Much as humans need a heart to distribute energy throughout our bodies, EVs need a heart to transfer energy from their batteries to their motors. This “heart” of an EV is called a power module, and it’s responsible for driving the vehicle’s propulsion unit as efficiently as possible.
Considering the critical importance of power modules, you can be sure that many companies are continually working to make them better. The engineers at Mitsubishi Electric, for example, have developed a technique called direct lead bonding (DLB), which they say will provide meaningful increases in reliability.
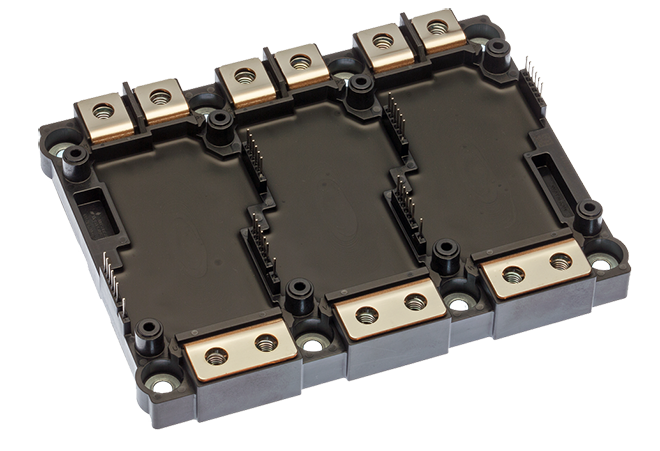
Direct lead bonding
Power modules incorporate a number of power semiconductor components, often in the form of insulated gate bipolar transistors (IGBTs). Although these components can be arranged in many different ways, a common topology involves six components interconnected in what’s called a six pack.
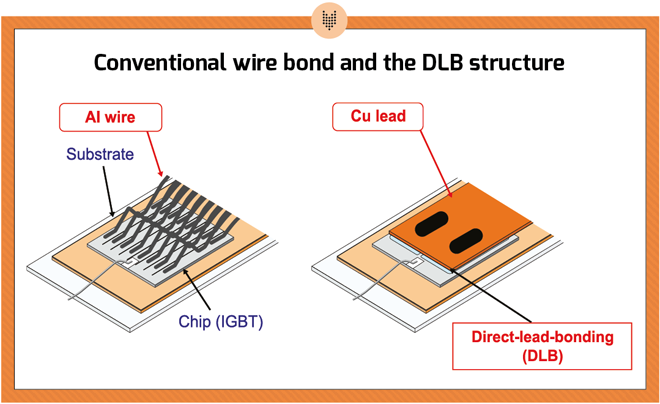
Mitsubishi Electric’s DLB technique concerns the way in which a power module’s IGBTs are connected together and to the device’s power terminals. Typically, these interconnections are made with aluminum bond wires. “In traditional large power modules, multiple small aluminum wires join the chips in whatever topology the module executes,” explains Adam Falcsik, Product Line Manager for Mitsubishi Products and Accessories at Powerex – the North American branding for Mitsubishi Electric products. “They connect the emitter of the upper device to the collector of the lower device, and so forth.”
In contrast, DLB replaces the aluminum bond wires with a single copper lead. “Rather than using multiple small aluminum wire bonds, we use a single thick copper bond that is attached to the surface with a solder layer,” says Falcsik.
Improving reliability with DLB
Why use DLB over aluminum bond wires? As Falcsik explains, aluminum wire bonds are one of the primary points of failure in conventional power modules.
“There are two main failure points in power modules, a thermal cycle limiting feature and a power cycle limiting feature,” says Falcsik. “The thermal cycle limitation concerns the overall heating and cooling of the system, and the power cycle limitation concerns the short excursions you’d see in the pulse-width modulation-type timeframe.”
DLB is used to improve the durability of the power cycle. With aluminum bond wires, the power cycle is limited by a predictable failure at the junction between the bond wire and silicon chip. Falcsik claims that in power modules with DLB, this weak point is eliminated. “Rather than having all these localized hot spots on the chip surface, it’s much more evenly distributed, and so is the current flow. So rather than having to flow through these points where the wires bond, the whole surface can be utilized.”
Consequently, because the power cycle typically fails before the thermal cycle, power modules with DLB benefit from increased longevity. “With DLB, the thermal cycle reliability becomes the driving force of the lifetime of the module. So rather than having to counterbalance these two features, now we can move our lifetime curve out to the thermal cycle threshold.”
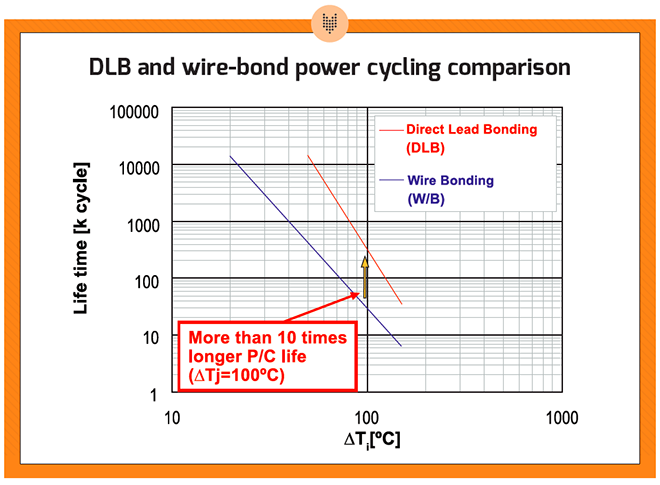
While DLB improves power module reliability, it can come with an increased cost over some aluminum wire bonded alternatives. However, Falcsik is confident that EV manufacturers will see the advantages of the more reliable DLB approach.
“Reliability is something the market is still trying to get a handle on, because they haven’t had a lot of long-term vehicles out there that are fully electric,” says Falcsik. “That’s something that we’re always selling: reliability over the lifetime of the vehicle. We’ve seen customers that are more in tune with the rigorous demands of an EV, and they tend to understand the benefits that our module can offer. Whenever they’re doing a side-by-side comparison of us and a competitor, they better understand the benefits.”
Mitsubishi Electric has published a paper on its latest six pack IGBT power modules, called the J1-Series, in which they demonstrate some impressive results. In this paper, DLB was shown to achieve ten times as many power cycles as conventional modules with aluminum wire bonding.
The J1-series offers a number of benefits over conventional transfer molded power modules (T-PMs). According to Mitsubishi Electric’s paper, the J1-Series achieves a 76% weight reduction, 40% footprint reduction, and 30% improved thermal performance over T-PM solutions.
Customer configured
With a number of major automakers as clients, Mitsubishi Electric has to provide power modules for a range of automotive needs. Ultimately, the customers drive the choice of specs. “We’re able to support customers that are chasing the high horsepower goals, but we’re also able to support somebody designing a people’s car, a commuter. So we need to have a range available to meet the range of vehicle requirements,” says Falcsik.
With these different demands from different customers, Mitsubishi Electric has developed several ratings and packages in the J1-Series. “In the smaller package, which we call our J1 package, there’s a 600 A, 650 V six pack device,” explains Falcsik. “There are multiple other ratings in development, and we work closely with potential customers to zone in on exactly what those are, but right now we’re developing a 700 A, 650 V device, and possibly a 1,200 V device.”
According to Falcsik, the majority of Mitsubishi Electric’s power modules are still produced for hybrids and PHEVs. However, for manufacturers of pure EVs, Mitsubishi Electric offers a more powerful module called the HPJ1. “In the larger HPJ1 package, we are currently in the final development stages for our 1,000 A, 650 V device, as well as a 600 A, 1,200 V device. So the HPJ1 is really focused on fully electric vehicles, not a hybrid-type solution.”
Whether an EV or a PHEV, a high-horsepower dragster or an efficient commuter, all electrified vehicles can benefit from more reliable power modules. As the heart of the electric powertrain, these modules have the same bottom line as our biological tickers: the longer they last, the better.
This article originally appeared in Charged Issue 32 – July/August 2017 – Subscribe now.