In a joint study, German chemicals company Henkel and engineering consultancy RLE International have examined the potential of high-performance structural foam for lightweighting in automotive body and closure parts. Henkel says the study shows that fiber-reinforced polymer components with structural foam ribbing and reinforcements can save more than 40 kg of weight per car compared to conventional all-metal designs.
The hybrid parts feature a solid frame or carrier molded in higher percent fiber-reinforced polymers (FRP) and selective reinforcements using Henkel’s Teroson EP structural foam, a commercially available epoxy-based material that delivers high strength and stiffness at low weight. The foam is injected into the carrier at predefined sections, expands in the e-coat oven, and creates a stiff connection between the hybrid component and adjacent parts in the body-in-white.
The project studied all major body and closure parts of an SUV, from the bumpers, fenders, pillars and doors to the rocker panel, side panels and tailgate.
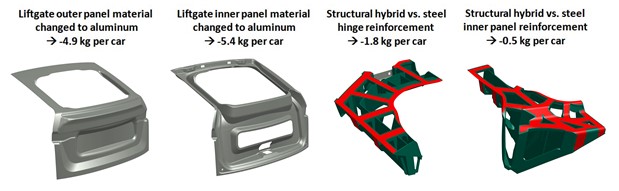
The crash simulations performed in the study adhered to international automotive standards, such as offset and small overlap frontal crash testing as laid out in the European New Car Assessment Program (Euro NCAP) as well as the Insurance Institute of Highway Safety (IIHS) at speeds of 64 and 50 km/h, respectively. The side crash performance was tested according to US NCAP specifications at 32 km/h. The rear impact scenario was simulated with a 60 km/h moving barrier onto a fixed test vehicle as defined by US Federal Motor Vehicle Safety Standard No. 301.
RLE and Henckel found that the hybrid designs with Henkel’s Teroson EP structural foam passed all these tests well within the limits of deformation and intrusion, while at the same time offering weight savings compared to conventional all-metal designs.
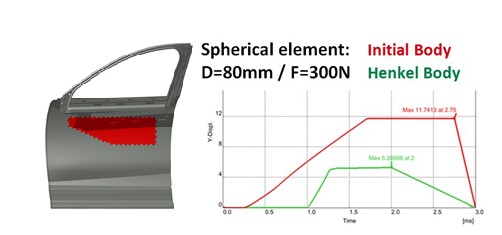
David Caro, Head of Global Engineering at Henkel, said, “The results of our study have confirmed that we can achieve significant further weight reductions without compromising the safety in typical crash scenarios by optimizing the stiffness of fiber reinforced plastic frames or carriers with selective foam ribbing and reinforcements, with competitive costs.”
Source: Henkel