When it comes to EVs, every pound matters. There is a direct relationship between a vehicle’s weight and the requirements of its expensive battery back, so automotive engineers will explore every possible measure to reduce vehicle mass.
However, one of the ways that engineers have traditionally achieved desirable properties in the domain of Noise, Vibration, and Harshness (NVH) is to increase the mass of structural components and body panels. This leaves EV designers with a trade-off between reducing mass and attaining the best NVH characteristics in the vehicle body.
“Mass is good for reducing noise, for quieting vehicles,” explained Matt Murphy, VP of Engineered Solutions at Materials Science Corporation (MSC). “There’s an equation in noise and vibration called the mass law, and it’s for airborne noise, which is the higher-frequency sounds that come through into the cabin. It shows that the thicker the panel, the heavier the panel, the better those sounds will be blocked or damped out.”
MSC is a Michigan-based provider of laminated materials that offers products with a dual focus on lightweighting and NVH optimization, recognizing the trade-off faced by EV designers and striving to eliminate it.
Reducing noise with less
Instead of using thicker steel or aluminum, one alternative solution to damp out airborne noise to is to use add-on treatments such as spray-on deadener or butyl patches. These products are essentially band-aids, and are often found on aluminum panels that don’t weigh enough on their own to provide the necessary NVH characteristics.
“If you take a Tesla, pull the carpet out and get down to the body only, you’re going to see these patches all over the car,” says Murphy. “Those are to damp the aluminum. And they need more of them, and they need thicker ones than they’d need if they used steel, because the aluminum doesn’t have the mass.”
To give auto engineers better options, MSC developed two products called Quiet Steel and Quiet Aluminum, which it says are alternatives to standard body-in-white materials that can eliminate the need for these add-on treatments. Murphy describes the products as a holistic solution for stamped automotive parts in applications with NVH requirements.
Quiet Aluminum
“For example, I have a part that we stamped and tested in our lab,” says Murphy. “It has a 46% weight reduction over the same monolithic aluminum part with a bake-on mastic for NVH. So, you can remove that mastic, save weight and we get improved NVH results.”
In addition to saving mass and improving NVH management, MSC says that Quiet Aluminum offers EV manufacturers another advantage: more packaging space. Add-on treatments take up valuable real estate and ultimately decrease the space available to passengers. For EV-makers wanting to offer the best possible experience for customers, every inch saved makes a difference.
Quiet Aluminum is made of two sheets of monolithic aluminum laminated together with an engineered viscoelastic polymer core. This core, which is about 0.025 mm thick, is chemically tuned to the exact application needed – depending on the placement in the vehicle, the Quiet Aluminum will face different temperatures and frequencies. The chemists at MSC must take these factors into account when designing the core.
“The chemistry is designed to provide the damping at the right operating temperature,” describes Murphy. “When we design the product, the first question we ask the engineers is: where in the vehicle are you going to use this? In an internal combustion engine, you have different levels of heat. You might have an exhaust in one area, or the engine upfront. With EVs it’s different, because they don’t have these typical heat sources. So, we design the core around the operating temperature and the frequencies that are most important in solving their acoustic problem.”
The Quiet Aluminum damps noise by shearing at the micro-level, according to Murphy. “The panels actually move against each other when you impact them. You’ll never see it – we’re talking tiny, tiny amounts, which allow it to damp. This is the key to providing structural damping at the temperature that the application is seeing. So, we select a specific chemistry for the polymer core that has those characteristics.”
A premium on pounds
Because of the benefits of reducing vehicle mass, manufacturers are willing to pay more to lose pounds. For example, one automaker is reported to offer two dollars extra for everyone pound of weight that a solution will save.
This willingness to pay more for less bodes well for Quiet Aluminum, which does cost more than standard aluminum because of the extra steps involved in its production. However, Murphy goes on to describe how this additional upfront cost is offset: “The overall system cost is typically lower, because you’re eliminating these patches, and you’re eliminating all the labor to put them in. When we look at the system, it’s usually equal or lower cost.” The benefits to the overall system explain why manufacturers are willing to pay extra for lightweighting solutions like Quiet Aluminum.
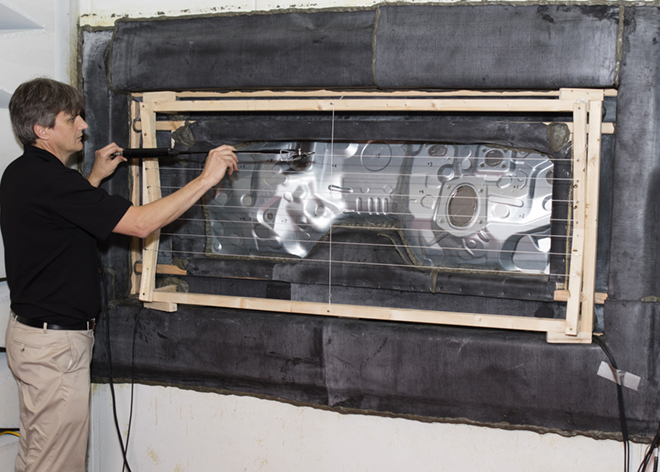
Customized lightweighting
MSC says that is it currently working with EV-builders and gearing up for the release of the first EV designed with Quiet Aluminum, although they can’t tell us which one. Murphy says that the automaker chose to use Quiet Aluminum from the beginning of the design process, before building a single car. “We engineered Quiet Aluminum for their specific applications, and the several body-in-white applications are designed for Quiet Aluminum,” said Murphy.
According to Murphy, the space-saving advantage was one of the main reasons for the choice to use Quiet Aluminum, as the automaker aims to maximize passenger comfort. “They told us they want spaciousness. So we enable them to keep that packaging space to an absolute minimum,” says Murphy. In the same interest of comfort, Quiet Aluminum was picked for its noise-damping capabilities, as it comfortably separates a relaxing passenger from motor and tire noise.
Mainstream auto manufacturers have also been taking advantage of MSC’s technology for years. Quiet Steel has been used in several vehicles, including the new Alfa Romeo Giulia and the Ford F-150.
EV manufacturers looking for customized lightweighting solutions can find them at MSC’s Application Research Center in Canton, Michigan. This facility employs chemists and noise and vibration engineers to develop MSC’s tailored technology.
“Using our technical and NVH testing resources in Canton, we work very closely with all of the automakers developing EVs,” said Murphy. “They provide us with the CAD models of the body-in-white and NVH package, and we perform a predictive mathematical analysis of mass and NVH performance of their baseline system and a system utilizing Quiet Aluminum. We typically break it down into different bandwidths for the frequency range. And usually, it’s a winner for mass reduction and performance.”
With their NVH improvement and weight reduction, these products offer clear advantages to the EV industry. So, keep your eyes – and ears – on the road to check out Quiet Aluminum in action.
This article originally appeared in Charged Issue 31 – May/June 2017 – Subscribe now.