices that engineers face is the shape of copper wire that is wound in the stator.
In a new paper published in the IEEE Transactions on Industry Applications, researchers compared using flat wire hairpin winding and stranded round wire in some of the most common motor technologies found in EVs: induction, synchronous permanent magnet and wound field machine topologies.
The research showed what many in the motor industry have been claiming for decades: there are significant advantages to using flat wire hairpin windings in some types of motors. “The advantage of flat wire winding associated with a parallel slot configuration is a much higher copper slot fill factor,” write the authors.
Cramming more copper into the available area has been shown to create a shorter end-turn space, reducing heat and improving torque and power density – which ultimately can reduce the motor size for a given application. Hairpin winding schemes can make it easier to strengthen the construction of critical connections between conductors. The windings are also well-suited to liquid cooling, which further enhances performance and reliability.
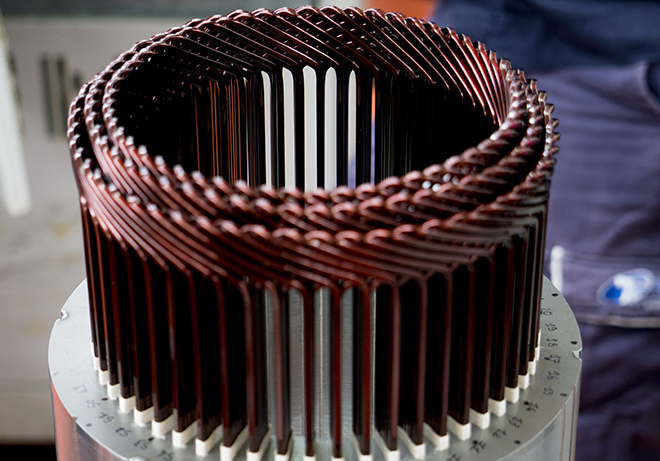
One example given in the paper showed that, when one particular induction motor design used a hairpin winding configuration, maintaining the same slot area, “the maximum starting continuous torque increases by 44% from 180 Nm to 260 Nm, while the maximum continuous power sees an increase of 17% from 135 kW to 158 kW.”
It’s no wonder that many automakers design motors that implement hairpin stator winding for EV traction applications. One Italian company, Tecnomatic, has built its entire business around helping automakers with design manufacturing processes for hairpin stator systems. Charged recently chatted with Maurilio Micucci, Project Manager at Tecnomatic, to learn more about the company and its technology.
Charged: How long has Tecnomatic been developing specialized hairpin stator assembly systems?
Maurilio Micucci: Tecnomatic was founded in 1973, so we have more than 40 years of experience. The company was founded for the design and development of special machines for stator winding and motor assembly. And then in the last 20 years, we focused on hairpin technology, beginning with things like automotive starters and alternators in 1999.
Since then we have developed a very long history with hairpin stator technology, and today we develop a fully-automatic system for manufacturing hairpin stator systems. The first project we worked on related to traction motor applications began over 10 years ago with Delco Remy. We started to develop that process around 2003, then we finalized the design, and those motors were used in GM hybrid vehicles like the Yukon and Tahoe.
Today we design special hairpin machines for lots of different stators – they range from lower-voltage applications like starters and alternators to bigger applications like traction motors – so from 14 V to 600-700 V or more. In the end, the process to manufacture them is similar, no matter the size or voltage. What changes sometimes is the specific materials like lamination steels, copper and insulation.
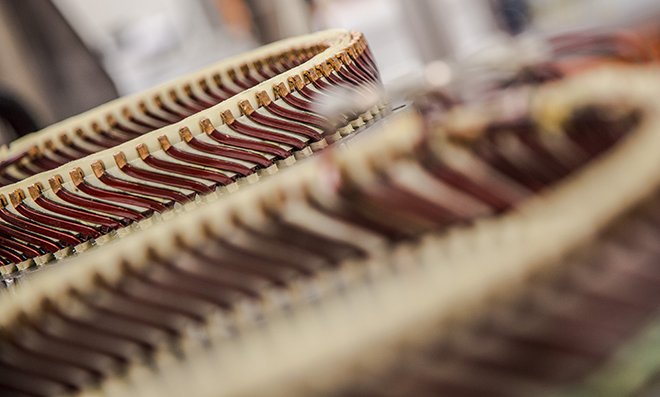
Charged: Do you help automakers with the stator design, or just the manufacturing process?
Maurilio Micucci: Both. Typically, a customer comes to us with an initial design, and we will help them with the process and then sell them the manufacturing equipment that we specially design for them. At the same time, we will provide recommendations for the stator design based on our experience and knowledge base. So feedback may include things like a method to modify something to achieve better manufacturing results, because we are very familiar with what’s possible on the machines. We’ll recommend things like the winding pattern, winding connections or overall dimensions of the stator.
In any case, we’ll take our customer’s design – maybe it will change somewhat, maybe not – then we will develop a prototype, and finally a fully automatic production system.
For the prototyping stage, we think it’s very important to make prototypes that are ready for the process, and not to make prototypes by hand. So we’ve developed a specific department at Tecnomatic with a dedicated team for prototyping according to the product design of our customers. The focus is to link the prototype of the design to the actual manufacturing process. The tooling that we will be using for the prototype is 99% similar, if not identical, to the tooling that is necessary for manufacturing. The target is to provide a sample assembled part to the customer as a prototype that is more or less industrialized. Of course, at that stage, there can also be some additional optimization of the stator.
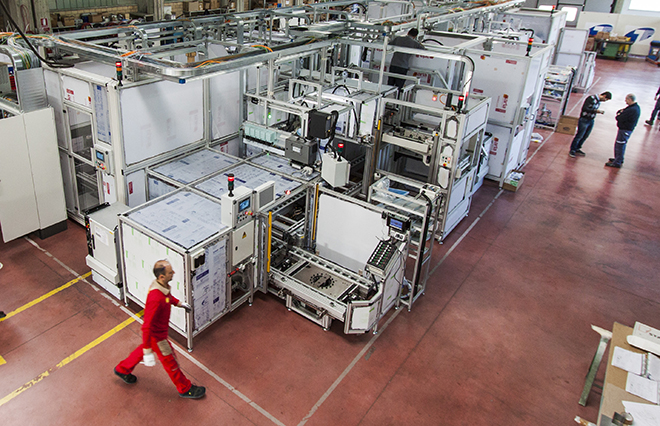
Charged: Are the manufacturing systems and processes you design for hairpin stators changing a lot as EV development projects are taking off?
Maurilio Micucci: Yes – nearly all of our customers are in the automotive industry. When I began at the company over 20 years ago, we also made systems and process for round wire, but decided to work with flat hairpin conductor applications specifically because of the advantages it offers for automotive, because we really believed that it is the future for these specific high-volume applications.
There are several reasons why engineers are choosing hairpin stators. Of course, to be very clear, they are best suited for some specific motor applications like automotive traction motors. Not everything can be made with hairpin technology.
We continuously conduct a tremendous amount of R&D. Our current portfolio is about 200 patents related to products and process for hairpin flat conductor applications. In the last year alone, we’ve had many more patent applications. The ultimate goal is to protect our customers’ investments.
So we’re researching things like connection technologies, advanced materials, winding schemes, etc. We are moving very fast to increase the number of conductors per slot, which increases the possible applications of stators with hairpin technology. This is because it offers more design options for the number of conductors, size of connectors, number of turns, etc. In the last two years, we’ve developed processes to go from using two conductors per slot to four, six and eight conductors per slot.
Also, we are involved in a lot of regional, national, and European research projects that are dedicated to new innovation in e-mobility, and one project in particular that is in agriculture applications for electric motors.
Also, we have a great partnership with the Department of Industrial and Information Engineering and Economics (DIIIE) at the University of L’Aquila – which is very close to Corropoli, where we’re based. They have a very important research department for electric motors, and we work with them when we need some specific research into motor winding theory.
This article originally appeared in Charged Issue 37 – May/June 2018 – Subscribe now.