Stamping precision parts for automotive-grade motor manufacturing
The demands of the automotive industry are unlike any other. Carmakers require that their suppliers deliver millions of parts with incredibly tight tolerances that will not fail after a decade of daily use. The companies that manufacture parts for ICEs have grown increasingly sophisticated and disciplined in the past 50 years.
EV technology suppliers have had some catching up to do. For example, there are large global companies that have been producing parts for electric motors and power electronics for a long time. However, they quickly learned that the automotive world is quite different than the industrial applications and consumer appliance markets they’ve been supplying for decades.
“When this e-mobility movement started, the first-generation motor designs were based on the best industrial motors,” Erik Hilinski told Charged. Hilinski is Senior Director of Steel Technology and Quality at Tempel, an independent manufacturer of precision magnetic steel laminations for motors, generators and transformers.
“Since then, the engineers in the auto industry realized they could do much better than building around an industrial motor,” said Hilinski. “So they redesigned the motors to run with ideal working points and deliver the best torque and efficiency for any given car.”
At this point in the history of the EV industry, a lot of design decisions are still driven by range. A 0.50% improvement in motor efficiency is something that automakers will pay a premium for, because it directly translates into getting more range without increasing the size of the battery pack. Some automakers are now in their third-generation design phase, continually pushing performance of these systems to the next level of torque, speed and efficiency. To get there, engineers are incorporating new steel formulations and the latest and greatest motor designs and topologies.
Electrical steels are soft magnetic materials found at the heart of electric motors. They’re typically manufactured by steel mills in cold-rolled strips. Tempel’s job is to stamp steel into precisely-shaped thin laminations, which are then stacked together to form the stator and rotor of a motor. The company works with many different steel suppliers to help meet the demands of auto OEMs.
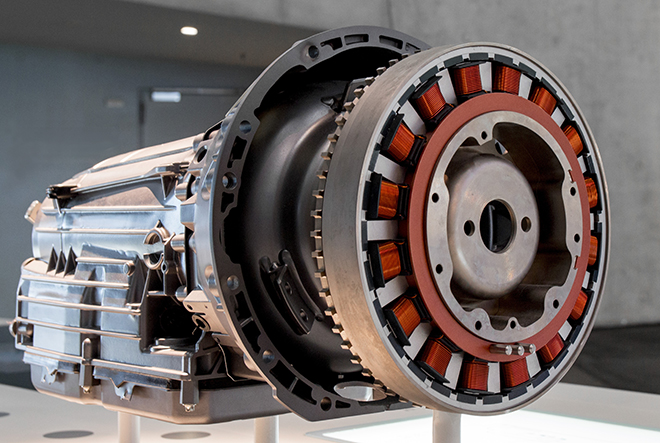
Better factories for tighter tolerances
In first-generation EV motor designs, Tempel explains that the gap between the stator teeth and the outer diameter of the rotor, which is the rotating portion, was in the 1 mm range. “The designs have become progressively tighter,” said Craig Woodard, Tempel’s Director of Global Manufacturing Engineering. “Because the closer you move the magnets to the outer diameter, you’re essentially creating more torque, you’re going to get better transfer of the flux or the electrical energy between the rotor and stator. So now you’re seeing designs with gaps as small as 0.4 mm.”
There is also a trend toward using thinner sheets of steel, because the thinner you make the electrical steel, the better the magnetic characteristics of the material are. Woodard said that most of the steel that Tempel stamps today for industrial applications is in the 0.50 to 0.72 mm range, whereas hybrid and EV designs are typically sized at 0.30, 0.27 and 0.25 mm.
These may seem like simple specification changes, but the tightening specs have presented significant engineering challenges in manufacturing.
“First of all, at 0.25 mm you’re nearing foil thickness,” said Zach Leveston, Tempel’s Senior Director for Global Engineering. “So, the technical complexity of stamping material that thin is much different than thicker steels used for traditional industrial motors.”
“As your laminations get thinner, it gets more difficult to make a nice clean cut, and the tooling tolerances have to be tighter and tighter,” added Hilinski. “So as things get smaller, complexity builds upon itself. It’s an additive effect.”
To meet the specs of performance EV designs, Tempel has developed unique capital equipment to support both the stamping and annealing processes. A 0.25 mm strip doesn’t have much rigidity, particularly when you’re trying to move it through a stamping die as fast as 250 strokes per minute. Special strip feeding equipment is required. And, as the lamination geometries become more complex, the stamping dies to produce the parts get longer. This necessitates stamping presses with longer press beds, more rigidity and better accuracy, which Tempel is specifying for all new production lines supporting hybrid and EV requirements.
“There is also a meaningful reduction in output as the laminations get thinner and thinner, which can add to the cost of the rotor and stator cores,” said Leveston. “If you think about a stamping line or a steel mill that goes from producing a 0.30 mm thickness to 0.27 mm, they lose 10% of their effective capacity. You will need 10% more laminations to build the same size stack.”
Tempel says it has developed a unique annealing process that can help motor designers meet efficiency specifications while using thicker steel sheets or alternatively improve torque and efficiency output at the same material thickness. Basically, it’s a heat-treating process, but instead of trying to induce better mechanical characteristics (which is common in the steel industry), the process is designed to induce better magnetic characteristics.
“This is an area where Tempel has a very unique core competency,” said Leveston. “As the steel gets thinner, it makes the magnetics better, which makes the motors more efficient. What we’re able to do with our annealing process, for example, is take a 0.30 mm material and anneal it to have the magnetics of 0.27 mm material. Basically, it creates effective capacity for the steel mills without our customers having to sacrifice the magnetics for the thicker steels.”
To manufacture top-of-line motor laminations, Tempel created a new top-of-line factory design that’s intended to be easily replicated in different regions as the demand grows. The first new factory, built in China, is predominately focused on making rotor and stator cores for hybrids and EVs.
“The factory has all new state-of-the-art capital equipment, and both temperature and humidity are tightly controlled,” said Leveston. “The tolerances for new traction motor designs are in some cases twice as tight as they were just five years ago. To ensure that Tempel is capable of meeting those requirements, we are controlling every variable in the production process, including environmental conditions, to minimize process variability. We also have a positive-pressure environment and an air filtration system cleaning the air 8 times an hour to meet emerging technical cleanliness demands for traction motor applications.”
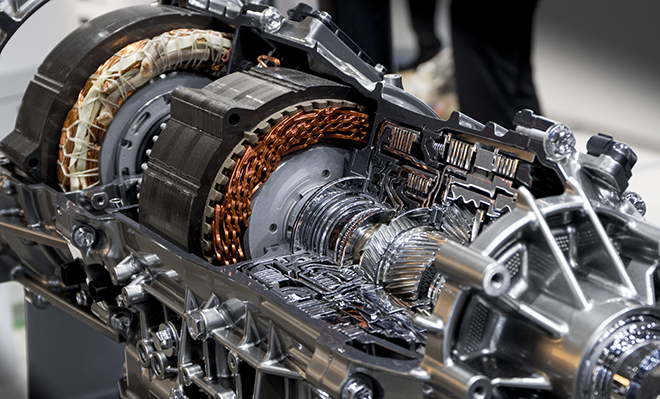
Selecting the right steel
Electrical steel is a unique class of materials and a niche product. While there are industry specifications which define performance, such as ASTM standards in North America, IEC or Euronorm for Europe, and JIS for Japan and Asia, the specified magnetic properties provided in these specifications used for grading purposes are not comprehensive enough for motor design. That kind of magnetic material performance data is not readily available in the public domain and must be requested from the steelmakers.
“Total steel production in 2017 was about 1.4 billion metric tons,” said Leveston. “Electrical steels was only about 20 million metric tons. If you think about what people care about with steel, generally, it’s mechanical properties. But in the electric motor application the mechanics are really secondary. What we really care about is magnetics.”
So, Tempel set out to compile the data itself. The company has an ongoing project to characterize magnetics for all the different electrical steel grades it can get its hands on. That is the primary function of the team Hilinski leads at Tempel, and his group has now assembled a database of over 1,800 steel samples.
“We’ve evaluated the full magnetic characteristics of these steels,” said Hilinski. “This gives us the ability to sit down with a customer and say, ‘Let’s talk about the operating points of your motor. What’s more important to you? Do you want high torque? Do you want high efficiency?’ Based on that, we can send them data on three or four different steels which we think may be suitable. We actually send them the magnetic characterization of those steels, which they can just upload into their electromagnetic FEA simulation.”
Tempel estimates that there are about 25 steel mills in the world that are producing steels for hybrid and EV applications. Each of those mills may have many variations of electrical steel products that all require testing, and Tempel says it has magnetic performance data on nearly all of them.
Before joining Tempel, Hilinski was a Technical Manager at the US Steel Research and Technology Center – a leading supplier of flat-rolled steel – where he worked on developing different types of electrical steels.
“Tempel maintains strong commercial and technical relationships with all major electrical steel mills globally,” said Hilinski. “For our customers, we’ll open up our full catalog of test data to find whatever will work best. Oftentimes a customer will come to us with designs that spec a specific steel from a specific mill, and we can show them with our data that a different steel from a different mill may actually provide better performance or be more cost-competitive.”
These are very expensive steels – typically two to three times the price of a traditional coil of 1008 or 1010 material – because of how highly engineered they are and the R&D work that’s required to develop them. Since the cost of the raw material is the dominant portion of the lamination’s cost structure, it’s critically important to choose raw material wisely. That’s why Tempel will continue to invest in evaluating new grades of electrical steels for hybrid and EV applications so it can provide the best application engineering support possible to its customers.
This article originally appeared in Charged Issue 39 – September/October 2018 – Subscribe now.