When you’re writing about the dawn of a new industry, “firsts” and “milestones” come along so often that they may start to lose their novelty. However, the BMW i3, which was officially “launched” in July, and is scheduled to go on sale next year, boasts an impressive number of innovations that has the EV press humming like an overloaded transformer.
The i3 is the first EV to offer a range-extending gas engine as an option, and it’s the first vehicle of any kind to make such extensive use of carbon fiber reinforced plastic (CFRP). In addition to its technological innovations, the i3 represents a milestone for the market. It’s the first production EV from any of the upscale German brands, and only the second European EV to go on sale in the US (the first was the smart electric drive).
While Europe would seem to be a perfect market for EVs, in fact American and Japanese automakers have been leading the way. Renault, which has a partnership with Nissan, is doing relatively well with its four electric models, but it’s the German automakers who set the tone in the European market, and the i3 gives that tone an electric edge. If BMW starts moving some electrons, VW and the other Continental carmakers are bound to turn up the voltage too.
That brings us to what we in the plug-in press think of as The Big Question: will the i3 be just another public relations project, or is BMW serious about selling it in substantial volume? At this point, the tea leaves look positive. BMW has created a separate sub-brand, i, just for electric vehicles, and it has said that the i3 will be available at about 300 of its 338 US dealers.
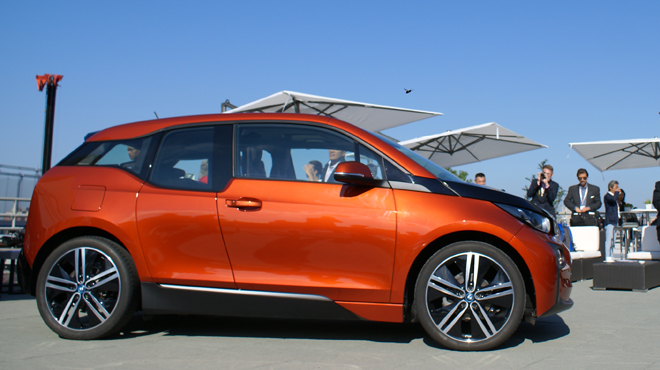
At the i3’s launch party in New York, Charged spoke with Jose Guerrero, the i3’s Product Manager, and Jacob Harb, BMW’s North American Head of EV Operations. They declined to make any specific sales projections, but said that production capacity will be “in the thousands.” BMW will start taking reservations at the end of the year, and plans to start deliveries in spring 2014.
The company has a reputation for introducing new models slowly and deliberately, and this certainly seems to be the case with its electrification efforts, which have proceeded in three phases. In 2009, BMW began field tests of the Mini E, a conversion of the Mini Cooper. In January 2012, it launched a trial of the ActiveE, which was based on the BMW 1 Series sedan, leasing 1,100 vehicles to “electronauts” for a three-year period.
The company has applied what it has learned in both of these programs to the i3, which Jacob Harb describes as the company’s breakthrough EV. “We crawled with the Mini E, we walked with the ActiveE and we’ll run with the i,” he said. “We learn every day. The electronauts have now driven over 12.5 million miles worldwide, and they are incredibly vocal.”
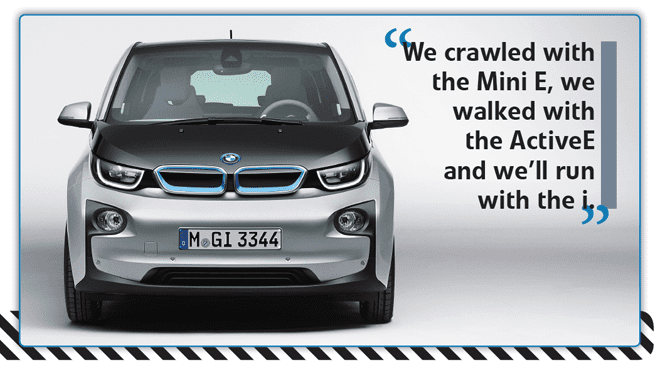
Because the i3 was designed as an EV from the beginning, BMW’s engineers were able to make it extremely light – 2,700 lbs, versus 4,000 for the ActiveE. This allowed them to drop the battery size to 22 kWh (compared to the ActiveE’s 32 kWh battery) while offering the same range (around 80-100 miles). This not only saves on weight and cost, but also charging time. The i3 has the same onboard charger as the ActiveE, but can charge in three hours, as opposed to four or five.
In a previous iteration, the i3 was called the Megacity, which gives a clue to its intended habitat. It’s compact, with a shape that allows it to squeeze into urban parking spots but maximizes interior space. It also features a 32-foot turning radius, which “sounds like a number until you try it,” as Jose Guerrero relates. “When you do a U-turn, you see how it’s really supposed to be used in a city environment. We were able to do that because of the rear-wheel drive. You don’t have all these components in the front, so the steering is aggressive, and you can whip this car around quickly.”
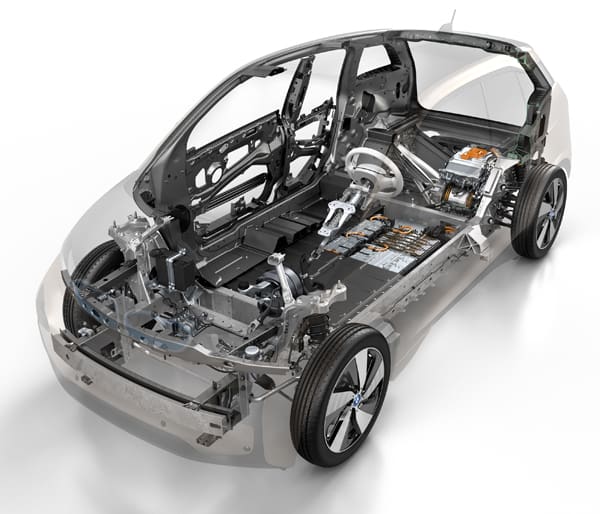
BMW designed the i3 “from the ground up” to be an EV, and developed most of the components, including the motor, power electronics and battery, either in-house or in cooperation with joint venture partners. Every part has been designed to save energy and weight, in order to maximize range. Energy-saving LED lights are used throughout. An optional heat pump uses up to 30% less energy than conventional electric heating.
The i3’s lithium-ion battery consists of eight modules, each with 12 individual cells, and produces 360 V and 22 kWh of energy. It’s possible to replace individual modules in the event of a fault. The battery pack sits at the bottom of the chassis, which improves handling and frees up interior space. The AC coolant also cools the battery, and can be warmed using a heat exchanger, keeping the battery at its optimum operating temperature of around 20° C. Both the battery and passenger compartment can be preconditioned before a journey begins, while still connected to the grid.
REx
The optional range extender is a 650 cc two-cylinder gas engine that is mounted next to the electric motor above the rear axle. The 25 kW/34 hp engine increases the car’s maximum range to around 180 miles. This is an interesting turnabout – while Toyota and Ford offer hybrid models with the option to plug in, BMW offers a pure EV with the option to add a bottle of dinosaur juice as a sort of security blanket, or what Jacob Harb calls “training wheels for the consumer that’s on the fence.” How many consumers will feel they need the training wheels is unknown, but BMW’s production line is flexible enough to build i3s with or without the range extender, according to demand.
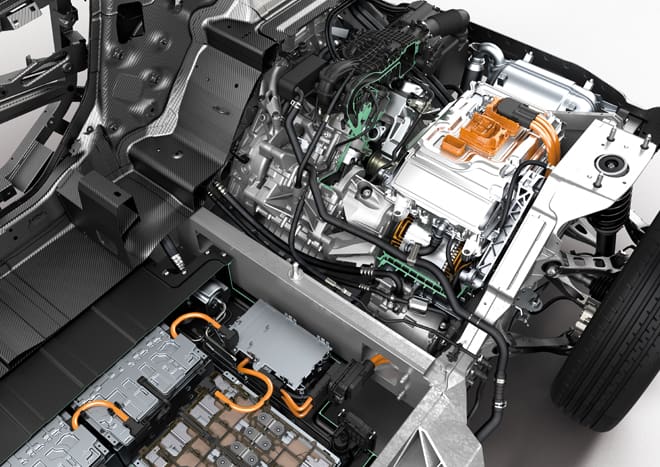
The range extender has no effect on luggage capacity (the nine-liter fuel tank is located in the front section of the car) and BMW spokesmen assured us that it doesn’t hurt the car’s performance. Apparently that little motor can produce enough energy to maintain the same acceleration and top speed while in range-extended mode. However, the addition of the extra weight does reduce the specs a bit, adding another seven tenths to the i3’s 0-62 mph time, and dropping electric range by 10%.
Jose Guerrero explained why BMW chose to offer the range extender instead of a larger battery. “Ninety percent of Americans drive less than 30-35 miles a day. We know that from our Mini E studies. Why do people want bigger batteries? Because of range anxiety. What happens when we add more batteries? More weight, more cost.” The range extender and a full gas tank add a mere 450 lbs and $3,850 to the equation. DC fast charging, which can deliver an 80% charge in 20 minutes, is another treatment for range anxiety, and Guerrero expects it to be a more popular option than the range extender. A majority of the electronauts that tested the ActiveE said they would rather have DC fast charging.
LifeDrive
The i3 uses a new architecture called LifeDrive, which is similar in principle to a body-on-frame design. The car consists of two horizontally separate modules: the aluminum Drive module (aka the chassis) incorporates the battery and drive system, while the Life module (aka the passenger compartment) is made of carbon fiber reinforced plastic (CFRP). This high-tech material is a big part of the i’s lightweight design strategy. CFRP components are around 50% lighter than steel components with comparable properties. According to BMW, CFRP is the lightest material that can be used in the construction of car bodies without compromising on safety. The low weight and high rigidity of CFRP allowed the i3’s designers to dispense with B-pillars, so they used opposing “coach” doors in order to give easier access to the two rows of seats. The i requires no central tunnel, which opens up even more interior space.
CFRP has other benefits. It saves time and costs on the production line, and it can be repaired more quickly than metal. As Jacob Harb explains, “you don’t rebend anything; you just replace a module.”
Of course, the main point of CFRP is to save weight. Designing any EV involves tradeoffs among battery capacity, weight and range. Range can be extended by increasing battery size, but that adds weight and harms performance. Similarly, a more powerful motor and power electronics require more energy, which again means heavier batteries or restricted range. A lightweight body, on the other hand, enhances performance, and the weight savings can be “invested” in larger batteries which, in turn, boost the car’s range.
Thanks to the aggressive weight-saving measures, the i3 is no heavier than a comparable ICE vehicle with a full fuel tank. The motor weighs just 50 kg, and the battery 230 kg. The lightweighting imperative extends to such components as the door trim panels (10% lighter than conventional equivalents), aluminum screws and bolts, and even the windshield wiper blades, which use a honeycomb structure to save weight.
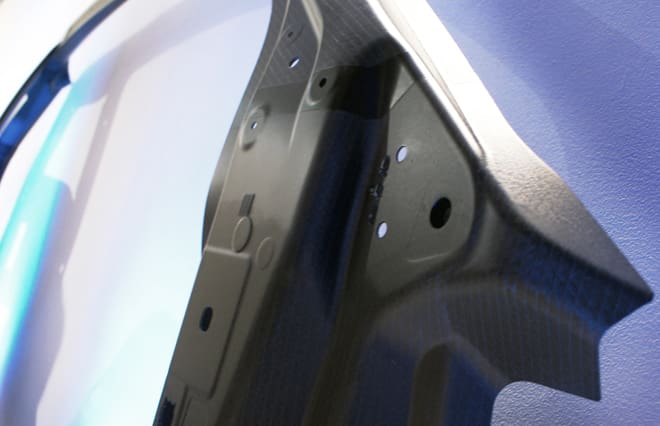
Engineering Notes: Carbon Fiber Reinforced Plastic
The carbon fiber raw material for the BMW i3 is produced at a plant in Moses Lake in Washington state, which is operated by the BMW Group and its joint venture partner, the SGL Group. In a complex multi-stage process, the constituent elements of the fiber are removed by gasification, leaving a virtually pure carbon fiber just seven microns thick. About 50,000 of these individual filaments are bundled into so-called rovings or heavy tows, and wound on reels, which are sent to the plant in Wackersdorf, Germany, for processing into lightweight carbon fiber laminates.
At the CFRP press shops in Landshut and Leipzig – where BMW is already producing other CFRP parts, such as the roofs for the M3 and M6 – the carbon fiber laminates are processed into body parts. At the initial “preforming” stage, the pre-cut carbon fiber laminate begins to acquire a shape. During this process a heat source is used to give a fabric stack a stable, three-dimensional form. Several of these preformed stacks can then be joined to form a larger component. In this way, CFRP can be used to produce components with a large surface area that would be difficult to manufacture from aluminum or sheet steel.
Preforming and preform joining are followed by a high-pressure resin injection process called resin transfer molding. As the fibers and the resin bond, the material acquires the rigidity that is the key to its special qualities.
Until now, CFRP body compartments have been manufactured only for special vehicles such as racers and extravagant individual sports cars. Production costs are of minor importance for these small quantities. The curing time for the adhesive bonds can be more than one day. To minimize this time for mass production of the i3, BMW has greatly accelerated this curing process.
A newly developed adhesive can now be processed for only 90 seconds before developing adhesion following application to a component. Half an hour later it is hard, a tenfold acceleration of the traditional bonding process. In order to further reduce the curing time to a few minutes, BMW has developed an additional thermal process that involves additional heating of specific adhesion points to further accelerate the curing process by a factor of 32.
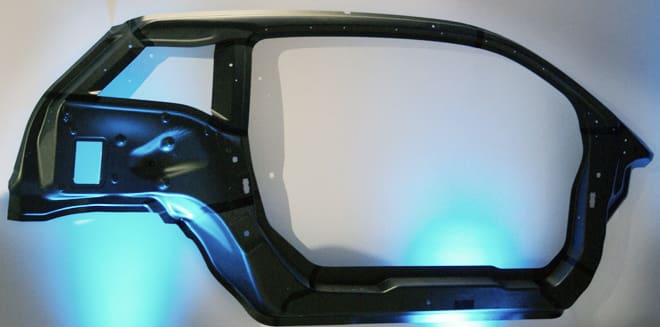
The new CFRP press shop has little in common with a conventional sheet-steel press facility – it boasts a leaner production structure which is reflected in lower costs. For example, costs are significantly reduced by the fact that a conventional paint shop and cataphoretic immersion priming are not required. The new production process brings enormous time savings, and makes it feasible to mass-produce large CFRP components, with newly formed parts leaving the press in less than 10 minutes.
Even complex assemblies like the entire side frame for the i3’s Life module leave the facility with many structural elements already integrated.
BMW is already using some CFRP parts in select models, and representatives indicated that it’s possible the leaner processes could lead to wider use in many more vehicles. However, the use of CFRP in electric vehicles is particularly cost-effective, because the reduction in weight can be offset by a reduction in the size of the battery pack, which is also expensive.
Regeneration
The i3 features what BMW calls a single-pedal control concept. The moment the driver eases off on the accelerator, the electric motor switches from drive to generator mode, and produces a precisely controllable braking effect. The regeneration is speed-sensitive, which means the car “coasts” with maximum efficiency at high speeds and generates a strong braking effect at low speeds. According to BMW, this creates a very direct interaction between driver and car, and an attentive driver can carry out 75 percent of braking maneuvers without touching the brake pedal. “Once you spend an hour in the car, it becomes a game,” says Jacob Harb. “Can I get away without using the brake at all?” The friction brakes are activated only when the driver really stomps on the pedal. The system is even smart enough to illuminate the brake lights when the amount of regeneration crosses a certain threshold.
Connectivity
Naturally, the i3 includes the latest and greatest connectivity and driving assistance features. An integrated SIM card and extensive smartphone integration via USB and Bluetooth allow drivers to share information with their car at any time. The i3 is in constant wireless contact with BMW’s servers, transmitting data about the battery and other electrical systems, and receiving up-to-the-moment navigation data.
The navigation system has a dynamic range display that considers several factors and gives drivers a continually updated range estimate. If the destination programmed into the navigation system is beyond the car’s range, the Range Assistant will suggest switching to the energy-saving Eco Pro or Eco Pro+ mode, and calculate a more efficient route. The AC and heating, which also condition the battery pack, can be activated remotely. The Driving Assistant Plus option includes Active Cruise Control and Collision Warning with braking function. The Parking Assistant option enables fully automatic parallel parking.
Sustainability
BMW has gone to great lengths to insure that the i3’s materials, production process, supply chain and recycling all adhere to sustainable principles. The production of the BMW i3 consumes around 50 percent less energy and 70 percent less water compared to other BMW models. The carbon fiber plant in Moses Lake is run entirely on hydroelectric power, and the Leipzig assembly plant is powered by on-site wind turbines. Taking all this into consideration, BMW says the i3’s carbon footprint is around a third smaller than that of the BMW 118d, which was named World Green Car of the Year in 2008.
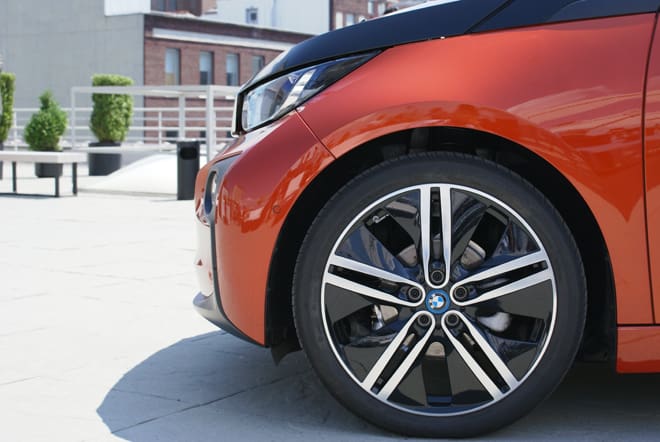
Charging
BMW will offer “white glove” installation of its Wallbox home charger, and installation costs can be rolled into the financing. In public, the ChargeNow card enables universal access to charging poles and provides a cashless means of payment. It allows customers to use charging stations operated by different providers with a single card and receive a single standardized invoice from BMW i. BMW is one of the partners in the Hubject joint venture, which is working to create a true roaming capability for EVs throughout Europe.
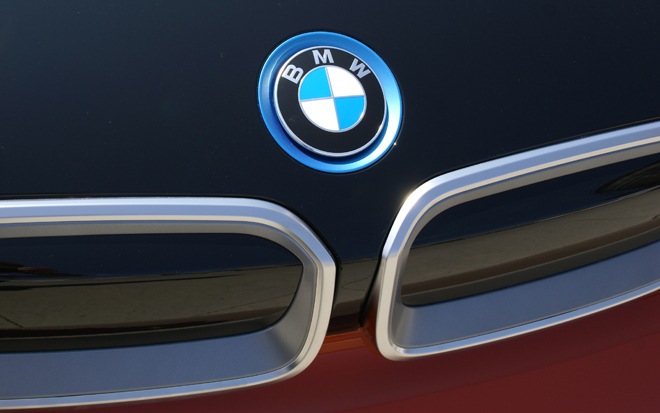
Shaking up the market
A couple of pundits have pontificated that competition from the i3 spells trouble for established EV sellers Nissan, GM and Tesla. BMW’s new offering is definitely going to stir things up, and give each of those three a kick in the pants, but it feels more like a model that fills a gap in the market, rather than one that directly competes with existing models.
Tesla’s Model S is a luxury sedan with a price tag way north of the i3’s, so there’s no head-to-head match-up there. However, BMW has another ace up its sleeve, the i8, a futuristic, performance-oriented PHEV that just might give Model S a run for its money. It’s scheduled to debut at the Frankfurt Auto Show in September, and arrive in showrooms in early 2014, around the same time as the i3. However, it’s planned as a low-volume car, with a much higher price point than the i3.
The LEAF and the i3 have roughly similar form factors (actually the i3 is a bit smaller, and seats only four), and few would dispute that the i3 is a snazzier ride. You’d expect a BMW to have a higher price tag than a Nissan, and you’d be right – the LEAF has an MSRP of $28,800 to $34,840 depending on the model, and that’s far enough below the i3’s $42,275 to make it unlikely that the i3 will be poaching very many of the LEAF’s customers.
The same logic applies to the Chevrolet Volt. The 2014 Volt has an MSRP of $34,995, whereas the i3 with the REx option carries a starting price of $45,200. Besides, the two cars look and feel very different, and they’re just not being marketed to the same type of buyers. The i3 is an electric city car, and a Volt is for people who want an EV, but need to have the capability to take long trips, something that the i3, even with the REx, is not designed to do.
All of this is excellent news for consumers. Different car buyers have very different sets of needs and wants, and EVs are really going to take off only when there are enough different models available to fill the various niches. When the i3 goes on sale, that day will be a whole lot closer.
This article originally appeared in Charged Issue 9 – AUG 2013
