Tuning a vehicle’s aerodynamic features is nothing new. Engineers have been using wind tunnels for decades, and more recently they’ve also employed computational fluid dynamics (CFD) software to reduce drag, minimize noise and increase stability by preventing undesired lift forces.
In the expanding world of EVs, car builders are doubling down on efforts to push drag coefficients to new lows. This is of particular importance to battery-powered vehicles, because every step towards drag reduction directly translates into longer driving ranges and lower requirements for pricey battery capacity. When cruising at highway speeds, the majority of energy a vehicle consumes is used to overcome aerodynamic drag and rolling resistance. And unlike the energy used to accelerate an EV, which can be partially recaptured through regenerative braking, the energy used to fight friction is lost to the atmosphere.
We see clear examples of the importance of drag reduction when automakers create all-electric models of existing vehicle lines, such as the Toyota RAV4 EV, VW e-Golf, Kia Soul EV, etc. For these EV versions, automotive engineers go to great lengths to improve the overall airflow performance of the standard vehicle. They redesign things like the car’s front fascia, headlight lenses, wheel arches, cooling area, tire and wheel combinations, spoilers and underbody.
Saving with simulations
In the old days, all aerodynamic tuning was done in wind tunnels, which was expensive and time-consuming. Car companies would build dozens of physical prototypes to test, tweak the design, and then repeat.
Today, CFD modeling software has replaced the early design stages. “CFD is now used upfront to do most of this vehicle design work,” Stephen Ferguson explained to Charged. Ferguson is Marketing Director at CD-adapco (recently acquired by Siemens), whose simulation tool STAR-CCM+ solves complicated problems involving flow of fluids or solids, heat transfer and stress.
Photo courtesy of DLR German Aerospace Center (CC BY 2.0)
“For the automotive engineer, it’s very quick and easy to change a numerical simulation and shape of a CAD model and rerun the simulation,” said Ferguson. “It’s almost an automated process. So CFD is typically used to do all the design tuning. They’ll work out the best design by examining the results of simulations and improve any features of the airflow that are not idealized. In most cases, car companies still use wind tunnel testing to verify the simulations with physical tests. However, now they do it only at the end of the process, and can build one or two physical production prototypes instead of 20.”
Better models mean better cars
Because computer simulations allow engineers to experiment with significantly more designs at relatively low cost, it allows them to optimize performance for given constraints in a way that would otherwise be impossible to calculate. However, this is only true if the numerical models accurately represent the real world. So, every step a company takes toward creating a more accurate representation of vehicles on the road can have significant payback.
Recently, Professor Gary Page and Research Student David Forbes of Loughborough University took real-world representations to the next level by dynamically coupling together two different simulation tools.
The idea is to combine the simulation of airflow forces around the car with a simulation of how the car’s suspension system and driver inputs will react to those changing forces. They describe the new technique as a dynamic coupling because there is a looped relationship between the aerodynamics acting on the car and the way the car responds.
In other words, the changing airflow forces will change the car’s position, roll and pitch. Once the vehicle’s position is changed slightly, then the airflow environment changes as well. It’s also important to take into account the predictable steering behavior, because a driver will tend to correct while driving and often overshoot the response.
Their new approach was to create a dynamic coupling between the CFD simulation in STAR-CCM+ with vehicle handling and driver models in the math-oriented programming language MATLAB, in order to represent the complete and realistic movement of the vehicle on its suspension system.
The research is also focused on taking into account unsteady events such as crosswinds. As cars become lighter, they become more susceptible to crosswinds, which are extremely difficult to reproduce in a wind tunnel. While simulation software like STAR-CCM+ can offer valuable insight into aerodynamic phenomena that crosswinds can present, they don’t account for the vehicle and driver response.
The new technique was developed as part of the Programme for Simulation Innovation – led by Jaguar Land Rover and the UK’s Engineering and Physical Sciences Research Council.
Dynamic coupling
A lot of research has been done on one-way coupling of STAR-CCM+ and MATLAB – in which the system is open-loop. These simpler methods use a CFD model to calculate aerodynamic forces, feed that data into the MATLAB vehicle handling model, and then call it a day. So, the responses from the handling model are not fed back into the CFD.
The new approach is an attempt to step closer to reality by sending CFD aerodynamic data to the handling model, which then gives back positional data to the CFD at every time step – creating a closed-loop and fully coupled system.
While closed-loop feedbacks are inherently more accurate, they also add complexity and costs. In this research, the direct coupling was achieved with the use of a Java macro to connect STAR-CCM+ to the MATLAB simulation. One considerable advantage of this type of coupling is the ability to run a CFD simulation on a large high-performance computing system while the handling model in MATLAB is run on a local machine.
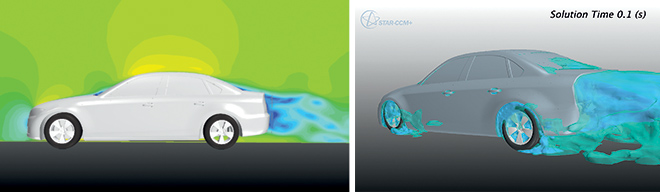
Figure 1: Initial simulations use the full scale DrivAer model.
For the CFD simulation, the DrivAer generic car model CAD geometry was used (Figure 1). Developed at the Institute of Aerodynamics and Fluid Mechanics at the Technical University of Munich, the model is full-scale, includes rotating wheels, and has about 20 million hexahedral cells (Figure 2).
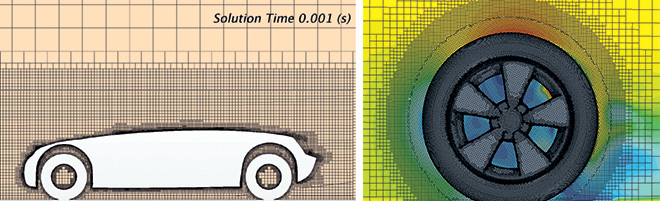
Figure 2: Dynamic overset meshing allows the motion of solid components within the fluid domain.
The MATLAB handling model was designed at Loughborough University for the university’s 6-degrees-of-freedom (DoF), Stewart-type platform driving simulator. It is a comprehensive and realistic dynamics model that includes the full suspension system and driver’s response.
Passing maneuvers
The typical commute rarely consists of an open road with a straight-on headwind. In reality, cars on the highway experience a very complex system of aerodynamic forces, including those exerted by other cars. When you pass a big truck on the highway, for example, you can feel the influence on your vehicle’s steering, because the airflow around the car is interacting with the airflow around the truck.
When subjected to a crosswind excitation, the vehicle’s resonant frequencies may cause the driver to respond and either alleviate or aggravate the vehicle’s response. One of the aims of this research is to identify the frequencies at which this happens, in order to improve a vehicle’s crosswind stability.
How does that interaction affect the overall drag coefficient? Is there a better way to design the suspension and controls to minimize any negative affects?
Forbes’s and Page’s research was meant to demonstrate how a fully coupled comprehensive and realistic ground vehicle simulation could be achieved. Because the numerical model of how a vehicle’s suspension systems will respond is specific to each vehicle, it’s up to the automakers to build their own comprehensive simulations.
“We recognize that difficult engineering problems are not a function of just aerodynamics or just structural dynamics,” explained Ferguson. “They tend to involve multiple physics. So that’s why we made it easy to interface to STAR-CCM+, so you can connect it to MATLAB and other tools. The MATLAB portion of this type of dynamic coupling will come from the car company, because it’s a proprietary model developed to describe their car. In principle, any car company could do this, but I don’t think many are. It’s groundbreaking research work with big implications.”
This article originally appeared in Charged Issue 25 – May/June 2016. Subscribe now.