Rivian has been generating a lot of headlines since the November 2018 reveal of its prototype pickup and SUV. The company has scored substantial investments, including $700 million from a group of investors led by Amazon and another $500 million from Ford. That cash was accompanied by a history-making order of 100,000 electric delivery vans from Amazon and plans to partner with Ford to build new EVs (including a rumored electric Lincoln).
Charged recently chatted with Rivian’s VP of Propulsion Richard Farquhar to learn more about the design and development of the company’s unique electric platform (you can read the whole story in our upcoming issue).
Farquhar described how Rivian engineers were able to achieve unprecedented energy density.
Richard Farquhar: We have what we believe is currently the highest volumetric energy density modules and pack in the world. It’s about 20-25% greater energy density in watt-hours per liter compared to anything on the market today.
What has allowed us to achieve this is the construction of the module. Each module has two layers, each containing 21700 type cylindrical cells. So, we’ve got 15 kWh of energy in each module. There are 9 of those modules in our standard pack, and we have 12 of those in what we call our premium pack of 180 kWh, which gets us over 400 miles of range.
At the heart of the module is a cooling plate between the upper and lower cell layers. That allows us to control the cooling of those cells in their most efficient medium, which is cooling axially. We pull the heat out of the cell through its center, which is the most efficient way to do it, as opposed to radially. It allows us to pack those cells really close together. This allows us to get the highest volumetric energy density available today.
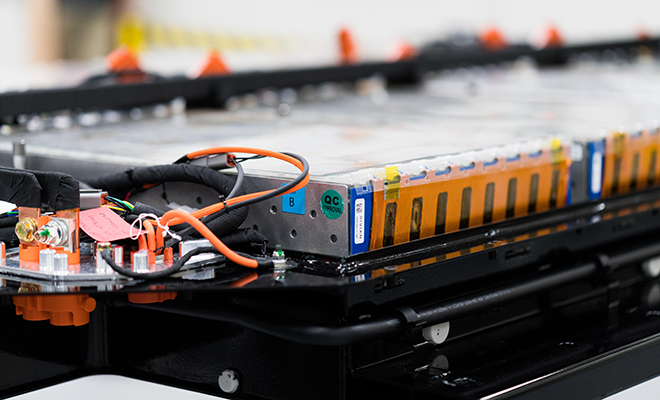
Because it cools the cells axially instead of radially, Rivian was able to design its modules with only air between the cells. There are no liquid cooling channels (or other thermally conductive materials) weaving between the cells like the ones Tesla and others have used.
Rivian is set to launch production at the end of next year. Farquhar told Charged the team is currently in the validation, reliability and durability testing phase with “tens” of production-intent vehicles.