As EV-makers continue to upgrade from 400 V to 800 V systems, parts suppliers have been hustling to keep up with the new specs.
Knowles Precision Devices, for example, specializes in high-voltage capacitors—it’s a market leader in multi-layer ceramic capacitors rated from about 200 V up to 12,000 V. Looking back just 10 or 15 years, there wasn’t much of a need for these products in the automotive market. Most vehicle electrical systems were all based on 12 volts, and used capacitors rated for 30 V or 50 V test requirements. But EVs are changing things quickly, and automotive needs have started moving to higher and higher voltages.
Let’s take safety caps for an example. The testing requirements for 800 V systems specify that the ceramic capacitors in the circuits are expected to survive up to 4,000 V. This is having a big impact on the parts supplier market, because many traditional automotive players—who were used to 50 V test requirements—do not have historical expertise in high voltage. So, business has begun to swing over to new entrants in the auto industry.
800 V systems specify that the ceramic capacitors in the circuits are expected to survive up to 4,000 V.
Knowles recently launched a new line of automotive-grade certified safety capacitors. Charged chatted with Applications Engineers James Brewster and Steve Hopwood to learn more about the company’s new EV product line.
Charged: What exactly is a safety cap?
Hopwood: The term safety caps is a relatively standard term for capacitors that meet a set of international safety certification standards. They’re actually rated around 250 V AC, and originally intended for applications where you’re going to see mains voltage. They’re mandatory when you’ve got applications that are connected directly to the mains, where a person could be at risk in the case of a failure. That means there are very strict requirements. When you’re dealing with a charging unit, an on-board charger, you are inevitably connecting to the mains to charge the battery.
And because of safety caps’ characteristics and ratings, they’re of interest to the battery management sector. If you’re directly on a battery rail, or if you’re in some way associated with a battery, you need to make sure that you don’t end up with failures on the battery lines.
There are various international standards that are applicable to safety caps, and automotive engineers are generally looking to the ordinary electrical international standards. For these types of safety-rated capacitors, they’re looking at IEC/EN 60384-14+A1 and UL 60384-14.
Charged: What makes high-voltage capacitors fundamentally different than the lower-voltage products?
Hopwood: There are a few things. The materials you use at a low voltage may not always be the same materials you need to use at higher voltages. They’ll need to have specific requirements in terms of things like voltage withstand, breakdown voltages, and so on. That’s expressed in terms of volts per micron. So, we’re talking about very thin dielectric layers between the electrodes. But you’ve also got the mechanical design of the part, where you have to understand a different methodology for how you create the electrode layers, how you design them, how you drop voltage across multiple layers, mounting capacities in series within a single unit.
Then there are specific designs relating to the interaction between the electrode and the outside layers of the capacitor to prevent flashover and arcing from occurring. It’s just a different way of thinking. If you’re dealing with a 50 V part, typically it will be a very small capacitor. If you’re dealing with something that’s 3,000 or 4,000 V, physically you’ve got to make the part a lot bigger, and you need to start thinking much more about your creepage and clearance distances. Your mechanical design comes into it a lot more.
We’re used to dealing with high-rail, high-voltage parts. Traditionally, our markets were aerospace, military, those sorts of applications, where failure isn’t an option.
In terms of the R&D we’re doing, we’re constantly looking at new materials, new designs. We’ve got a couple of patents that we apply to our products, which relate to internal structures, construction and the way we actually put the ceramic in there. I can’t go into detail on those, but they’re all aimed at getting higher voltages, better withstand, more reliability and more capacitance per unit volume. So, one of the things we’re doing a lot of work on is the range—how much capacitance we can get into a part for a given size and voltage rating.
All R&D for the automotive line is done out of Norwich in the UK. We’re actually next door to the Lotus factory. The manufacturing is all in Suzhou, China. We’re IATF 12649 certified, and everything we do for automotive is AEC-Q200 certified.
Our automotive customers are very interested in reliability…like voltage-withstand tests—can you hit the electronic circuit with two and a half times the voltage rate?
Charged: Are you seeing a lot of special requirements and requests from the automotive industry?
Hopwood: Yes. Our automotive customers are very interested in reliability, for example. Like voltage-withstand tests—can you hit the electronic circuit with two and a half times the voltage rate?
So, 400 V battery systems, which most of the world is using now, are looking for 2 kV dielectric withstanding voltage (DWV). The move to 800 V battery systems is doubling that. Some manufacturers are going to a 3 kV withstand rating, some manufacturers are going to a 4 kV DWV rating. The idea is, if it can safely take 4,000 V for a short duration, it will work at 800 V reliably without any risk of a short circuit.
That test puts a huge stress on the components. For instance, if you take a normal 800 V ceramic capacitor, its breakdown is probably going to be somewhere around 1,500 V. So, this is much more stringent. It’s a much higher specification that’s needed.
We’re seeing more and more manufacturers that say they’re not going to do any more 400 V battery systems, so it’s big news to us, this move to 800 V. It makes life very demanding on parts.
Brewster:To cover that, we’ve got a hundred-percent test— the components are fully tested to 4,000 V just to ensure that they’re definitely going to withstand that level.
Our new product line SYX is our biggest in what we call our Enhanced Safety Range. There are one to five case sizes, and each case size has two types of dielectric: one for low-loss applications, and one for high-capacitance applications. These are both being externally approved by TÜV and UL, the external certification bodies who independently certify these parts for safety.
In addition, this range has got the 4 kV DWV testing that Steve is talking about. It also has humidity robustness grade three, which means it’s suitable to be used in high-humidity environments. And it’s got a supplementary 1 kV DC rating on it. These are ratings which kind of put us ahead. We’re, as far as we know, the only company who offers all of these ratings on a single range of parts. It’s also, obviously, AEC-Q200 certified. I would say this is our most automotive-focused range here. It will come out of our IATF-certified factory, so we’ll cover everything that the auto industry needs.
In addition to that, we’ve got the SYS, which is the same as the SYX, however it’s a shorter part, which means it doesn’t meet the creepage requirements for full 60384 qualification, so this range of parts is only approved for machinery within the scope of IEC 62368, which is mostly telecommunications equipment.
We also have the S3X range, which is our highest-capacitance ceramic capacitor family. That has a lower rating, X2, which means it only needs to withstand 2,500 V impulse, as opposed to 5,000 V. And it has a lower DWV rating of 3,000 V. This means that we can get to a higher capacitance of up to 56 nanofarads, which again, for this high-voltage sort of application is top of the range for us and all other competitors.
Hopwood: The 56 nanofarad is a class X, so that’s using line-to-line. They’re not usually looking for such a high test voltage there, which is why it’s got a slightly lower rating, and therefore a slightly higher capacitance. 305 Vac is looking at three-phase systems. Again, that’s something that we’re going to be market-leading on. There is no one else at the moment with a ceramic multilayer capacitor doing a 305 V AC rating with safety approval.
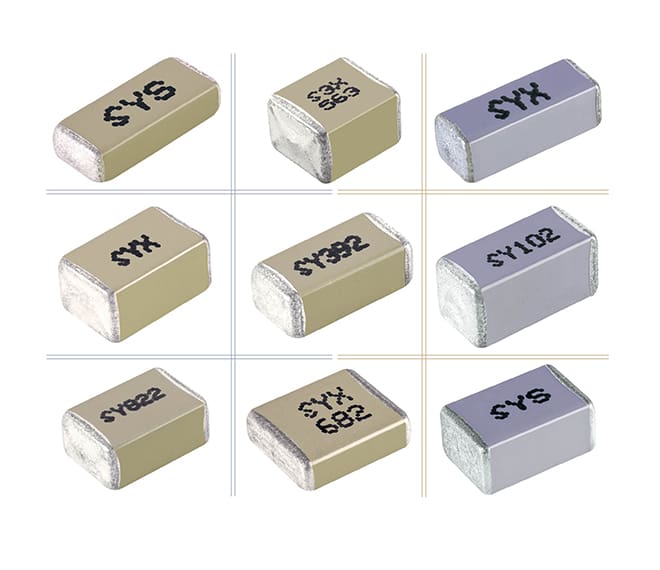
Charged: When you’re working in automotive, are there other major considerations, like assembly time, manufacturability, etc.?
Hopwood:Yes. A lot of safety-rated capacitors are through-hole, radial-mount. Those are for circuit boards where leads go through holes and are soldered on the backside of the board. Through-hole is still widely used for high-voltage systems because the boards’ epoxy coating insulates the components. But they’re relatively expensive to put through boards. You need to have different soldering techniques, and you have to align the leads to go through the hole, which isn’t always as easy. Our parts are surface-mount, so they’re very quickly, easily and inexpensively placed on boards.
When capacitors went from being through-hole to surface-mount, safety-rated ones lagged behind, because you had to have the coating material on there to make them pass the high-voltage tests. It was only when the world developed the ability to manage the high-voltage requirements in surface-mount packages that they were able to go over to surface-mount, and that was something we were at the forefront of.
And that’s the same thing with the board height—a leaded part will traditionally sit up off the board, whereas the surface-mount is much lower down, which adds more challenges.
Charged: Do you see a lot of companies in the auto industry struggling with high-voltage designs and parts selection, because it’s so new to them? Are there common mistakes you find engineers making?
Hopwood: Most people we see who are choosing high-voltage safety caps generally know what they’re doing. What they sometimes get wrong are things like creepage clearance distances, where they don’t allow for the voltage. We have application notes that assist with board designs.
What they sometimes get wrong are things like creepage clearance distances…some struggle to work with high voltages on circuit boards for the first time.
Some struggle to work with high voltages on circuit boards for the first time. There are things you’ve got to do—for instance, making sure you don’t get solder balls trapped underneath the chip when you put it on the board, which can suddenly cause arc-over situations.
When you’re not used to high-voltage systems, now you don’t know what to think about. Some seem to struggle to get their head around the voltages they’re talking about. And even though they’re asking us for a part that must withstand 4,000 V, we see designs where the conductors aren’t physically far enough apart. So, we help with that. We’re used to discussing the application as well—the layouts, mounting methods, etc.—things beyond what’s on the data sheet.
This article appeared in Charged Issue 54 – March/April 2021 – Subscribe now.