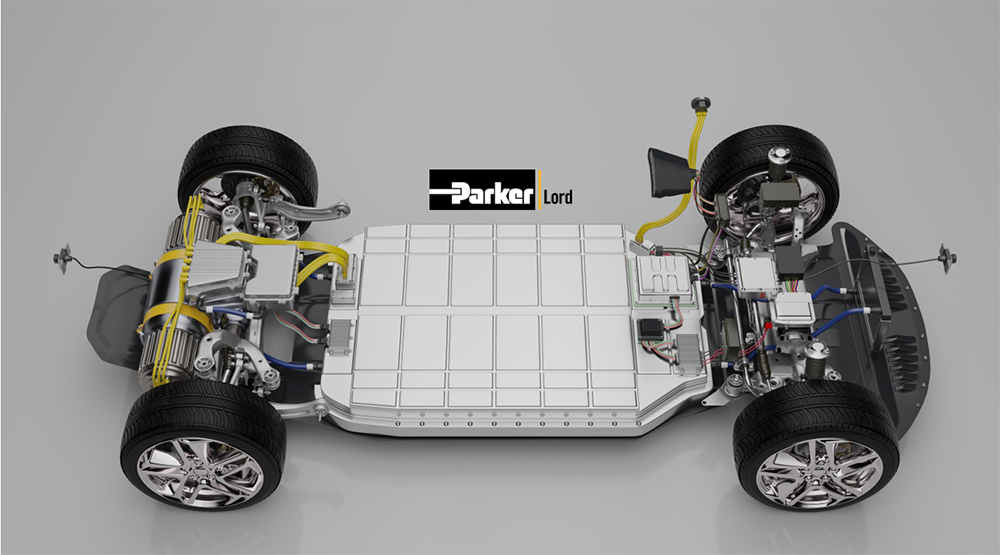
The demand for electric vehicles continues to increase, with EV sales growing faster than any other major category of automobile. According to an article in Forbes, 2023 was the first time more than 1 million EVs were sold in the U.S. in one calendar year, reaching between 1.3 million and 1.4 million cars by year end.
Thermal management is a critical requirement for the safety and performance of EVs. Poor thermal management may result in thermal runaway events, creating a hazardous fire condition. Also, poor thermal management reduces the electronic components’ efficiency because excessive heat increases electrical resistance and lowers the power and energy of the EV. It is, therefore, important to remove heat from battery and powertrain components efficiently.
What is Battery Safety?
Generally, battery safety encompasses protecting the battery system from several adverse circumstances – electrical, thermal and environmental conditions. The purpose behind battery safety is to provide a safe and reliable battery pack operation in all situations, as well as minimize the losses in case of hazardous events such as battery thermal runaway.
Safety Hazards
Electrical safety: With high voltage components in an assembled battery pack, it becomes highly important to keep those high voltage components isolated. Otherwise, an arcing event or electrical short can compromise battery life and even worse can lead to thermal runaway and eventual battery fire. Such electrical isolation can be incorporated in a battery pack with use of dielectric coatings, gap fillers and seals.
Thermal hazards: The Li-ion batteries operate most efficiently within a tight temperature range of 20 to 35 °C. Due to electrochemical reactions within a battery while it is charging or discharging, a lot of heat is generated. If the heat dissipation is not managed property, that can compromise battery performance and in worst case, lead to thermal runaway. A well-engineered active temperature control system allows for battery pack to operate in optimum temperature range. The efficient temperature control is provided by thermally conductive and electrically isolating interface materials. These are applied in between heat source (battery) and heat sink (cooling plate/ribbon).
Environmental isolation: The high-voltage batteries can be sensitive to moisture. The individual battery packaging allows for moisture isolation. However, redundant solutions must be incorporated in battery pack design for additional safety against moisture. Structural adhesives, extruded seals, molded seals, and dispensed seals can be used to seal battery modules and packs. Additionally, the batteries contain toxic components, such as fluorinated electrolytes and transitional metals which can contaminate water supplies and ecosystems. The seals provide enclosure for containing these inside the pack until it can be disposed of adequately.
Battery Thermal Safety
The safe operating temperature range for batteries is defined as between -40 °C (-104 °F) and 80 °C (176 °F). The best performance is found between 20 °C (68 °F) and 35 °C (95 °F). Operating at the extreme temperatures is dangerous and can cause a fire.
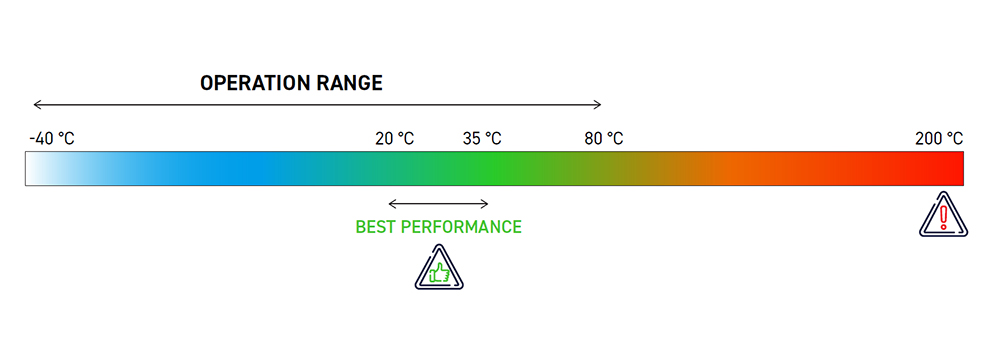
Causes of Battery Thermal Runaway
- Thermal Runaway is described as an uncontrolled increase in cell temperature caused by exothermic reactions inside the cell.
- Thermal Runaway Propagation (TRP) is the sequential occurrence of thermal runaway within a battery pack triggered by thermal runaway of a cell in that battery pack.
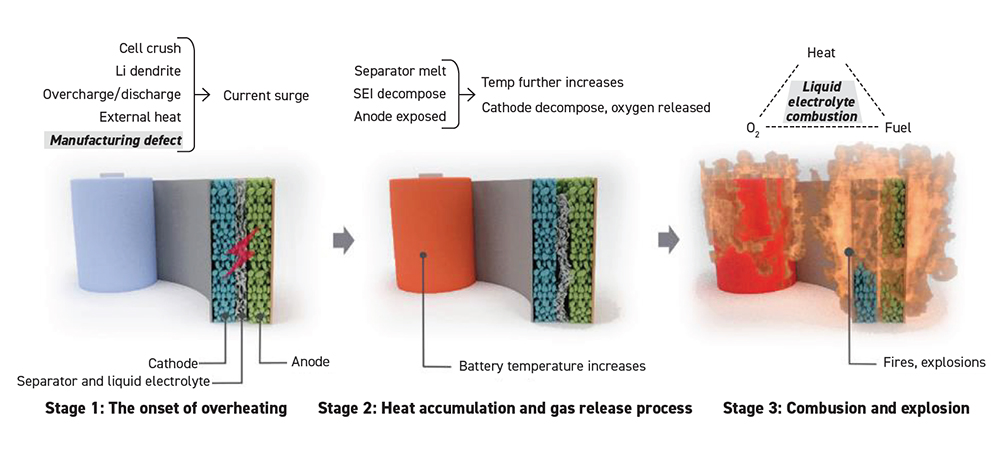
The scientific consensus on the thermal runaway of Li-ion batteries is still developing. However, there is a still wealth of literature to provide a broad understanding of the process happening inside a cell that leads to its thermal runaway.
The onset of overheating is most likely caused by a manufacturing defect that leads to internal short and a consequent current surge. Such internal short can also result from cell crush, Li dendrite formation, overcharge/discharge, or external heat. The current surge produces spike in temperature. If not dissipated quickly, this results in separator melt, SEI layer decomposes, and anode is exposed. As the temperature increases further, cathode decomposes, and oxygen is released from cathode lattice structure. A self-sustaining fire cycle is formed with fuel in form of electrolyte, oxygen and heat. At an onset-temperature, the cell blasts into a fire and if this heat, fire and gases are not managed properly, this can cascade into thermal runaway of neighboring cells.
Regulatory Landscape on Thermal Propagation
Regulations on battery safety have been advancing throughout the world in last decade. UN EVS-GTR No. 20 Phase I was enacted in 2018 that among other battery safety protocols, enacts a 5 min warning to passenger after thermal runaway of first battery is detected. Since then, the regulation has been adopted in Europe and USA. China enacted GB 38031 in 2020 that adopted the same 5 min warning. India enforced regulations around battery safety through their AIS 038/156 enactment in 2021. It describes various safety test for batteries and battery pack. However, no 5 min warning is required.
Currently, US, Europe, and Japan are working towards Phase II of UN-EV GTR No 20, which is anticipated to come into effect before end of this decade. The expectations are the regulations will become more stringent around battery safety, with possibility of introducing no thermal runaway propagation.
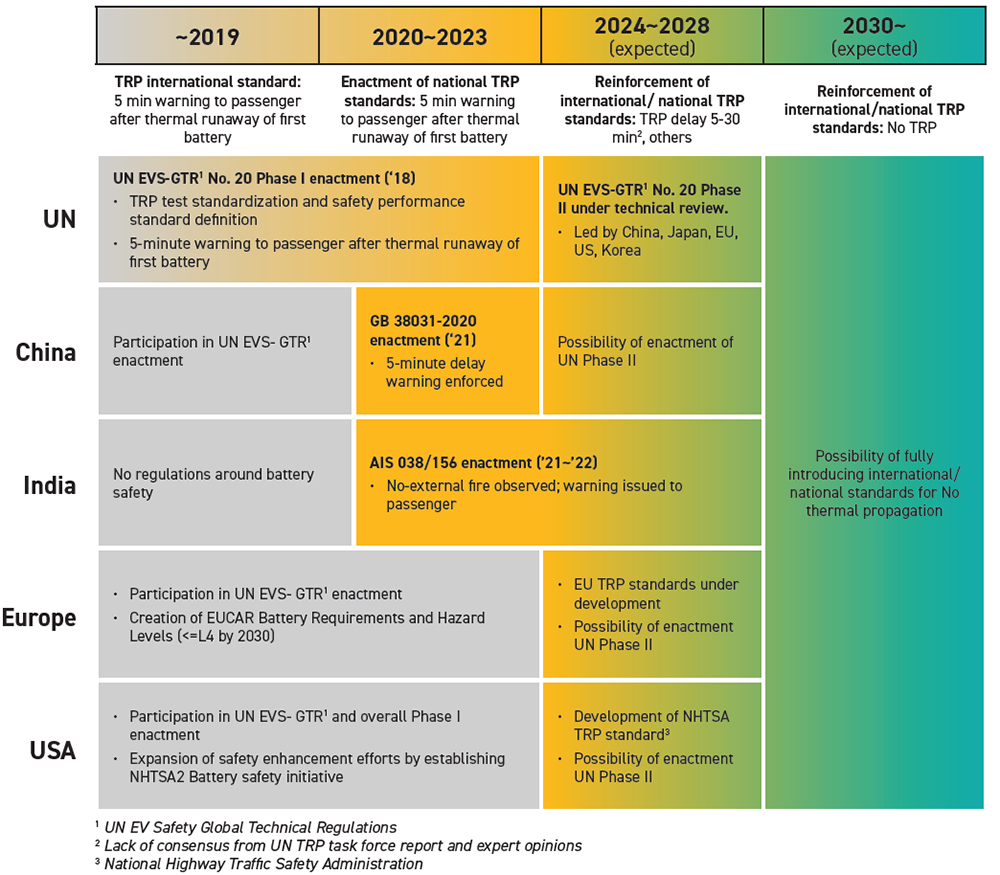
Operational and Thermal Runaway Safety Solutions
To protect the EV battery, Parker Lord has taken several steps to reduce the threat of thermal runaway. These solutions can be seen in the assembly around the battery.
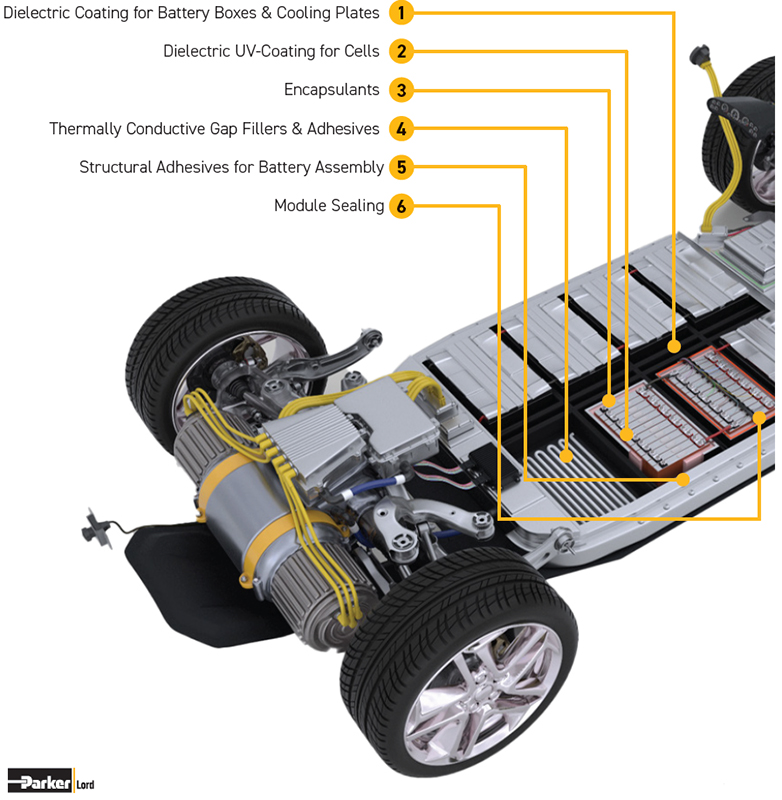
1 & 2 (Coatings): Coatings for batteries are available as a dielectric epoxy coating or ultra-violet (UV) cure dielectric coating. Application areas for coatings include the cooling plate, battery pack enclosure, prismatic cell can enclosure and cylindrical cell can enclosure. Higher energy density requires powerful high-voltage batteries. Higher voltage therefore requires greater precaution in preventing arcing between electrical components and a need for increased battery safety. One major area of focus to achieve this is to improve electrical isolation by using dielectric materials, such as Parker Lord’s Sipiol UV cure coating and heat cure epoxy coating.
3, 4 & 5 (Thermal Management Materials): The most used thermal management materials are gap fillers, thermally conductive adhesives, as well as potting and encapsulants. These materials are used on the cell-to-cooling plate, module-to-cooling plate, intra-cell potting, and enclosure potting. Parker Lord’s CoolTherm® thermal management portfolio is recognized for its reliability and custom solutions for use in electric vehicles, energy storage systems, motors and other power electronics. These solutions increase performance, reliability and safety while delivering tailored products to manage the heat and increased power density in electric vehicles.
6 (Sealants & Adhesives): Structural adhesives and sealants for thermal management include the use of non-reworkable adhesives as well as reworkable sealants. They are used for enclosure bonding and sealing as well as module bonding and sealing. Parker Lord’s adhesives provide a structural bond and reduce the amount of mechanical fixturing required. They also allow greater design flexibility and the ability to bond dissimilar substrates. These structural adhesives can provide a structural or non-structural seal for battery modules and packs to keep battery cells protected from the elements and improve safety.
Your Partner in Innovation
Innovations in materials and technologies play a crucial role in advancing the reliability, efficiency and safety of electrified transportation. Thanks to their market leading safety solutions, Parker Lord works together with their customers to propel the transition toward sustainable and electrified transportation ecosystem.
If you have questions, reach out to Parker Lord today.