Sponsored by AVL
Because integrated validation is only carried out during vehicle tests, development and validation of individual electrical components and the interaction of the overall system is often time-consuming. Using integration test stands, AVL is changing this process for electric drives.
The majority of OEMs examine electrical and electronic drive components individually during the development process of the entire system, with road validation typically occurring after the components have been fully integrated into the vehicle. However, vehicle tests are time-consuming, expensive and not easily duplicated. If a vehicle test conducted late in the development process indicates an issue, it can be quite costly to change any of the components in the system when they’re already that far along. AVL closes this gap with its integration test stand: the AVL E-Integration Test System.
Mario Propst, an AVL application manager, explains, “The timing of joint tests is shifted significantly forward through the test bench. The integration team can identify and solve problems together with component managers at an earlier stage, and not only during practical field tests – giving them the ability to decrease validation efforts by 30%.”
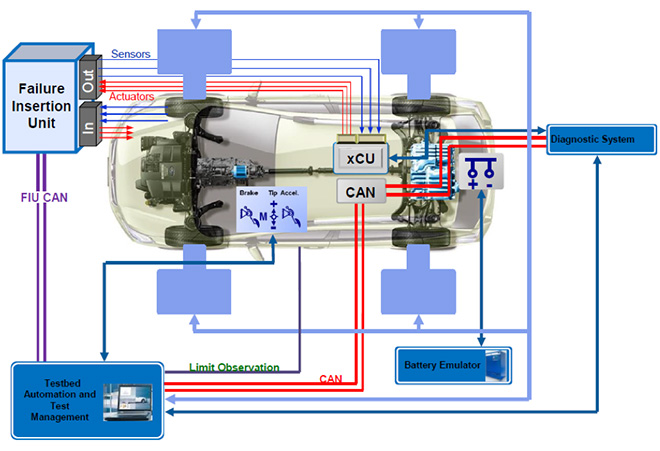
Figure 1: Functional testing on a 4-wheel integration testbed allows the robustness of software, hardware and their integration to be validated.
With this type of testbed, the real components of an electric or hybrid propulsion system can be validated in a laboratory environment. Automated emulators can replicate stress on the system in the laboratory, making it possible to effectively and reliably validate its robustness and fail-safe features. Climatic chambers, for battery and power electronics, are also used during stress tests to simulate extreme climatic conditions, as required.
“Emulators allow test specimens to be reproduced and tested within their boundary conditions; this is not possible with production components,” said Propst. “The battery emulator can, for example, supply the drive system with constant voltage, but can also simulate the real behavior of a battery and represent extreme load jumps. These stress tests show whether the vehicle will function reliably even under extreme conditions. Another example is the grid emulator – in which different power-grids can be mapped – allowing car manufacturers to ensure the car can be charged reliably anywhere in the world.”
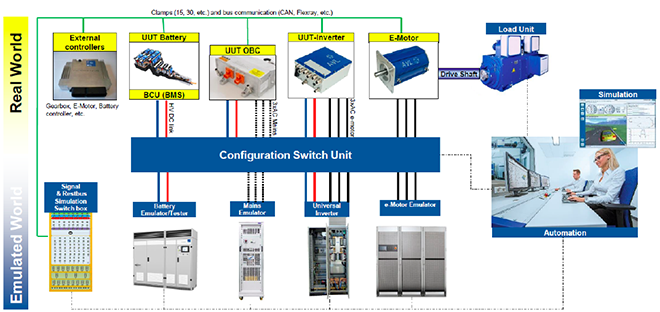
Figure 2: The interaction of real hardware and emulated components allows for complete layers of new test cases and accelerates system validation. Errors are detected and can be solved before the propulsion system is integrated into the vehicle.
Propst also stated, “We have the ability to change the configuration 5-6 times per day without any manual modifications – our system can do this in one minute.”
VEHICLE SIMULATION
Complete vehicle simulation opens a whole new spectrum of test cases. The real drive components are integrated into a simulated vehicle that is directed by a virtual driver on a virtual test track, making it possible to conduct the same tests as those performed on the road. Interactions occurring in the vehicle can influence brand-relevant driving characteristics and can be systematically analyzed and optimized so the systems achieve a very high degree of maturity before the first vehicles even hit the road.
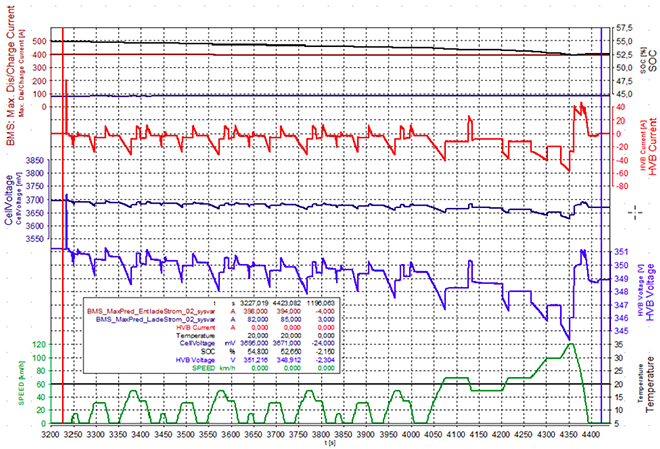
Figure 3: Vehicle simulation allows the execution of true driving cycles (in this case NEDC) under reproducible conditions with different SOC levels. Using those driving cycles, the propulsion concept can be verified without a real battery and the control quality increased at a very early stage during the development process.
“Most importantly, OEMs need to confirm the functional safety of all components responsible for the drive,” said Propst. “How do the components react to an electric cable break? Are the protection concepts working? Can we rely on the high-voltage system to switch off during the event of a crash? It is really exciting when it comes to topics where everything goes together, like the forward-looking energy management of hybrid vehicles, where driver assistance systems also play a role. We can analyze such functions using the AVL E-Integration Test System in realistic driving scenarios.”
Figure 4: A consistent toolchain from simulation to real hardware testbeds allows a high correlation between test results on testbeds and on the road.
For more information about the AVL E-Integration Test System, please contact:
Gernot Hacker, Gernot.hacker@avl.com