The electromobility revolution is gathering speed, but the world’s EV-makers have fallen behind popular tastes in terms of the form factors auto buyers want, and this has emerged as a roadblock to mass adoption. Buyers love SUVs and pickups, and automakers love the high profit margins associated with these models. Electric SUVs are starting to appear at the high end of the market, but so far no one has built a viable electric pickup.
The word on the street is that any automaker that can bring a compelling electric pickup to market will have a hot product on its hands – and just possibly deliver the killer app that will push ICE vehicles over the ridge and down the slope to extinction.
Pickup kings Ford and GM, disruptor Tesla and startups Workhorse, Havelaar and Bollinger all have pickups in the pipeline. However, the company that has really grabbed the attention in this space is Rivian Automotive, which came on the scene in November, 2018 after nine years in stealth mode to present prototypes of a pure electric pickup truck and an SUV, both with specs that rival those of the gas-belching, money-printing trucks currently on the market.
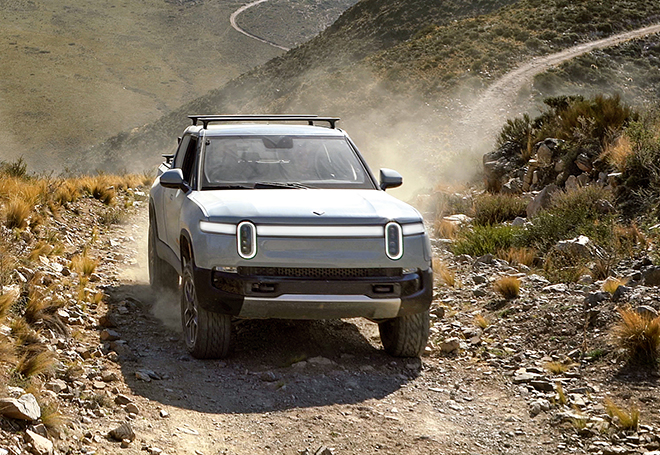
Since that head-turning reveal, Rivian has been garnering substantial amounts of investment, including a recent $1.3-billion funding round which followed a $700-million round led by Amazon and a $500-million round led by Ford.
Ford also plans to partner with the startup to build a new EV. And in September, Amazon changed the game for Rivian by announcing a history-making order of 100,000 electric delivery vans.
Things are so busy at Rivian these days that Charged felt lucky to score an interview with VP of Propulsion Richard Farquhar to learn more about the design and development of the company’s unique electric platform.
Farquhar spent his engineering career working on propulsion systems for high-performance vehicles designed for the road and the racetrack. He spent 15 years as Powertrain Director at McLaren Automotive. From day one he was given the engineer’s dream of designing and developing some of the highest-performance propulsion systems in the world for sports cars, supercars and hypercars – first internal combustion engines, and more recently hybrid and electric.
For the next chapter of his career, Farquhar “desperately wanted to be at the forefront of electric propulsion systems for electric vehicles, which is undeniably penetrating our industry right now.”
So, he joined Rivian as VP of Propulsion to work on high-performance electric propulsion systems for premium electric adventure vehicles. Farquhar now leads all of the engineering teams for the company’s powertrains, batteries, power electronics and thermal systems.
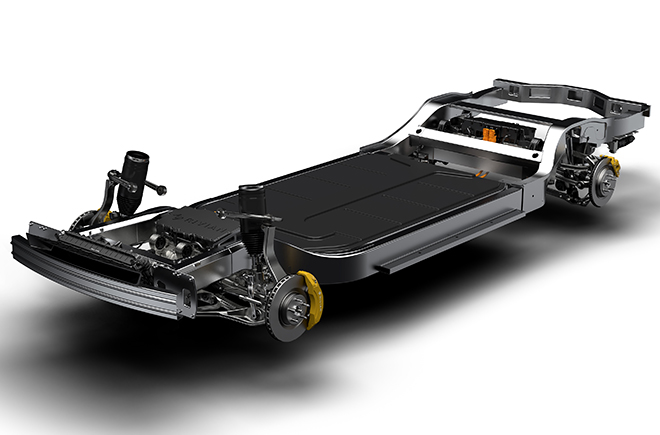
Charged: Rivian calls its electric drivetrain a skateboard platform. What systems are included in that skateboard architecture?
Richard Farquhar: The skateboard is at the heart of all Rivian’s vehicles, and we can build different vehicle types off of that platform. It consists of the energy storage unit – the battery – positioned low and center between the axles for great dynamic control of the vehicle, low center of gravity and great polar moment of inertia. On each axle of the vehicle we have symmetrical electric drive unit assemblies. One driving assembly in the front, one at the rear. Each drive unit assembly has two electric motors – four total – independently connected to the driven wheel with a fixed-ratio single-speed gearbox. We have independent fast-acting, accurate torque control to every contact patch, so dynamically it doesn’t get any better in terms of on-road handling and ride of the vehicle. But also – really important for us – is off-roading. Independent torque control to every contact patch gives the best off-roading capability possible.
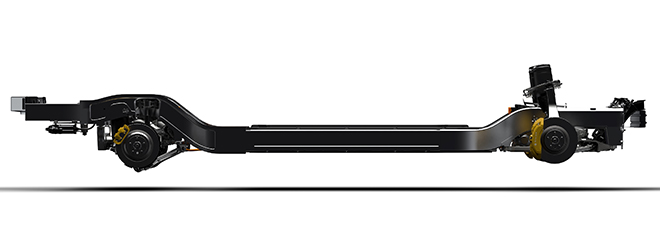
The skateboard also includes the full thermal system. There are three thermal control loops to manage the heat energy in the drive unit assemblies, the battery, and the passenger cabin. To bring the best out of battery electric vehicles, we need excellent thermal control and thermal management, and that’s something we focused on a lot to really maximize performance and efficiency.
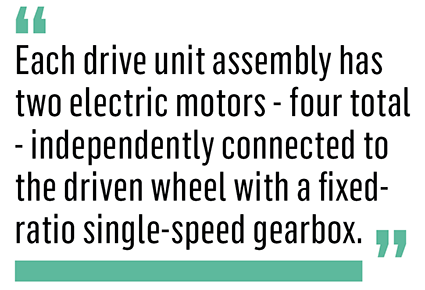
The last element of the skateboard is the chassis systems. We’ve got full ride height control in terms of air suspension, and adaptive roll control on a hydraulic system front to rear, corner to corner. So, in terms of engineering dynamics, it doesn’t get any better to have this degree of control of both propulsion and chassis systems.
Charged: You said that there are symmetrical drive units, so you have four identical sets of motors and drives?
Richard Farquhar: That’s correct – we have four identical motors, left and right, front and rear. Every wheel has the exact same amount of torque and power available to it to maximize performance. We achieve over 14,000 Newton-meters of grounded torque at the wheels combined and 125 miles per hour maximum speed. With the fixed-ratio single-speed gearbox there is no need to change gears, no need for twin speeds. This maximizes efficiency in terms of losses from gear meshing while achieving all of our performance targets.
The inverters are one of the jewels in the crown of this propulsion system, and are fully designed in-house. We designed a dual power inverter device integrated into the drive unit assembly, which allows very efficient control of two electric motors from one inverter assembly. We focused a lot on electrical efficiency from the battery to the inverters to the motors and on to the wheels. Having one dual combined inverter per axle allows us to maximize that electrical efficiency and therefore use the energy to maximize the vehicle’s range.
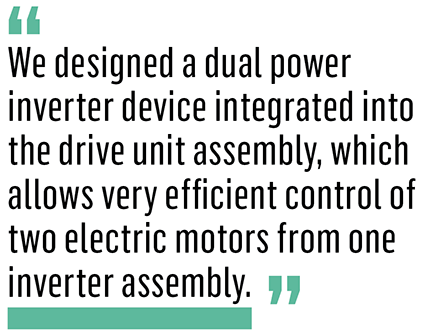
Charged: Was the motor designed in-house as well?
Richard Farquhar: For the e-machines, we work with a partner to design the core electromagnetics and motor assembly, and then package them into our drive unit. It’s similar to battery modules in that we work with partners to source the cells and then design and develop the modules and pack in-house exactly as we want it.
So, the electric motors are unique to Rivian in terms of how they’re integrated into our drive unit assembly, how they’re mounted, how the inverter connects with them, how the cooling connects with them, and how they’re oriented in our gearbox.
Charged: You said that getting maximum EV performance is all about thermal management. Could you elaborate on which areas of performance have thermal issues as the limiting factor?
Richard Farquhar: EV system design is always about trade-offs and optimization, and thermal management always comes right to the top of the list. In terms of the corner cases of EV performance, whether it be DC fast charging, power deployment at a constant rate, or towing and high torque, it comes down to thermal limits in the electric motors, the inverter and the battery.
So, by separating the three cooling systems and having some intelligent valve control within the cooling system, we can look at the consumers of energy – the heat being generated – and maximize the cooling very intelligently so we can achieve the highest performance.
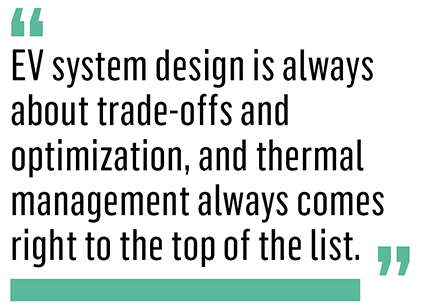
The battery has a dedicated circuit with heating and a chiller so we can intelligently prepare the battery for the optimum temperature for whatever it needs to do. If we’re in a very cold environment, we can heat up the battery temperature to maximize its efficiency and therefore the vehicle’s range.
The same principles go into the separate circuit for the traction system to keep the motors and inverters at an optimum temperature. The motor and inverter has a water-glycol circuit to cool the stator and the power electronics.
Then the third loop is for the passenger cabins and the heating, ventilation and air conditioning circuit. So, for those three separate circuits, we’ve got intelligent valves and control systems to optimize their performance.
There is also an intelligent controls element in the thermal system. We can intelligently – through our connected car controls – think about where the vehicle is heading. If you’re on the way to a DC fast charge, for example, at a very high power rate, we know what the optimum temperature is and we can pull down the temperature of the battery using the chiller.
It also goes beyond just the thermal system itself. We’ve developed the complete module and battery pack in-house as a mechanical-electrical system, and we produce it in our brand-new Normal, Illinois assembly plant. In addition to the hardware for controls of the battery management system, we also developed the software, the algorithms and the control strategies and linked it all to our connected car platform (also developed ground-up at Rivian). So, we can not only control the functional performance of the battery for optimized life and performance, but we can vary the parameters of the battery management system tailored to individuals and how they use their vehicles, whether that be charging preference or energy throughput. We can tailor how we use the battery to optimize life and efficiency to give you the best performance that we can. So we have really intelligent control of the BMS linked through our connected car platform and how the user will use the vehicle.
Charged: Can you tell us about the design of the battery modules and pack?
Richard Farquhar: If you zoom out, we have what we believe is currently the highest volumetric energy density modules and pack in the world. It’s about 20-25% greater energy density in watt-hours per liter compared to anything on the market today.
What has allowed us to achieve this is the construction of the module. Each module has two layers, each containing 21700 type cylindrical cells. So, we’ve got 15 kWh of energy in each module. There are 9 of those modules in our standard pack, and we have 12 of those in what we call our premium pack of 180 kWh, which gets us over 400 miles of range.
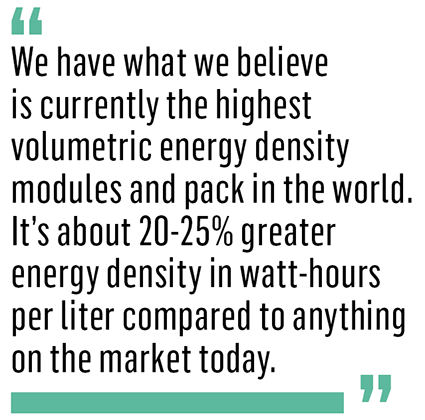
At the heart of the module is a cooling plate between an upper and lower cell layers. That allows us to control the cooling of those cells in their most efficient medium, which is cooling axially. We pull the heat out of the cell through its center, which is the most efficient way to do it as opposed to radially. It allows us to pack those cells really close together. This allows us to get the highest volumetric energy density available today.
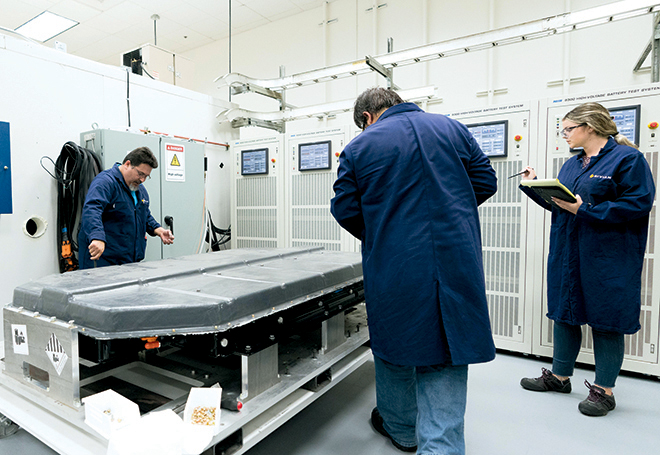
Charged: Are you using a thermally-conductive interface material between the cells?
Richard Farquhar: No, just air. We don’t need to put anything between the cells that are packed together. Their spacing is designed to ensure that, in any scenario you can think of, this module in itself and the pack and the vehicle is as safe as possible. Safety is very much on our agenda.
These are off-road vehicles that can go anywhere with that independent torque control of each wheel. I’ve already had a lot of fun driving in some off-road places. We need to think about those scenarios, when you’re rock crawling, for example, and falling off rocks on a steep descent. We need to protect the pack structurally so it’s very much integrated with our body structures. There is a ballistic shield underneath the bottom of the pack as part of the primary vehicle structure to protect from any ground strike events.
The pack itself is surrounded by an aluminum structure of extrusions to protect it in crash events, whether that’s frontal crash or side-pole crashes. Passive safety is of the highest standard for us and within the pack it’s protected from shocks and vibrations that you get from off-roading for long durations.
Also, the packaging of the pack is designed in such a way that it’s very well protected. For example, in those 9 modules, inside the pack, all the high-voltage, low-voltage and cooling systems are packaged in the spine of the pack right up the vehicle centerline. So it’s as far away from the outside as possible for any crash event. The components are well-protected at the center of the pack. A lot of thought has gone into that integrity from a passive safety crash and an off-road scenario perspective.
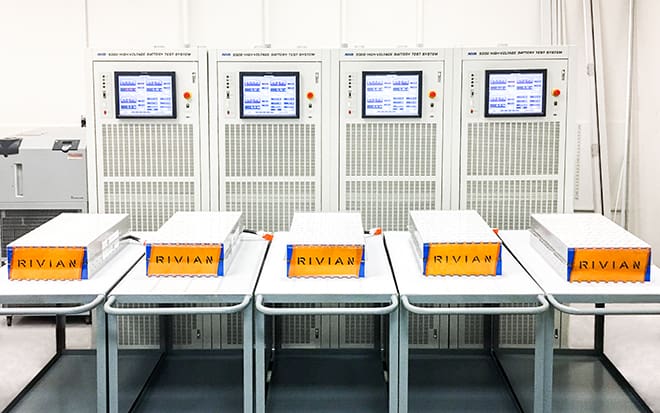
Charged: Rivian has said the vehicles can drive in up to one meter of water. So, all of the drivetrain components would be submerged? Can you talk about the engineering challenges of a submersible system?
Richard Farquhar: Yes, that’s right. One of our big requirements was to be able to drive the vehicle in one meter of water for a period of time. And so, if you sweep through the vehicle from front to rear, everything – our cooling system, our HVAC cooling modules, the battery pack, the drive unit assemblies that I’ve mentioned with electric motors and inverters, they all come into that category of being submersible. And so how they breathe, how they operate, and changes of temperature [from] being submerged in water for a period of time have all been considered as part of our vehicle design. Any deeper and the vehicle will actually start to float – it’s mass itself that prevents it from going any deeper.
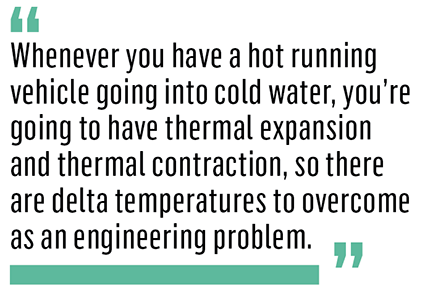
The engineering challenge is really thinking about the laws of physics. Whenever you have a hot running vehicle going into cold water, you’re going to have thermal expansion and thermal contraction, so there are delta temperatures to overcome as an engineering problem. And how things breathe with that change of temperature. Then, obviously, you’ve got to seal things to water through every aperture. Whenever you’ve got a dynamic pressure as well as a static pressure of water, those are parts of the design criteria and test criteria. Venting and drains are really important. It’s definitely provided interesting engineering problems to overcome in our development process.
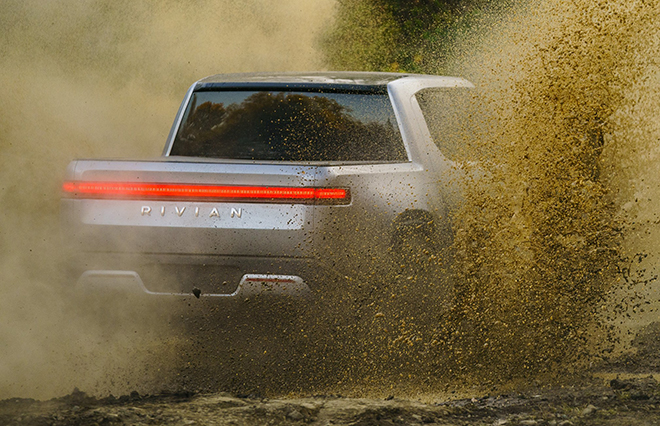
Charged: With the official start of production announced for the end of next year, what stage of the development process are you currently in, and what stages are next? Is there a point at which you will freeze the design, or do you continually manage major design changes through production?
Richard Farquhar: We operate on what we call the RDP, Rivian Development Process, where we very clearly lay out for ourselves a set number of gateways we need to start production. We lay out what deliverables, what milestones we need to achieve by each gateway to be on time. And we worked through four main phases: the concept phase, the development phase, the validation phase and then ramp up into production. We’ve built a number of prototype vehicles, and we’re doing component and systems tests. We use processes within Rivian, which are maturing all the time, to allow what is now well over a thousand people to come together and to deliver these products. So, this is a very defined process with those milestones along the way.
In terms of your point about how we manage design changes, in the early phases we want to maximize attributes of the vehicle. We’ve defined what performance, functions and features we want this vehicle to have. And there’s a lot of creativity, a lot of innovation to achieve those in the most efficient way, whether it be in mass terms, energy terms, cost terms, or other. I guess you could say we move out of that truly creative and innovative phase through the development and validation phases. Then we’re focused on reliability and performance and high quality in the maturation of the product.
We’ve built several test vehicles already. We’re in the teens of development vehicles, and we’re building more prototype vehicles to test more attributes with higher levels of production-ready components. We’re all focused on what we call our validation phase. Here we will build tens of validation vehicles, which are production-intent, to complete all of the validation, reliability, durability testing, and start the certification process to go through the quality maturation for production launch at the end of next year.
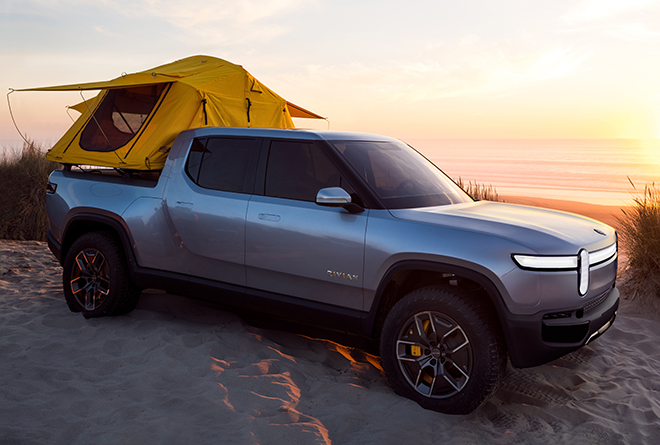
This article appeared in Charged Issue 46 – November/December 2019 – Subscribe now.