Alta Motors claims that its dirt bikes have a battery pack with energy density that’s among the highest of any production vehicle. With help from Scheugenpflug’s custom production equipment and Wevo-Chemie materials, the motorcycle builder says its thermal design was the key to achieving that.
Seven years ago, a group of motorcycle and off-road dirt bike enthusiasts starting thinking about the advantages of an electric off-road two-wheeler: constant power output, tunability, great control and responsiveness. Fast-forward a couple of years, and Alta Motors is manufacturing electric motorcycles at its California facility at a rate of up to 10 bikes per day.
Alta calls its first production model the Redshift MX. With a water-cooled 14,000 RPM motor and a 5.8 kWh battery pack, the company describes it as the electric equivalent of a modern 250 that’s as capable on trails as any MX2/Lites class motocrosser.

What really caught our eye at Charged was the company’s claim that its battery design had one of the highest energy densities at the pack level of any production vehicle.
One of Alta’s production equipment suppliers, a company called Scheugenpflug, introduced Charged to the motorcycle builder’s innovative designs. Scheugenpflug helps many companies around the world set up adhesive bonding dispensing equipment in production lines for battery systems (and many other applications), so they know innovation when they see it.
To learn more, we chatted with the engineering teams at Alta Motors and Scheugenpflug.
Charged: Does Alta Motors design its drivetrains in-house?
Rob Sweney, Alta Motors’ Director of Advanced Powertrain: Yes, early on we took a strategy of doing as much in-house as we could. I joined Alta to lead the battery design, but also had a hand in the powertrain and chassis design. We really wanted to respect the traditions of motorcycling and not change things like chassis geometry and suspension, so in those areas our designs are intended to match the performance of any other gas-powered products. We make careful efforts not to reinvent the 70 years of motorcycle chassis and suspension evolution. We focus on all of the new EV-specific aspects of the vehicle in order to have control over their integration and optimization.
My personal focus when I joined was to lead the battery pack design and build it up from scratch. The main driver was to really optimize for this application. That included the robustness requirements of an off-road motorcycle. The energy density is important not only for getting to a competitive weight in a race vehicle, but also to get the center of mass where we wanted it to meet packaging design and handling goals, making it a very nice motorcycle overall.
The cells we use are an 18650 form factor from a top supplier. Similar to Tesla, we started with the small form factor cells that grew out of the consumer electronics industry, and then did everything ourselves to integrate them into a larger pack. We designed all the BMS, safety and packaging.
The result is what we believe to be the highest energy-density pack that’s currently in production in a vehicle. We’re right around 180 Wh/kg, which is about 20-30% higher than the current Tesla Model S. We believe the Model 3 will probably be on par with where we are today, although they haven’t announced numbers yet, so we can’t calculate it.
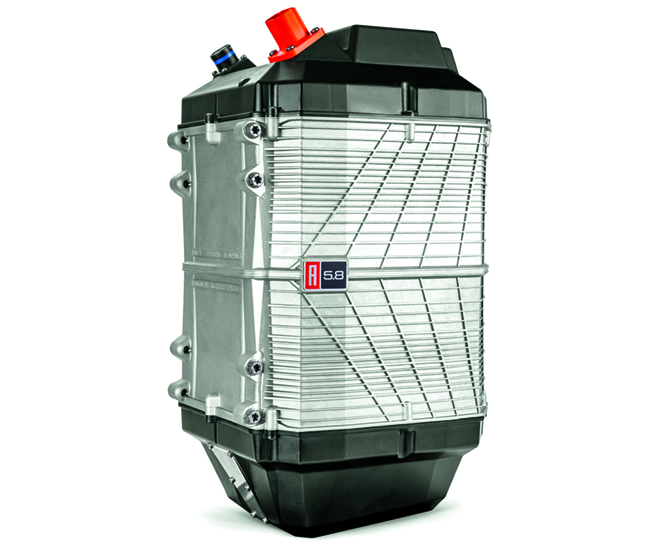
Charged: What were some of the design features that allowed you to achieve that?
Rob Sweney: As a battery designer, I tend to think of everything as overhead. You have a cell with a certain weight, cost, output and volume associated with it. Then it’s really trying to whittle away at everything around the cell to reduce that to the minimum necessary set of things in order to meet all of your system-level requirements. Doing more with less, or using the least amount of stuff possible.
Overall, there are 3 or 4 key aspects that we improved above the state of the art. It’s packaged well. I would say that interconnect technology – how you connect cells to each other – is a major challenge of battery design, and we have some innovation there. Then there’s our thermal system – how we cool and manage heat between cells. And also how we absorb or disperse heat from the cell in a safety-critical thermal runaway.
So, we have a few key designs for thermal management and interconnect that allow us to package cells as tightly as possible and really come up with a dense highly-curated design that reduces the amount of overhead.
Charged: Could you tell us how your interconnect technology works?
Kevin Kim, Alta Motors’ Mechanical Engineer: Unfortunately we can’t disclose too many details about the interconnect system because it’s proprietary. I will say that the system allows us to very effectively cool the battery using passive (air-cooled) methods, with no need for liquid cooling. We describe it as being passively air-cooled, and it helps keep the weight down significantly.
Passive cooling means that the thermal conductivity of the materials that surround the cells is very important. After some testing, we found that a two-part polyurethane from Wevo-Chemie (a German company for tailormade casting, bonding and sealing resin solutions) had the highest thermal performance, so it became a critical component in our system as an adhesive.
For any battery pack, you have to balance the need to take away heat from the system while dealing with the high-voltage electrical challenge. Usually things that are good at conducting heat are also good at conducting electricity. Optimizing for those two goals is a fundamental challenge of any battery pack design, so this implementation with the Wevo-Chemie material is part of our solution to improve that tradeoff, because it conducts heat extremely well and at the same time has a high dielectric strength – so it’s also electrically insulating.
It has good mechanical properties and is rated as flame retardant. It’s not super-stiff when it is cured, so it has mechanical give. And it was also cost-effective. All of these things made that a very desirable material.
Rob Sweney: The Wevo mixture we chose contains special inorganic fillers. Many thermally conductive adhesives have slivers of aluminum filler, however aluminum works against the dielectric barrier. A thermally conductive ceramic, on the other hand, can help achieve both goals. So we found a great material, but then ran into some challenges working with it in a production environment.
Kevin Kim: Basically, the resin has the consistency of peanut butter – it’s extremely viscous or thick. Also, the hardener component of the two-part mixture has a very low viscosity, about the consistency of water. That, [together with the challenging 100:8 mixing ratio of the material] makes it difficult to dispense.
So it was a pretty unique material that we wanted to use and, thankfully, Scheugenpflug was able to help by customizing its dispensing equipment specifically for this material. In fact, they were the only company we found that had successfully dispensed this material before. And they were the only company that was willing to tackle trying to build up a production machine for us to dispense it.
They provided things like the material storage tank, the CNC dispensing robot, and a metering head which accurately measures the two components and is able to withstand the viscosity and the abrasiveness of the filler in the resin and the low viscosity of the hardener at the same time.
Charged: What exactly were the technical challenges for the adhesive bonding dispensing equipment?
Christian Geier, GM at Scheugenpflug USA: When an adhesive contains a lot of filler material, in this case inorganic fillers, it can increase the complexity of the production equipment. For instance, the inorganic fillers can be incredibly abrasive and quickly wear out dispensing machine components. Depending on the material, each system is designed based on the needed application.
You also have to constantly recirculate the material to prevent the microspheres from settling. And to achieve a homogeneous mixture, it’s important to recirculate all the way down to the final valve right before it dispenses. In other words, you have to fight gravity, which is always forcing the filler to settle on the bottom. The less material you dispense the longer it takes to get fresh material in the material hoses, and that’s why material is continuously recirculated.
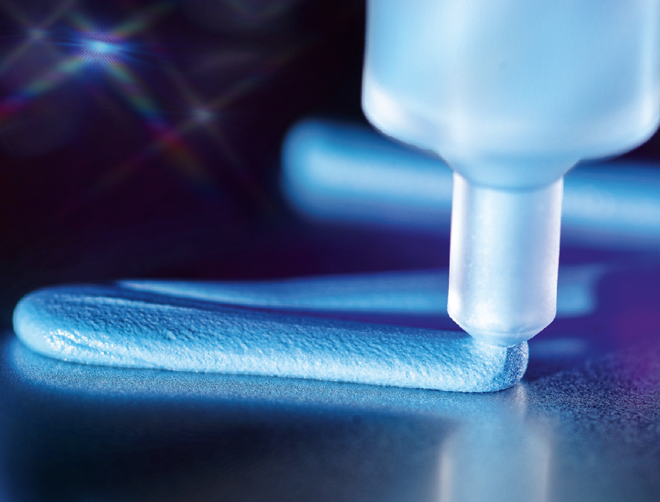
A uniquely viscous material will also require some reprogramming. The fillers can get caught in the head, which causes issues with the mix ratio and the dosing amount because it will start to dispense less filler out of that head. So it requires careful programming to flush the head appropriately. It depends on the cycle time, the dosing amount and length of the material hoses.
In a vehicle production environment, it’s also really important to minimize equipment downtime. We’ve seen cases where other dispensing equipment runs for a very short period – less than an hour – before you need to break it down and clean it. We aim to have production equipment that could run for months, like a tank.
This application and collaboration effort with Alta Motors is also quite different from most battery pack adhesive dispensing equipment needs. It’s a very specific kind of thermal insulating material-containing battery pack. In general, most vehicles have a large, flatter surface area. Alta’s pack is more 3-dimensional, and the adhesive material is supporting it in multiple directions. In an off-road motorcycle, things are being knocked around like crazy.
This article originally appeared in Charged Issue 31 – May/June 2017 – Subscribe now.