Comparing the spec sheets from different parts manufacturers is tricky business for engineers in any industry. However, the advanced battery market seems to be uniquely challenged in this regard. As Tesla CEO Elon Musk often points out, when it comes to batteries, the BS factor is outrageous.
Even if you assume that every vendor provides product specs that are based on real data and not wishful thinking, there are so many important parameters in battery benchmarking that it’s very hard to compare apples to apples without testing different samples yourself.
In an effort to help the EV industry cope with this challenge, the Southwest Research Institute (SwRI) created the Energy Storage System Evaluation & Safety Consortium (EssEs) in 2011. Now in its second phase, the goal of EssEs is to provide transparency in the automotive, utility and battery markets. Members include automotive manufacturers, electric utilities, OEMs, battery pack integrators and others across the lithium-ion supply chain.
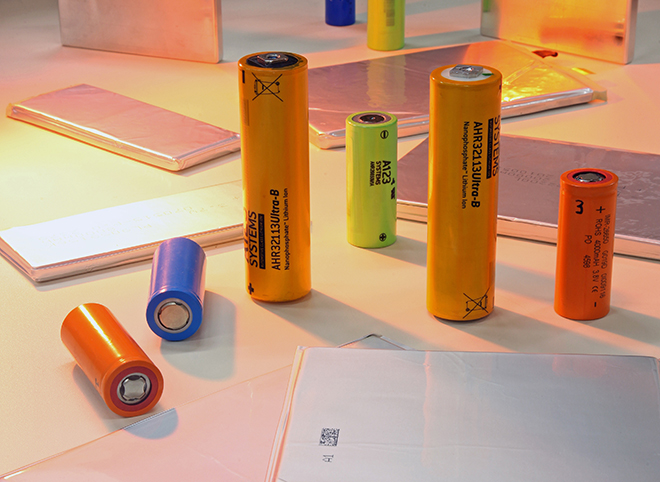
SwRI has a long history of putting consortiums together in different technical areas such as diesel engines, spark-ignited engines, robotics, etc. “We decided to look for interest in pre-competitive benchmarking and research in the battery area,” Bapi Surampudi, Staff Engineer at SwRI, told Charged. “And we certainly gathered enough interest to decide to start a consortium in the area.”
Willingness to share
When designing battery packs, companies will develop a lot of proprietary information regarding the packaging, cooling, insulation, heat spreading, management electronics, etc. Most of that is considered competitive product information, and is not something they are willing to share within a consortium.
However, the “pre-competitive” data refers to a better understanding of the strengths and weaknesses of different commercially available cells. These things are partially satisfied by the battery manufacturer, but there is no standard as to how a battery should be completely specified and what type of information has to be provided. So companies are very willing to work together on basic research and benchmarking to share the costs and avoid the need to do testing in-house.
“It’s best to reserve as much of the budget as possible for customized product development,” said Surampudi. “Everyone recognizes the tendency for cell manufacturers to highlight the strengths of their batteries. So one of the benefits of the consortium is that it provides a common benchmark by using the same test procedures to conduct a 360-degree view of the cell data. Then members can compare different chemistries and see what will be the best fit for their application.”
SwRI says that the majority of members in Phases 1 and 2 have been vehicle OEMs and battery pack integrators. While one battery manufacturer did join in Phase 1, Surampudi describes the industry’s attitude as similar to that of the combustion engine industry in the early stages. “Many years ago, engine manufacturers who were competitors would never come to the same table to look at what is the state of the art in the industry. That has changed over time because they’ve realized there is no sense in not sharing that type of information. It’s just the nature of this early stage of the battery market – it forces manufacturers to focus on their products rather than working together wherever possible. But that will change over time.”
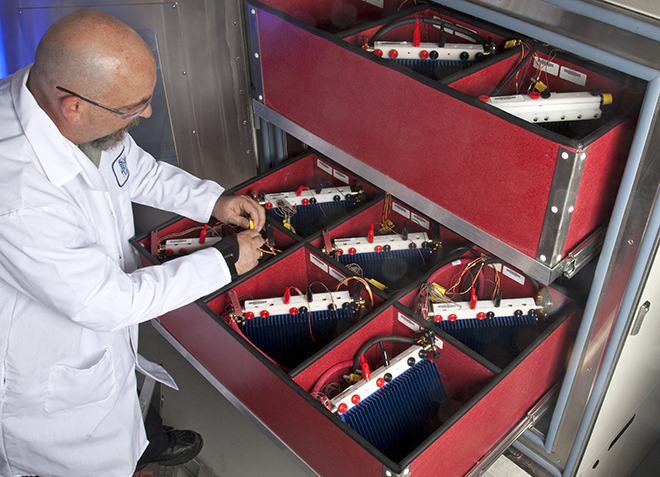
The tests
SwRI consortiums go through a gradual adoption of the scope of work – Phase 1, 2, 3, 4, etc. – in an attempt to match the requirements at different times. Its diesel engine consortium, for example, is now in Phase 7.
In EssEs, each phase of the consortium typically contains both benchmarking and research projects, and members vote on which specific cells to benchmark and what research projects to perform. In some cases, cells are not readily available on the open market, so EssEs will buy a vehicle, drop out the battery pack and remove the cells for testing.
The cell-level tests are broadly classified into four categories: manufacturing, performance and characterization, calendar/cycle life, and safety/abuse.
Manufacturing
In the area of manufacturing, the researchers analyze the cells to see how consistent they are at the beginning of their life. Tests include mass variance, initial internal resistance, open circuit voltage and Electrochemical Impedance Spectroscopy. Statistical analysis then provides insights into consistency of samples and extrapolations to larger populations. Cell samples are binned for different test categories based on sigma levels.
“Results from the manufacturing tests give members the insight to know that the amount of imbalance between the cells will be as small as possible,” said Surampudi. “They know exactly what to expect when they acquire batteries within a certain sigma level.”
Performance and characterization
To test data sheets and marketing specs against comprehensive and objective benchmarking, the consortium will map batteries – just like an engine – across many temperatures and many charge or discharge curves. Tests include static capacity, energy efficiency, hybrid pulse power and cold cranking. Analysis delivers mapping of beginning-of-life data for pack sizing and initial calibration of battery management systems. Data includes comprehensive maps of capacity variations with current and temperature along with pulse power data sets as a function of depth of discharge (DOD) and temperature. Cold cranking data allows members to select appropriate cell chemistry for their plug-in hybrid applications in cold climates.
“We can actually measure the thumbprint electrochemical behavior of the battery and mark the signature of the chemistry inside the battery,” said Surampudi. “We measure how the capacity, power, and energy change across different conditions.”
Calendar and cycle life
Life testing helps members determine the true cycle life of cells and packs under normal and extreme conditions. Li-ion cells also age while in storage, so EssEs will also develop guidelines for the best temperature and state of charge (SOC) for long-term storage. Both factors have been shown to influence aging while sitting on the shelf.
Tests include Taguchi DOE map-based cycle life and calendar life at various DOD, current, power and temperature test conditions, and reference performance testing. The cycle life analysis delivers a model as a function of change in SOC, charge power, discharge power and temperature. Tests also measure temperature variations in cells at different duty cycle stress levels.
“Our cycle life data helps to determine how long a manufacturer will warranty the powertrain and pack itself,” said Surampudi. “We’ve also patented a special method for life testing in Phase 1, and all the members get access, royalty-free, to any patent that is generated in the consortium.”
Abuse
The last category of cell-level testing is abuse or safety. Abuse testing pushes batteries to the limits to evaluate thermal stability, overcharge and penetration risks. One overcharge test is conducted on a production module to study fire propagation. Analysis of test data provides ambient temperature thresholds of venting and fire for each cell type; threshold of overcharge failure and impact; impact of heat spreaders, insulators and battery chemistry towards fire propagation inside a production module; and internal short circuit simulated by nail penetration.
Road tests and pack architectures
EssEs will also conduct simulated driving tests of the vehicles they acquire before disassembling them to access the cells. “For example, we wanted to test the Panasonic 25 Ah cell that was used in the VW e-Golf,” explained Surampudi. “We weren’t able to get the cell directly from the manufacturer, so we bought an e-Golf. It made no sense to simply disassemble the vehicle immediately without any testing, so we put the vehicle on a chassis dynamometer and simulated high-stress conditions like grades and high speeds.”
“When we test a cell acquired from a vehicle, we don’t have a spec sheet from the cell manufacturer, so we have to generate our own. We can do this by monitoring the vehicle voltage, power and charge management to determine the operating boundaries that the manufacturer designed the system within. That is very important to generate our own specifications for our tests so that when we disassemble a battery pack, we can still honor the manufacturer’s specifications.”
Also, EssEs provides members a detailed look at the pack design for the vehicles they disassemble. Benchmarking on commercial EVs delivers insights into various active and passive thermal management systems, and members can learn about the delicate trade-off between performance and safety that becomes a major design factor in these systems.
Future work
Phase 1 of EssEs was conducted from 2011 to early 2015, and Phase 2 began in late 2015. The consortium is always soliciting new members, and interested parties can join at any time and gain access to all the data, including that generated during Phase 1.
Surampudi explained that about 70% of the consortium’s budget is spent on benchmarking, and 30% on research. Currently, one research topic is picked every year. Examples include overcharge tolerance of aged batteries and diagnostics of lithium plating (a Li-ion failure mechanism in cold temperatures).
“Moving forward, as membership increases, we expect to benchmark more and more batteries per year and also grow the research content at the same time,” said Surampudi. “For example, our diesel engine consortium does 100% research and development projects. So, as members drive the direction, we expect to generate a lot of useful algorithms for batteries – diagnostics and prognostic data, threshold thermal management strategies, insight into fire propagation, effectiveness of heat spreaders and insulation materials between cells, etc.”
Membership has its benefits
EssEs offers four main benefits to members. The first is cost. Members can leverage benchmarking cost-sharing, freeing up in-house resources for product and application development. “If you were to attempt the same testing in-house, you would spend roughly 10 times the cost of the membership,” said Surampudi.
Second, from an R&D standpoint, members get exclusive comparative intelligence and detailed performance data to help them select the best matching cells for a specific application. The generated proprietary data is shared only among consortium participants. “It’s completely unbiased data, because we’re not partial towards any particular manufacturer,” said Surampudi. “Everything is tested at exactly the same conditions, so they can compare and shortlist battery types that have a natural match for their application – either power-centric or energy-centric.”
The third benefit is access to data that members can use for pack system design. The data gathered and its analysis assists in the design of pack architecture, thermal management systems, battery management systems and algorithms.
“And finally, our team actually attends all the major conferences,” said Surampudi. “We capture a summary of the state of the art of the battery industry and the various applications. We present that to the members during our meetings in San Antonio.”
Because consortium testing goes above and beyond industry standards, EssEs says it aims to contribute to standards-making bodies. Members have also conducted many of the international regulatory battery pack safety standard testing at SwRI’s facility.
“Ultimately we want to help the industry by providing transparent information, with a focus on safety, performance, warranty and quality,” Surampudi said. “This is what drivers and passengers expect of electric vehicles.”
This article originally appeared in Charged Issue 29 – January/February 2017 – Subscribe now.