In 2013, Shafigh Nategh completed his doctoral thesis on the thermal management of high-performance electrical machines at the KTH Royal Institute of Technology in Stockholm, Sweden, and by 2014, the results of his doctoral work had begun to pique the interest of some heavy hitters in the electric motor industry.
For his thesis, Nategh designed an oil-cooled permanent-magnet motor and compared the performance of identical motors when they were either varnished or potted with two different materials. He had seen a talk on LORD Corporation’s new highly thermally conductive, electrically insulating silicone material, Thermoset SC-320, so that was one of the two materials he chose. The other was an epoxy product called Epoxylite, which is widely used to seal electric motors for applications with harsh environments.
The research results, in short, showed that hot-spot temperatures for the motors using LORD Corporation’s SC-320 were 35 to 40° C lower than the motors with just varnish, and 20 to 25° C lower than the motors using Epoxylite.
Naturally, once LORD got wind of Nategh’s findings, the company saw a huge opportunity and far-reaching benefits for electric motors using a thermally conductive material like SC-320, including increased horsepower, longer lifetimes, and higher efficiency.
Charged detailed Nategh’s work back in our June/July 2014 issue. At that time, LORD told us that they were actively working to validate the potential benefits of their thermally conductive materials for electric motors and seeking development partners and early adopters to test prototypes.
We recently caught up with LORD Staff Scientist, Dan Barber, to get an update.
Charged: It’s been about two years since we first learned about Nategh’s thesis and LORD Corporation’s excitement about the results. How has the technology and market matured since then?
Dan Barber: The article Charged published in 2014 was really where customer pull started for our technology. It was there that we announced the plan to begin testing our materials specifically for thermal improvements in motors. That is also when we began to identify customers who wanted to validate the technology with us.
Since that article was published, we have worked with Dr. Keith Klontz and his team at Advanced MotorTech to validate the initial finds. We have also completed accelerated aging tests with the Motors and Drives Test Laboratory at Advanced Energy.
Shafigh Nategh’s PhD work was completed using our SC-320, which is a flexible elastomeric silicone material with high thermal stability and a thermal conductivity of about 3.2 W/m∙K. Since then, we have developed a 3.5 W/m∙K rigid epoxy with high thermal stability.
We have completed a fair bit of work to validate and confirm Nategh’s results. We also wanted to be sure cooling effects extended to different types of motors.
Frankly, I was surprised by what we found. Nategh had used a liquid jacketed motor, and he saw about 50° C lower temperature. I assumed that when we tested off-the-shelf air-cooled motors, we’d see maybe 15° C lower temperatures. What we actually found was 35° C lower temperatures in motors impregnated with our materials, with no other special attempts at cooling. Our customers who are using liquid jackets are still seeing improvements approaching 50° C, which is great.
Charged: Could you explain how the validation tests were performed? What were the results?
Barber: The tests that Advanced MotorTech performed were using 3 hp off-the-shelf motors. Some motors were impregnated with our 3.2 W/m∙K silicone, and others used the 3.5 W/m∙K epoxy.
Then, the folks at Advanced MotorTech chose two other epoxies made by different companies for comparison. The ones they chose are known as workhorses in the industry because a lot of manufacturers use them to protect motors from corrosive chemicals or moisture. Usually in these cases, it’s seen as an added benefit that when you replace air gaps in the motor with epoxy, it reduces operating temperatures as well. In other words, improving thermal conductivity has not typically been the main reason people used these materials. The data sheets for these epoxies advertised a thermal conductivity of 1.4 W/m∙K for one material and 4 W/m∙K for the other. However, the effective thermal conductivity of the 4 W material in both lab tests and motor performance tests was about 1.6 W/m∙K. One explanation for the large difference in advertised versus effective thermal conductivity could be that the material didn’t fully impregnate throughout the motor because it was too thick. This is a common issue for highly-filled epoxies that we have worked hard to improve in our high thermal conductivity epoxy.
The test results showed that when the 3 hp motors were operated to 175% of their rated horsepower, the end winding temperature of the unpotted control motor was about 140° C. Those potted with our competitors’ epoxies were about 120° C, and our materials reduced the temperature to about 105° C. We have published all of that data in a webinar and a white paper, entitled How Proper Application of Thermally Conductive Materials Will Improve Motor Power Density.
The temperature readings were taken at the end windings with 6 thermocouples at each end of the motor. So reported temperatures are an average of the temperatures at each end of the motor. In general, the end windings are considered to be a problem hot spot, and if you can get the heat away from the windings, you can reduce the overall temperature as well.
The team at Advanced MotorTech also did some simulations and thermal models that predicted the rotor itself would operate about 9° or 10° C cooler because it was next to a cooler stator. It would be very hard to measure the actual rotor temperature, but it’s safe to assume that if you can open up the heat flow away from the bottleneck in the end windings, then you can remove more heat from the motor in general.
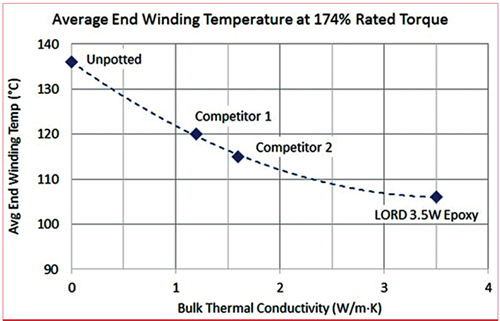
Performance test results of a 3 hp commercial industrial motor with varnish only (unpotted) or potted with two competitor epoxy materials and a LORD high thermal conductivity 3.5 W/m·K epoxy, operated at 174% of the rated motor torque. Note that Competitor 2 had an advertised bulk thermal conductivity of 4 W/m·K.
Charged: Did you use the same motor-epoxy setups for the accelerated aging test as well? What did you learn from those tests?
Barber: Yes, we took those exact same motors to Advanced Energy for accelerated aging tests. We wanted to beat them to death to see whether the materials could survive both the high temperatures and constant temperature cycling.
Our goal was to cause the motors to fail in a relatively short amount of time, so they were pushed far beyond their thermal limit. The motors tested were Class F, which means they have a 155° C maximum, and we were operating them above 200° C.
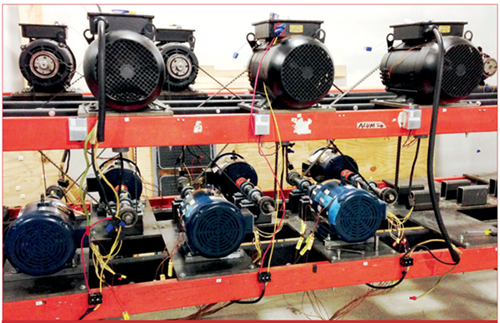
Accelerated aging test set-up showing test motors on the bottom rack and load motors on the top.
The test protocol had over 400 starts per hour with very high torque, low speed, and short cycle durations, so the in-rush current would heat the motors to their equilibrium temperatures, which varied depending on whether or not they were potted, and with what material. Motors were operated for about 6 to 8 hours per day, and then we would let them cool down to room temperature overnight. We repeated the cycle for about 25 days, which gave us additional information on thermal cycling stability. The test was run without any attempt to actively cool the motors externally, just natural convection.
At the highest temperatures, the unpotted motors were running at about 260° C. The motors that were potted with our competitors’ epoxies were running about 20° C cooler than that, and the motor that was potted with our epoxy was running 40 to 45° C cooler.
All of the motors that we ran in the accelerated aging test eventually failed. The tests with two of our competitor’s epoxy failed first, at different times, and the motors with our materials eventually failed as well.
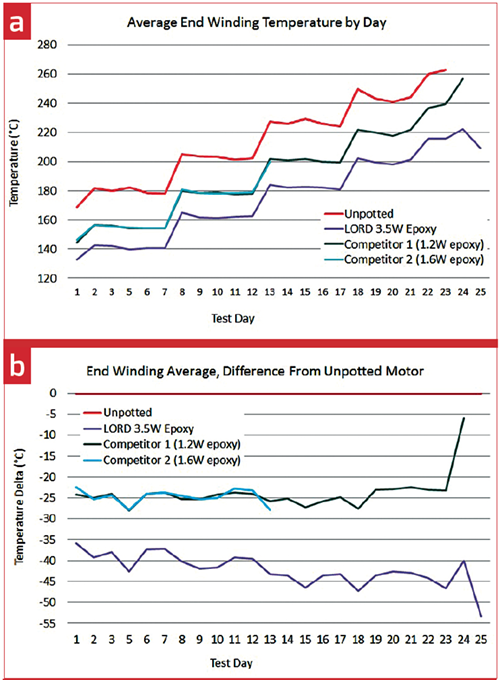
Average motor end winding temperature (a) and temperature difference from unpotted motor (b) for epoxy-potted motors during the 25-day life test. Note that Competitor 2 motor failed due to lead wire short and seized rotor and bearing on Day 13.
Charged: What were the failure mechanisms at the end of the accelerated testing?
Barber: There were a few different failure modes. The motors that we were testing had a varnish applied to them, and we impregnated the epoxies on top of the varnish. Most motors have some kind of varnish applied to the windings, particularly motors that aren’t potted, because something needs to protect the wires and keep them from moving and chafing during vibration. One of the key failure modes that we saw was that the varnish under the potting materials was liquefying. In some cases, it would liquefy while running during the day then solidify overnight in the motor’s air gap. So it would jam up and cause the motor to seize and not run anymore.
We also had a couple of motors with electrical shorts, which were most likely due to the overheating of wire insulation at a certain location.
The most interesting finding for us was that one competitor’s epoxy lasted longer than the other. However, even though it lasted longer in the test, there were about six to eight stress cracks throughout the epoxy when we opened the motor up afterward. Our materials had no stress cracks at all.
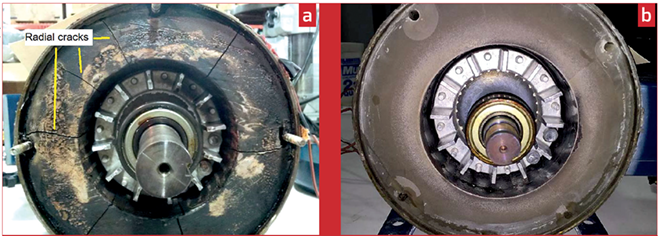
Post-test views of motors potted with (a) competitor 1.2 W/m·K epoxy, showing multiple radial stress cracks, and (b) LORD 3.5 W/m·K epoxy, showing no cracking of epoxy after test.
Charged: Why exactly do you think LORD Corporation’s materials performed so much better in both tests?
Barber: Our materials have a few different properties that make them ideal for this application.
High thermal conductivity and low viscosity are the two properties that make them so effective at reducing hot spots in the motors. It’s very important to have both for this application. Our 3.5 W/m∙K conductivity material, for example, has about one third the viscosity of materials from our competitors with comparable conductivity, which means that our material flows and levels like cake batter rather than like paste. When the material is too thick, it makes it really difficult to impregnate all the fine areas that you need to reach when potting a motor.
Another important property is a high glass transition temperature (Tg), which is the reason there were no stress cracks in our material after the accelerated aging tests. Tg is the temperature where materials go from being more rigid to more elastic, so it gets a little bit softer. At that point, the thermal expansion coefficient also changes pretty dramatically.
The thermal expansion of copper and steel is in the 10 to 15 ppm/degree C range. Ideally, you want a potting material that does not create any mechanical stress. Silicones accomplish this by being so soft that they can deform without causing any issues. If you use a more rigid epoxy, you need to have it match the thermal expansion of the material around it to minimize the mechanical stress.
When you exceed a material’s Tg, the expansion coefficient can increase by about five- or six-fold. You may have an epoxy with a 20 ppm/degree C expansion below the Tg and about 100 or 120 ppm/degree C above the Tg. As you’re cycling back and forth across that temperature, you’re constantly changing the thermal expansion of your material – pushing and pulling in every direction. We think that’s the reason for the stress cracks.
So, we design our motor potting materials to have not only a high thermal conductivity and low viscosity but also a high Tg. Our 3.5 W/m∙K epoxy has a Tg over 200° C, so it should be good for at least a Class H motor. It also has a very low expansion coefficient of 12 ppm/degree C. That’s comparable to the steel and copper, so you don’t get a loss of adhesion or additional mechanical stress.
Charged: How are you able to design a material with such great properties, while your competitors appear to fall short?
Barber: That’s the magic of the formulation, which is a trade secret. Getting those materials to be as low-viscosity as possible but also high-conductivity has been the chief goal of our chemical research group over the past few years. We’ve achieved it in our silicone materials, and now we’re extending it into our epoxy materials as well.
Charged: You mentioned that you’re working with some customers on impregnating motors. What applications do you think are best suited for potted motors? Are any customers close to using your material in production?
Barber: We’ve been actively pursuing applications where you need a really high power density, because removing more heat allows you to make the motor smaller and lighter. Based on theoretical calculations that we have done on industrial motors, you can get about a 15 to 25% percent decrease in the weight of the motor for a given horsepower by using our material.
We’ve also done tests with a few customers, and depending upon the configuration, we’ve seen improvements in maximum power output between 20 and 30% at the same peak temperature. Getting in on the design phase of the motor can really help because the motor can be designed to maximize ease of potting and take full advantage of the high thermal conductivity of the potting material.
Motors are limited by their maximum temperature range, mainly because the insulation material that keeps the wires from shorting has a temperature limit. There is also an efficiency loss as you get hotter because the resistance of copper increases.
We also have customers that want to reduce operating temperatures to extend a motor’s lifespan as much as possible. We’re actually starting production of our 3.5 W/m∙K epoxy for a customer who is going to use it in a marine application. They are very concerned about the product’s lifetime because it’s going in an inaccessible location, and they essentially need the motor to last forever. It’s a liquid-cooled motor, and it was getting up to about 135° C. By potting with our new material, they were able to drop the temperature by 40° C. So they were thrilled, and we’re going into production by the end of October.
Charged: What about EVs? Do you think automakers will be impregnating motors someday in the near future?
Barber: We’re already heavily into the EV industry with products on the power electronics side, so we’ve been talking to a lot of our current customers about the potential to make motors lighter weight with a smaller footprint and still high power.
There are a variety of new things that these companies are looking at to improve motors in the future, and we think this will be seen as an additional option.
There are a couple of ways to get more power or more efficiency out of your motor. Most of the time that involves making the motor bigger, or adding more copper and steel. Our material has about the density of aluminum, which is half the density of steel and copper. So, you can take the same motor and make it act like it’s 25% bigger.
Everything in the automotive industry is driven by cost, so our solution has to be the most economical way to reliably reduce temperatures. We need to validate in every customer’s design that the added cost of using our material in a potting process is economical for them. If they can solve it with a different method, then that’s what they’re going to do.
We have potted some EV motors just to prove to customers that there is a real benefit. We’re hoping to bring some of those projects to a resolution in the next few months. The testing has been going on for quite some time, and we’ve had at least one automotive customer that sees a lot of promise with our solution on the financial side. We’re hoping that will keep moving forward.
We’re also working with a number of different motor manufacturers, most of whom build products for both EVs and industrial applications. In most cases, we are trying to validate in their industrial versions first.
Charged: How long before we could potentially see the technology in production EVs? Will it take 6 to 8 years – the typical design cycle for cars?
Barber: It really depends on the customer. If you’re solving a big problem for them, then they’re very motivated to get your material into their application as soon as possible.
There is also a lot more to EVs than just consumer automobiles with shorter development cycles. Before it gets into mainstream automotive, it will probably be 3-5 years, but there are a lot of other applications that we could hit a little sooner than that. We’re still quite early in the development stages.
The first commercialization for our new material with 3.5 W/m∙K conductivity is the marine application, but it’s not a drive motor. That customer has already started purchasing the material, and we’re in scale-up mode, moving towards production.
This article originally appeared in Charged Issue 27 – September/October 2016. – Subscribe now.