In August 2013, KLD Energy announced that it has received official UN and IEC certification for the battery pack solution of its proprietary electric drive system. The announcement marked the end of a five-year development effort and the beginning of high-volume production for the company’s ultra-efficient turnkey oneDRIVE propulsion system.
There are hundreds of different types of electric motors in existence, although only a handful are used for traction applications. This summer KLD Energy Technologies added one more to that short list.
The Austin-based startup is beginning high-volume production of its motor, which has a unique inside-out design – internal stator, external rotor. Unlike other inside-out topologies (like the in-wheel motors made by Protean or Schaeffler, for example), KLD uses a patented “stator block” design. These blocks allow for a modular stator that’s scalable to different power outputs for a broad range of applications.
To use a permanent magnet motor for different power applications, engineers will typically redesign it, changing the stator windings and other components. KLD’s stator blocks are common among all configurations of its motor. To scale the power, you can simply add more blocks – up to six in its first production model, which the company claims will lower cost, increase reliability, and simplify serviceability.
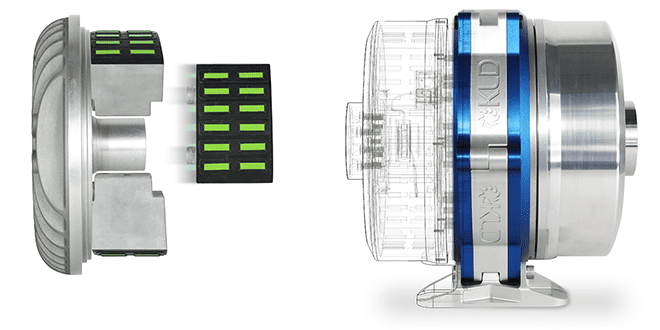
The stator block technology, originally invented by Ray Caamano, KLD’s Chief Science Officer, uses a tape wound core design. While most permanent magnet motors have traditional laminated monolithic stators that are continually wound, KLD’s tape-wound blocks are not magnetically connected to each other. This unique low-inductance feature enables high-speed direct drive at low voltage.
The company claims many advantages for its stator design, including: a reduction in rare-earth magnet content of as much as 60 percent; high-frequency operation in excess of 1,500 Hz, allowing high power density and a larger torque arm radius; direct thermal paths from the stator components out of the motor; low inductance; and very high efficiency.
One system approach
KLD was originally founded in 2008 by CEO Christian Okonsky to commercialize Caamano’s motor design. However, the duo quickly realized that to fully capitalize on the potential of stator block technology, the company would need to build complete drive systems. “Ray was making impressive strides building his own EVs based on this motor technology, but one of the big problems he would run up against was the motor, controller and battery integration,” Okonsky told Charged. “At that point we realized we needed to surround ourselves with experts in those areas as well.”
The company decided to focus on maximizing efficiency with a fully integrated turnkey drivetrain, and the result is its oneDRIVE system, which was officially launched in June 2013.
Battery
The scalable powertrain features 48 V battery modules. With lithium-ion cells supplied by Samsung, the packs have KLD-designed battery management systems that fully integrate with the custom motor controllers, also designed in-house. Because of the unique attributes of the stator block motor technology, KLD was able to make some novel design choices for its pack.
The motor’s extra low-inductance means that KLD can achieve high-speed operation with a low battery pack voltage. One of KLD’s first customers was the electric scooter maker Eclimo. The Malaysian company searched the globe for a direct-drive solution that could achieve 80 kph (about 50 mph) with a battery pack less than 60 V. “To the best of my knowledge, we have the only technology that can achieve that,” said Okonsky. “Many others can achieve it at 72 V or 96 V, but not below 60 V.” Eclimo wanted to have the most energy-efficient solution in the industry. With KLD’s system, it was not a problem.
Because of the high overall efficiency of the system, KLD chose to use power cells, rather than the energy cells that are typically used in automotive applications. Power cells have a lower internal resistance, so they create less heat during cycling and are considered safer, which means no active cooling is necessary. But the trade-off is capacity. “Because we have such an efficient system, we actually wind up with more range, even though we use a power cell,” explained Okonsky. “We don’t need the capacity that most people need for the same application.”

Controller
The hardware in the oneDRIVE motor controller is essentially the same as a typical inverter, but the software is unique to the KLD system. The controller operates at much higher frequencies than conventional controllers to handle the high output regeneration of the motor (another benefit of KLD’s system). It also plays a major role in supporting a multitude of safety and performance vehicle features – Controller Area Network (CAN) bus communication to the BMS, charger and dashboard interface, kickstand safety switch (for motorcycles), reverse operation, etc.
The market
Since receiving the critical UN and IEC certification for its battery pack – which included heavy industrial testing and allows KLD to ship the system via air cargo – oneDRIVE is beginning high-volume production and shipping to customers.
Because the system is scalable, the company sees many different potential applications. For automotive use, the current product line is targeted at vehicles that are 1,000 kg or less, but it can be applied to larger vehicles in the future. “Imagine our motor is a pie, with six stator block pieces,” explained Okonsky. “It’s scalable in that sense. Each stator block has a rough equivalent of about 2 kW of power.”
Two-wheel vehicle designers can use one of those motors, and its inside-out nature lends itself perfectly to in-wheel packaging. For heavier four-wheel vehicles, the KLD system is transmission-free, and has two motors side-by-side, direct drive, with an electronic differential between them.
“Right now we’re focused mainly on the vehicle market, and we’re very excited about it,” said Okonsky. “We started in two-wheel vehicles because the infrastructure involved is much less. Then people began to come to us for the four-wheel vehicles, like Cenntro Motors.”
The Kombi EV, by Cenntro Motors, is a light-duty utility vehicle – designed for maintenance, delivery and light cargo transport – and is built around KLD’s oneDrive. The product is expected to be available later this year, and it claims an impressive 250 MPGe – twice what is available on the market today.
Upping efficiency
Another promising area that KLD is actively exploring is the elevator market. “We’re currently in phase-two testing with Schindler elevators,” Okonsky told us. The Switzerland-based Schindler Group is one of the largest manufacturers of people movers. “They actually approached us and were very interested in our highly-efficient scalable technology.”
For an elevator company, scalability is extremely important. A commodity-grade elevator is 20 stories and below, which accounts for about 90 percent of the world’s elevators. KLD’s drive system can provide the power for a 20-story elevator in a six stator block solution, or for shorter buildings, it can use a motor with fewer stator blocks. “They could use one motor for the entire product line of elevators, and greatly improve serviceability,” said Okonsky.
The two companies are also exploring the use of battery packs to capture regenerated energy during an elevator’s descent. By adding the right size battery pack and regenerative braking for the down cycle, KLD says a system could run off-grid well over 50 percent of the time.
Typically, an elevator company will source a motor from Company A, a motor controller from Company B and a battery from Company C. “We do all of it in one system and offer a whole different strategy,” said Okonsky. “Because we design the entire system, we’re able to achieve regeneration rates that are very high. Higher than anything we’ve seen out there in the industry.”
Global reach
Okonsky was one of the original six engineers in the notebook division at computer maker Dell, so it’s no surprise to learn that KLD has chosen the contract manufacturing model. The company will do all of the pilot production in-house. The engineering team will produce all of the manufacturing documents for fixtures, test equipment, processes, etc, then outsource to contract manufacturers around the world. “We use what’s called a regionalized model,” Okonsky explains. “When we’re selling heavily in the US and Europe, we’ll have US and European suppliers. If we’re going to sell heavily in China, we’ll have regionalized Chinese suppliers and manufacturers. The same with Malaysia, and eventually South America.”
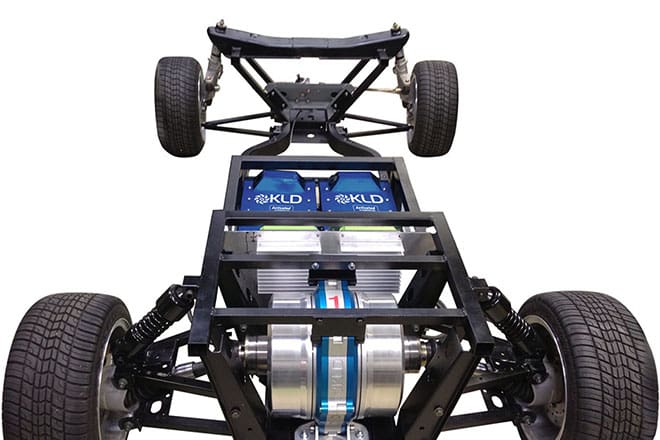
Okonsky describes the response to the oneDRIVE product launch as “frankly overwhelming.” He says that they receive many inquiries every day about the new system. “It’s sort of what we envisioned headed in, the idea that people will come to us and say, ‘We’ve tried to put together a low-voltage high-efficiency motor, controller and battery system, and I’ve got to tell you that it’s not working.’ We knew that they would love to buy a system technology that’s more cost-effective and efficient than buying pieces and trying to integrate them.”
At the moment, KLD is focused on supporting its existing customer base, and expanding the electric vehicle market with its oneDRIVE system. Although the motor technology could be used in many different applications, besides working with Schindler, the company’s main focus is the automotive market.
“My time is mostly taken up by evaluating potential customers and determining whether or not it makes sense to pursue that opportunity or another opportunity,” Okonsky told us. That sounds like a good problem for a fledgling start-up company to have. With any luck, we should hear a lot more about the use of stator block technology in many industries in the coming years.
This article originally appeared in Charged Issue 10 – OCT 2013
