Elaphe Propulsion Technologies, a manufacturer of in-wheel electric propulsion systems, and HFM, a developer of mechatronics systems for electric and autonomous vehicles, have announced a new partnership. HFM’s autonomous EV platform Motionboard will now incorporate Elaphe’s in-wheel motor technology.
Motionboard is a modular and scalable platform that’s used as a base for building autonomous EVs. The platform can be modified based on the vehicle’s requirements of length, width, mass, and battery capacity. Motionboard is road-legal and meets European requirements as an M1 Class vehicle, a passenger vehicle with up to eight seats in addition to the driver.
Now, Motionboard’s propulsion will be provided by Elaphne L1500 direct-drive hub motors.
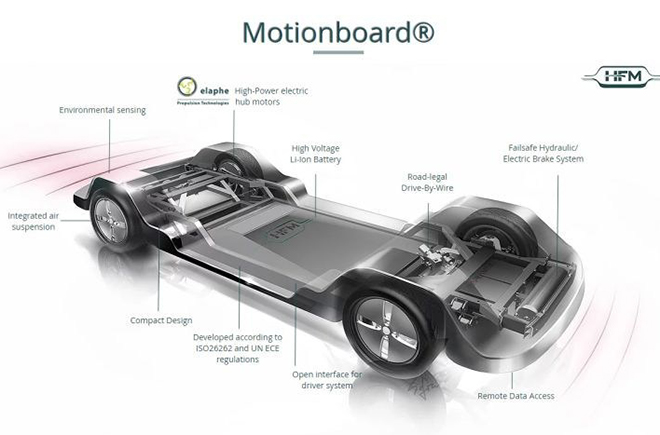
“Elaphe’s in-wheel motors operate at over 90 percent efficiency and allow us to achieve extended operating ranges,” said Marcus von Wilamowitz, Head of Electrical Integration and Functional Safety at HFM.
“Our in-wheel technology is put through extensive automotive validation under a wide range of demanding operating conditions and loads,” said Urska Skrt, Head of Business Development at Elaphe. “Elaphe’s patented electromagnetic topology allows our motor design to be highly scalable, light-weight and the most compact on the market. Combined with intelligent motor control, it is the most simple and modular electric vehicle propulsion that enables ultimate packaging and user-centered design.”