Electric motors are everywhere: in household appliances, in hand tools, in buildings, in consumer electronics, and increasingly in automobiles. Motors are used in windshield wipers, power windows, throttle controllers, and, more and more, in the drivetrains of electrified vehicles.
Electric motors abound, and Odawara Engineering knows how to make them. Charged spoke with Odawara’s Chris Spejna about the design of electric motor manufacturing lines and how automakers may adapt to the new technological landscape in the years to come.
Charged: Why do the automakers need help from companies like Odawara? Don’t they employ an enormous number of engineers?
Chris Spejna: If you go back 30 years ago, Ford, GM, Chrysler, made most of their own motors – wiper motors, window lifts, HVAC, Cooling fans, etc – but as they got into the 1980s, they realized they couldn’t make affordable motors anymore, mainly due to the increase in labor costs at the time. So the OEMs started to outsource to Tier 2 or 3 suppliers. Over the years, through attrition they lost a significant amount of engineering expertise, and now they are investing heavily to rebuild their electric motor competency, especially in the EV-HEV Traction Motor area.
At this point, however, they rely on us and other very competent suppliers. At this time, EV traction motors are not a commodity item. Maybe in 10 or 20 years they’ll be a commodity item, much like a blower motor for a vacuum cleaner. I can go online and see probably 30 or 40 different suppliers of winding equipment for vacuum cleaner motors. You can’t do that right now for electric vehicle traction motors.
Charged: Do you think in 10 to 20 years that major automakers will all have in-house teams to do what you do?
Spejna: They may not make their own winding systems, but they will have much deeper motor design and manufacturing teams to support motor manufacturing as a core competency. If you look at the OEMs, they farm out seats, they farm out tires, they farm out glass, but what’s the one thing they all have in common? They make their engines, transmissions, drivetrain and frame. It’s an integral part of the whole system. I think it’s inevitable that they all invest heavily in the EV and HEV areas. In addition, there are large Tier 1 suppliers that will follow suit and invest in this traction motor area, companies like ZF, Continental, Magnum and Bosch. Some of these suppliers will develop competent teams in-house and work closely with the OEMs.
Charged: How many major EV and HEV projects has Odawara worked on?
Spejna: Our parent company was fortunate enough to work with Toyota to provide the winding systems for the electric motor and generator for the original Prius 20 years ago. Since then, we’ve worked on numerous automation systems, probably in the neighborhood of 29 or more, for the new drivetrain motors for electric and hybrid vehicles.
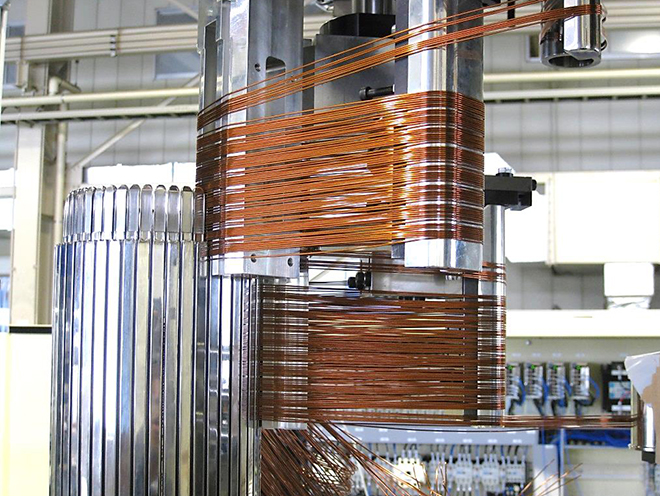
I’ve been with Odawara since 1980. We were originally a small family-owned company called OTT-A-MATIC. In 1986, we were purchased by Odawara Engineering of Japan. In our early years, we concentrated on winding systems for appliances and power tools, and some automotive motors. Primarily universal commutated motors for power tools, gear motors and vacuums. But also a lot of PMDC [Permanent Magnet Direct Current motors] for cooling fans, HVAC for cars, wiper motors, window lifts, seat movers.
For the EV and HEV motors, Odawara focuses on the stator line, the stationary part of the motor. A customer will provide us a design and ask, can you quote a winding system? And we’ll look at it and offer suggestions to make it manufacturable, and then also quote the entire winding system, from start to finish. Then we design the equipment, manufacture, install, and then train the customer’s employees to operate it.
Charged: What are the key metrics that you’re trying to optimize for when designing a line?
Spejna: First is speed and labor – working to lower the labor content. The more automation we can provide does this. Of course, it raises the capital cost, but as we get better at making these systems some of the cost should come down. And anytime you have a person on the line, there’s a variable. They can make mistakes or forget to do a process. The long-term evolution is to get the systems to have a higher per-hour throughput with fewer operators on the line for greater efficiency and quality.
Then there is a range of more technical goals like slot fill efficiency. We work a lot with distributive wound motors, which is what Nikola Tesla developed over 100 years ago. It’s round wire, and we take multiple wires in hand, and we wind them around tooling arbors without twisting the wires and insert the coils for maximum slot fill. I think we’ve got the best technology that’s available to achieve maximum slot fill at a high production rate and manufacturing efficiency. I’m talking about maybe 85% or more for slot fill. Say you need to put 5 pounds in a 5-pound bag – at a certain point the bag’s going to want to rip or tear and you’ll have rework. You’ve got to tape it up when you’re done. And many designers, they just say, well we’re going to fill the slot of the stator with wire. And then at the end of the line, you’ve got some operator trying to salvage what didn’t get in there correctly. And that’s just a waste of time, money, and effort. What we do is, if you’ve got a 5-pound bag, we can get in 4.9 pounds efficiently. And we can do it all the time. That’s the expertise we bring to the party.
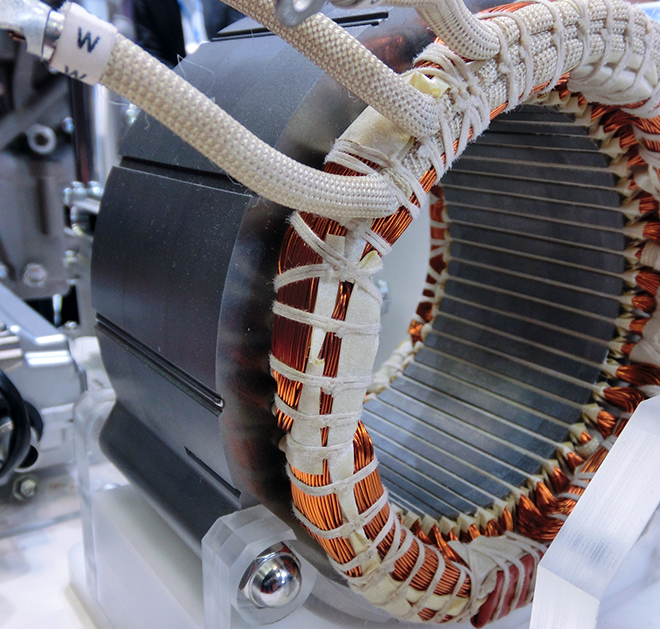
Charged: What are the basic stages of your stator assembly lines?
Spejna: For a distributive wound motor, you start with a stator stack and a lamination stack. And then you have to put slot liners in it, insulation, because you have to insulate your lamination core or stator from your lamination wire. If it shorts out, you got nothing. And then we wind wire, insert the wire, then drift or form the wire to get it out of the way. Typically these 3-phase distributive wound motors require 3 insertion passes. We call them the U, W, and V phases. So you insert U, drift it out of the way, insert W, drift it out of the way, [then] insert V. And then you do a final blocking and form, lace the end turns and fuse the connecting terminals. After a detailed electrical test, it is then trickle-coated with a varnish so it’s one solid mass. These are pretty standard processes.
Charged: Are large traction motors typically more difficult to manufacture than smaller-scale motors?
Spejna: Everything’s related to the physical size, so the equipment gets much bigger. For example, we’ve done winders for little components for cell phones, and you almost need a magnifying glass to see them. And then, for vibrators in cell phones and stuff like that, it’s a little motor about the size of the tip of an eraser. But, typically, the drive motors for an electric vehicle might weigh over 150 pounds, with the rotor and housing and all. So, we’re talking from a traditional fractional horsepower motor being a few pounds if not ounces, to a traction stator that may be close to 100 pounds. So the physical size of the equipment, the complexity of the equipment, and the cost of the equipment, is significantly higher.
Charged: Does that mean automotive is becoming one of the biggest parts of your business?
Spejna: It definitely is. These systems are large. And in addition to designing the equipment, we also work very closely with our customers to improve manufacturability. Everyone wants these systems to work at 99.9%, and, you know, not everything that looks right on the CAD works right in reality. So that’s what’s great about our very knowledgeable staff. We’re probably in the neighborhood of 1,000 years of engineering experience, if you add up all the people who’ve been working on these systems at the company.
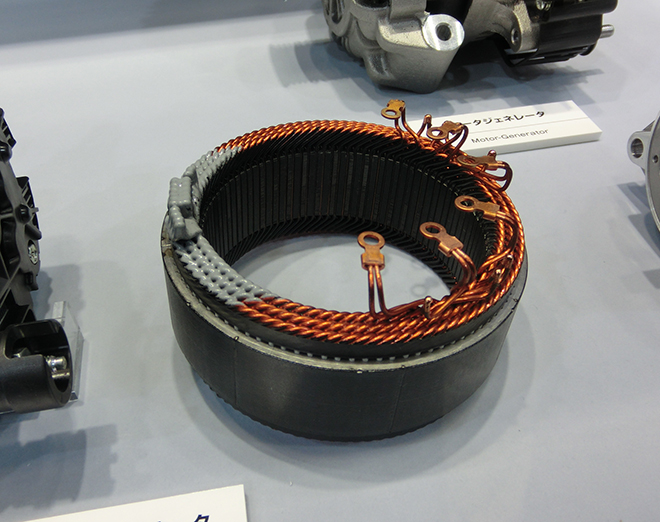
This article originally appeared in Charged Issue 33 – September/October 2017 – Subscribe now.