California Lithium Battery took advantage of national and local government programs so it could focus on its revolutionary silicon-graphene anode material. Now with EV, electronics, and energy storage customers lining up, it hopes to break the battery bottleneck.
When you think about a bottleneck, you think about constriction – something that moves in a particular direction and runs into a tightening of available space. In the case of traffic, the bottleneck that brings us all together in frustration and occasional road rage, you alleviate it by adding layers – new lanes to accommodate the progress of vehicles.
There is another kind bottleneck affecting the future of our roadways as well. Unfortunately, for the bottleneck of electric vehicle battery capacity and energy density, there is no left lane opening up just ahead. Our only real solace in this waiting game is knowing that construction is in progress. Yet just as with traffic, alleviating the battery bottleneck will mean adding new layers of complexity to the workspace: new battery chemistries and technologies, new working relationships, new infrastructures.
California Lithium Battery (also known as CalBattery) exemplifies the kind of interrelationships and operating structures needed to fuel the battery powder keg that seems set to explode in a few years’ time. The small startup has thrived on the partnership of government with private enterprise, the teaming of business manager with scientist, and most importantly, the fusion of silicon with graphene to produce a highly energy-dense anode material.

Savvy Startup
If CalBattery accomplishes its current goal of changing the battery game by commercializing the silicon-based battery anode – specifically, its patent-pending silicon-graphene (SiGr) composite anode material – it will be partially because of a US Department of Energy (DOE) technology transfer program. In 2011, the DOE held its first “America’s Next Top Energy Innovator Challenge.” Reality-show reject name aside, the program specifically targets small American startup companies and gives them a chance to license unused patents from the DOE’s national laboratories at bargain-basement prices.
In 2009, CalBattery co-founder and CEO Phillip Roberts was leading Ionex Energy Storage Systems, working on grid-scale energy storage systems for renewable-energy integration in California, when he was approached by Argonne National Laboratory (ANL), the oldest of the DOE’s national research labs. “I was speaking at an energy storage conference,” Roberts said, “and one of the Argonne reps came up to me and asked ‘how would you like to lower the cost of your lithium battery by 70 percent?’ I started laughing. I said, ‘Yeah, sure, where do I sign up?’”
While it may have sounded too good to be true at first, the Argonne team, led by the new material’s inventor Dr. Junbing Yang, later convinced Roberts that its SiGr composite anode material had great promise. In ANL tests, it showed the potential to dramatically improve Li-ion battery performance, as well as lowering the average cost per kWh. Within two years, Roberts and his business partner Wei Cui had spun off CalBattery as a joint venture and, through the DOE’s America’s Next Top Innovator/Startup America initiative, begun working with Argonne to fast-track the development and commercialization of this new high-capacity SiGr battery technology.
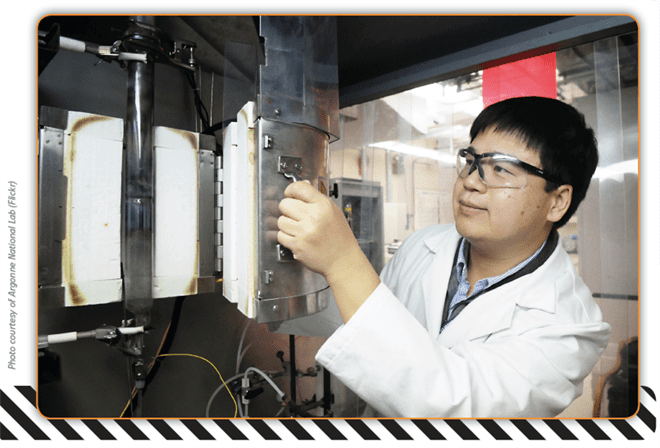
During that time, CalBattery settled down in the newly-opened LA Cleantech Incubator (LACI) in the “Cleantech Corridor” near downtown Los Angeles – ironically, not in Silicon Valley. LACI began in 2011 with major funding from the City of LA and the LA Department of Water and Power. The facility offers deeply discounted office and lab space, executive mentorship, and a network of potential customers and financiers.
Thanks in part to the slow-burn environment that LACI provides, CalBattery spent a quiet 2011-2012 working behind the scenes with Argonne under a Work for Others agreement, eventually leading up to CalBattery’s official licensing of the SiGr composite anode from ANL in November 2012. The company’s plan was to rapidly commercialize the material, but even with the license secured, not all the pieces were in place yet.
“When you get a license, unfortunately they don’t give you an instruction manual,” Roberts said. “It’s just kind of a general idea in which direction to head. The real work to get to a product, that’s a whole new challenge.”
Roberts needed a partner to scale up the SiGr production to commercial levels, and who better than the inventor himself? Junbing Yang, Ph.D. had been with Argonne since 2004, had a strong background in R&D on high-energy and high-power lithium-ion batteries, and is credited with inventing the ANL silicon-graphene composite anode material that CalBattery had just licensed. For about a year, as CalBattery worked with Argonne, Yang continued to optimize the process of producing SiGr. However, he had zero executive or startup experience.
“It’s a big change to go from the research side to an early-stage startup. I had to make a decision,” Yang said. “But I’m not interested in just being the first person to publish the research. I want to see the research go into a commercial product.”
This past June, Yang joined CalBattery as Chief Technology Officer in charge of new product intellectual property (IP) and development. “To go from scientist to entrepreneur, it’s a lifestyle change,” Yang said. “Here, in this early-stage environment, you do everything by yourself, very quickly, and economically efficient. It’s totally different. It’s an evolving story. Maybe after six months, I’ll have more personal feelings for this change in myself.”
Roberts then chimed in, saying, “He’ll certainly have more gray hair; this is my third startup and I have plenty of gray hair to prove it!”
With Yang and the rest of the executive team in place at the LACI headquarters, CalBattery opened a pilot production facility 30 miles down State Route 60 in Brea. Now it’s full-speed ahead with scaling up production, and CalBattery thinks that in a few of years it can churn out SiGr on a commercial scale.
Metal-Mineral Fusion
Beyond CalBattery’s startup backstory, there’s also the saga of its keystone, the silicon-graphene composite. “Silicon has been kind of the Holy Grail of battery research for about 10-15 years,” Roberts said. “It’s such a big deal because silicon absorbs lithium 10 times better than any other material. The key is to have it work in a stabilized manner for extended cycle life. The problem is that during lithiation (charge/discharge cycle), it expands to over 400 times its size, and when it discharges, it goes back down. If you put it into an electrode in a battery, it’ll break the contact and lose its capacity in less than 10 cycles.”
Yang found a composite production process that works around the limitation of silicon’s expansion. It’s a gas phase deposition process that uses organosilane heated up to a gas. The sub-micron-size particles form between crevices in the graphene layers and uniformly embed themselves throughout these platelet layers, creating a stable silicon-based anode composite material that maintains its structural integrity for long cycle life, for use not only in EVs but also in consumer portable device applications. “You can’t just mix them up,” Roberts said. “We tried it; it didn’t work. To coat it doesn’t work. The only way it works is to put it in as a gas.”
“The silicon gas goes everywhere, and then it decomposes to form solid particles,” Yang added. “That’s how you form this embedded structure.” The resulting composite allows silicon to expand and contract, but not so much that it breaks the battery electrode contact.
Because a silicon-based anode holds so much promise for lithium batteries, many other companies and entities are trying to find new methods to stabilize silicon as well, but Yang feels that the Calbattery method is the best so far. “To stabilize silicon, you want the silicon to be intermittently mixed with graphene,” Yang said. “The silicon must not agglomerate to produce a material with the best performance and longest cycle life. The way other researchers or companies incorporate silicon into graphite is different. They basically have silicon loosely sitting on the surface of the graphite, which does not help, because during cycling the silicon particles migrate and then agglomerate, causing rapid capacity fading. I tested many other silicon procedures. We know ours is the best, because we tested the materials with the same procedure, so we can make an apples-to-apples comparison.”
Roberts claims that the result is a stable anode material with three times the specific capacity of any other, and that it’s closer to being commercial-ready than any other silicon-based solution. “It has triple the capacity to absorb lithium ions,” Roberts said, “and when you combine it with other high-energy-density cathode and high-voltage electrolyte materials that CalBattery is currently developing, you can double or triple the energy density. We tested it with some of the best battery cathodes and electrolytes, and it worked very well with all of them. Then we were confident enough to go to the next step to put in the effort and resources to rapidly commercialize it.”
Scaling Up
With the entire industrialized world starving for a breakthrough in lithium battery capacity, CalBattery has attracted more attention than Roberts initially expected. Roberts told Charged that they have interest from many major EV and lithium battery OEMs – as was evidenced by the long lines waiting to speak with Calbattery at a recent industry show in Detroit. With the dream of smartphones and laptops that last 24 hours in everyone’s mind, CalBattery has revised its initial business strategy and is now targeting consumer electronics as the first application for SiGr-based batteries, followed by electric vehicles, and finally stationary energy storage applications.
“With EV batteries, the commercialization process takes five to seven years,” Roberts said. “You first have to develop the cell, then the pack, test them in the field, and there are OEM liability issues that slow the market entry process down even further.”
How much longer? CalBattery is currently perfecting and scaling up the SiGr production process, including building its 3rd-generation reactor for continuous-flow production, and developing low-cost manufacturing techniques. Both Roberts and Yang think that in a few years they will be able to start selling a finished product to key customers, and begin selling the material on a grand scale (many thousands of metric tons) in four years or so, depending on capital resources. Yang said that using a commercial-scale reactor, they could produce fifty metric tons of SiGr material per reactor, per year, and eventually more as their process understanding and global demand grow. “We do not think it’s a problem to scale up,” Yang said, “because for this process we can use existing equipment borrowed from another industry. What we did was modify the reactor.”
The company has supplied SiGr samples to certain customers, who are already looking to develop their next-generation SiGr batteries with them. While CalBattery says that SiGr works with existing cathodes and electrolytes, the company is also working on its own SiGr-optimized cathode and electrolyte materials to use in full cells for EVs and cell phones. The Company is currently being sponsored by a global industrial giant to build and demonstrate an 800 Wh/l cell phone battery in Q1, 2014. Most of the prospective Calbattery OEM customers have already developed their own cathodes and electrolytes and are just looking for a high-capacity yet stable silicon anode material. The bottom line for Roberts is that SiGr can be used as a drop-in replacement for current graphite-based anodes. And with a Who’s Who in both the EV and lithium battery worlds waiting in line to incorporate the Calbattery silicon anode material into their next-generation EV and cell phone batteries, he thinks the company can capture 10-25 percent of the estimated $6 billion LIB anode market by 2020.
“If it’s not the Holy Grail, it’s one of the keys to substantially improving the next generation of lithium batteries without a doubt,” Roberts said. “From my experience it’s what everybody’s been looking for, and I would say it’s the most promising lithium battery material entering the market today. A lot of people talk about lithium-air or sulfur, and while it’s exciting, that’s a long time down the road to a commercial product, if ever. This anode product is designed as a drop-in replacement for graphite, and it’s going to improve anything and everything that needs to store energy practically and cost-efficiently. It not only pays for itself, it is fundamental to making high energy-density lithium batteries possible in the very near future. That’s why we think it’s going to be a game-changer – making the cost of EVs on par with gas vehicles, tying renewables together with low-cost grid energy storage and – my daughter Jasmine’s favorite – making it possible to use a smart phone for twice as long on a single charge. It’s a potentially disruptive technology that could transform a lot in our society for the better.”
This article originally appeared in Charged Issue 11 – DEC 2013
